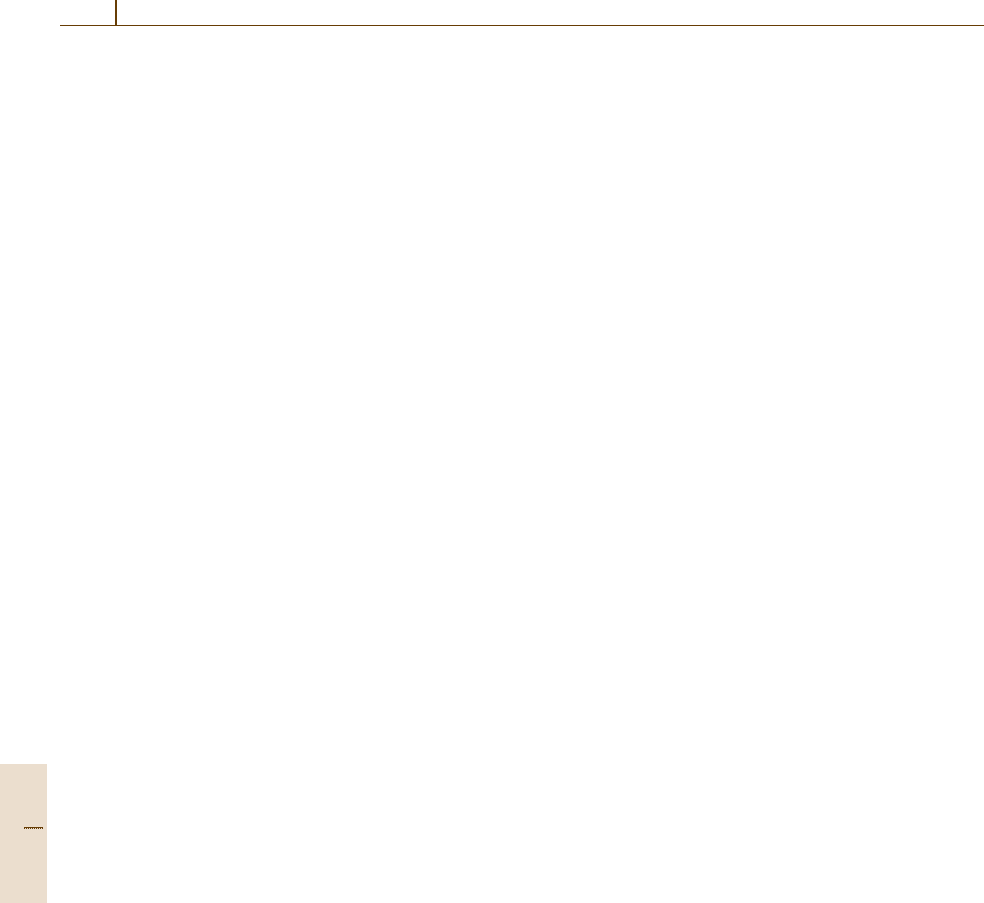
928 Part F Industrial Automation
The semiconductor fabrication technique is a ma-
tured top-down method, which has been used in the fab-
rication of microelectromechanical systems (MEMS).
However, it is difficult to build nanostructures using this
method due to limitations of the traditional lithogra-
phy. Although smaller features can be made by electron
beam nanolithography, it is practically very difficult
to position the feature precisely using e-Beam nano-
lithography. The high cost of the scanning electron
microscopy (SEM), ultrahigh vacuum condition, and
space limitation inside the SEM vacuum capsule also
impede its wide application.
Atomic force microscopy (AFM) [53.1] has proven
to be a powerful technique to study sample surfaces
downto the nanoscale. It can work with both conductive
and insulating materials and in many conditions, such
as air and liquid. Not only can it characterize sample
surfaces, it can also modify them through nanolithog-
raphy [53.2, 3] and nanomanipulation [53.3, 4], which
is a promising nanofabrication technique that combines
top-down and bottom-up advantages. In recent years,
many kinds of AFM-based nanolithographies have been
implemented on a variety of surfaces such as semicon-
ductors, metals, andsoft materials [53.5–8].A variety of
AFM-based nanomanipulation schemes have been de-
veloped to position and manipulate nanoobjects [53.9–
13]. However, nanolithography itself can hardly be
considered as sufficient for fabrication of a com-
plete device. Thus, manipulation of nanoobjects has
to be involved in order to manufacture nanostructures
and nanodevices. The AFM-based nanomanipulation is
much more complicated and difficult than the AFM-
based nanolithography because nanoobjects have to be
manipulated from one place to another by the AFM tip,
and sometimes it is necessary to relocate the nanoob-
jects during nanomanipulation while nanolithography
can only draw patterns. Since the AFM tip as the ma-
nipulation end-effector can only apply a point force on
a nanoobject, the pushing point on the nanoobject has
to be precisely controlled in order to manipulate the
nanoobjects to their desired positions. In the most re-
cently available AFM-based manipulation methods, the
manipulation paths are obtained either manually using
haptic devices [53.9, 10] or in an interactive way be-
tween theusers and the atomic force microscope (AFM)
images [53.11,12]. The main problem of these schemes
is their lack of real-time visual feedback, so an aug-
mented reality interface has been developed [53.14,15].
But positioning errors due to deformation of the can-
tilever and random drift such as thermal drift cause
the nanoobjects to be easily lost or manipulated to
wrong places during manipulation; the result of each
operation has to be verified by a new image scan
before the next operation starts. This scan-design-
manipulation-scan cycle is usually time consuming and
inefficient.
In order to increase the efficiency and accuracy
of AFM-based nanoassembly, automated CAD guided
nanoassembly is desirable [53.16]. In the macroworld,
CAD guided automated manufacturing has been widely
studied [53.17]. However, it is not a trivial extension
from the macroworld to the nanoworld. In the nanoenvi-
ronments, the nanoobjects,which includenanoparticles,
nanowires, nanotubes, etc., are usually distributed on
a substrate randomly. Therefore, the nanoenvironment
and the available nanoobjects have to be modeled
in order to design a feasible nanostructure. Because
manipulation of nanoparticles only requires transla-
tion, while manipulation of other nanoobjects such as
nanowires involve both translation and rotation, manip-
ulation of nanowires is more challenging than that of
nanoparticles. To generate a feasible path to manipulate
nanoobjects, obstacle avoidance must also be consid-
ered. Turns around obstacles should also be avoided
since they may cause the failure of the manipulation.
Because of the positioning errors due to the random
drift, the actual position of each nanoobject must be
identified before each operation.
Beside, the deformation of the cantilever caused by
manipulation force is one of the most major nonlineari-
ties and uncertainties. It causes difficulties in accurately
controlling the tip position, and results in missing the
position of the object. The softness of the conventional
cantilevers also causes the failure of manipulation of
sticky nanoobjects because the tip can easily slip over
the nanoobjects. An active atomic force microscopy
probe is used as an adaptable end effector to solve these
problems by actively controlling the cantilever’s flex-
ibility or rigidity during nanomanipulation. Thus, the
adaptable end effector is controlled to maintain straight
shape during manipulation [53.18].
Apart from nanoassembly, manufacturing process
of nanodevices is important. Carbon nanotube (CNT
)
has been investigated as one of the most promising can-
didates to be used for making different nanodevices.
CNTs have been shown to exhibit remarkable electronic
properties, such as ballistic transport and semiconduct-
ing behavior, which depend on their diameters and
chiralities. Recently, it was demonstrated that CNTs
can be used to build various types of devices such as
nanotransistors [53.19], logic devices [53.20], infrared
detectors [53.21, 22], light emitting devices [53.23],
Part F 53.1