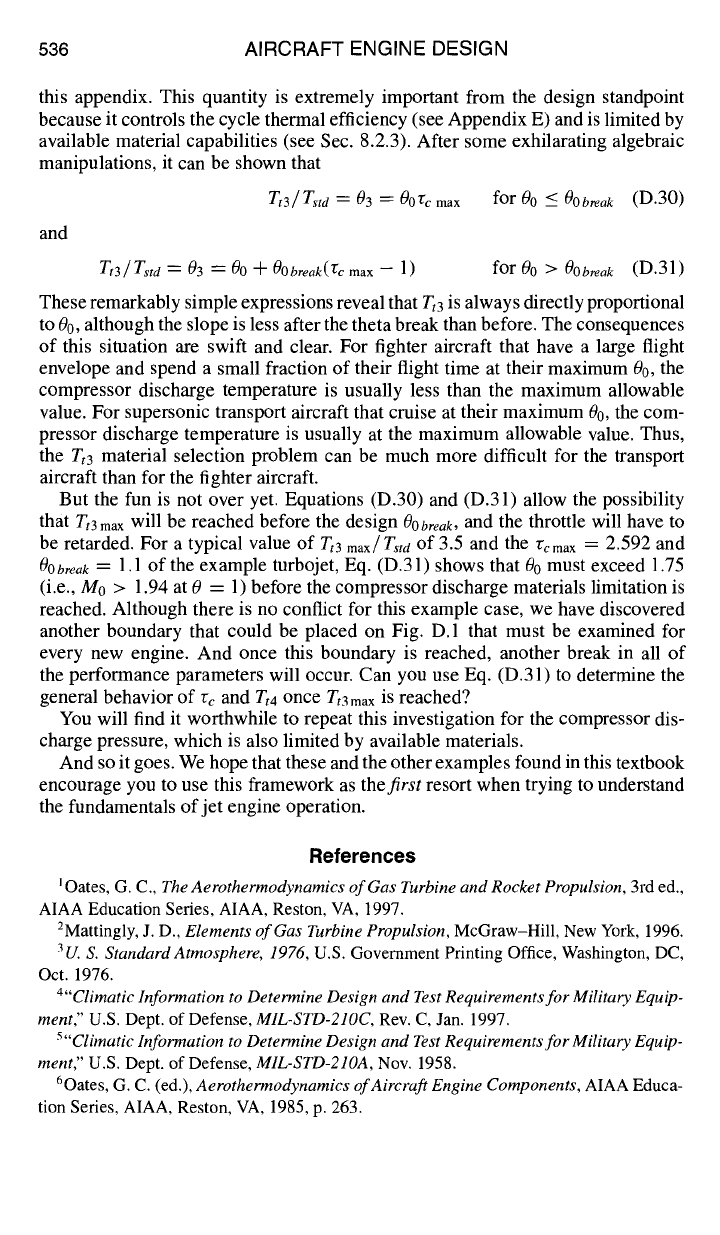
536 AIRCRAFT ENGINE DESIGN
this appendix. This quantity is extremely important from the design standpoint
because it controls the cycle thermal efficiency (see Appendix E) and is limited by
available material capabilities (see Sec. 8.2.3). After some exhilarating algebraic
manipulations, it can be shown that
Tt3/Tstd=03
u~-00Tcmax for00 _< 00bre,k (D.30)
and
Tt3/Tstd = 03 = O0 ~-OObreak(Tc max -- l) for 00 > 00break (D.31)
These remarkably simple expressions reveal that Tt3 is always directly proportional
to 0o, although the slope is less after the theta break than before. The consequences
of this situation are swift and clear. For fighter aircraft that have a large flight
envelope and spend a small fraction of their flight time at their maximum 00, the
compressor discharge temperature is usually less than the maximum allowable
value. For supersonic transport aircraft that cruise at their maximum 00, the com-
pressor discharge temperature is usually at the maximum allowable value. Thus,
the
Tt3
material selection problem can be much more difficult for the transport
aircraft than for the fighter aircraft.
But the fun is not over yet. Equations (D.30) and (D.31) allow the possibility
that T,3
max
will be reached before the design O0break, and the throttle will have to
be retarded. For a typical value of Tt3 max/T~ta of 3.5 and the rcmax = 2.592 and
OObreak
-~-
l. 1 of the example turbojet, Eq. (D.31) shows that 00 must exceed 1.75
(i.e., M0 > 1.94 at 0 = 1) before the compressor discharge materials limitation is
reached. Although there is no conflict for this example case, we have discovered
another boundary that could be placed on Fig. D.1 that must be examined for
every new engine. And once this boundary is reached, another break in all of
the performance parameters will occur. Can you use Eq. (D.31) to determine the
general behavior of r~ and Tt4
once
Tt3
max
is reached?
You will find it worthwhile to repeat this investigation for the compressor dis-
charge pressure, which is also limited by available materials.
And so it goes. We hope that these and the other examples found in this textbook
encourage you to use this framework as thefirst resort when trying to understand
the fundamentals of jet engine operation.
References
J Oates, G. C., The Aerothermodynamics of Gas Turbine and Rocket Propulsion, 3rd ed.,
AIAA Education Series, AIAA, Reston, VA, 1997.
2Mattingly, J. D., Elements of Gas Turbine Propulsion, McGraw-Hill, New York, 1996.
3U. S. Standard Atmosphere, 1976, U.S. Government Printing Office, Washington, DC,
Oct. 1976.
4"Climatic Information to Determine Design and Test Requirements for Military Equip-
ment," U.S. Dept. of Defense, M1L-STD-210C, Rev. C, Jan. 1997.
s,,Climatic Information to Determine Design and Test Requirements for Military Equip-
ment," U.S. Dept. of Defense, M1L-STD-21OA, Nov. 1958.
6Oates, G. C. (ed.), Aerothermodynamics of Aircraft Engine Components, AIAA Educa-
tion Series, AIAA, Reston, VA, 1985, p. 263.