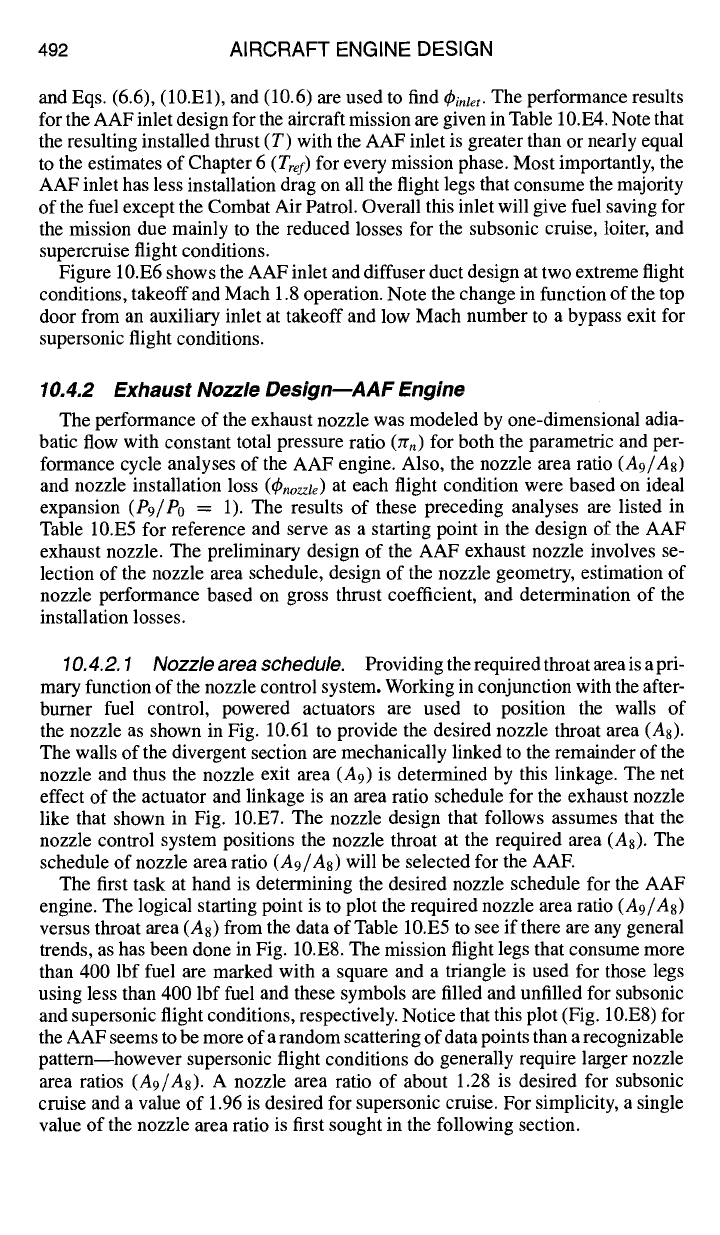
492 AIRCRAFT ENGINE DESIGN
and Eqs. (6.6), (10.El), and (10.6) are used to find
~inlet.
The performance results
for the AAF inlet design for the aircraft mission are given in Table 10.E4. Note that
the resulting installed thrust (T) with the AAF inlet is greater than or nearly equal
to the estimates of Chapter 6
(Trey)
for every mission phase. Most importantly, the
AAF inlet has less installation drag on all the flight legs that consume the majority
of the fuel except the Combat Air Patrol. Overall this inlet will give fuel saving for
the mission due mainly to the reduced losses for the subsonic cruise, loiter, and
supercruise flight conditions.
Figure 10.E6 shows the AAF inlet and diffuser duct design at two extreme flight
conditions, takeoff and Mach 1.8 operation. Note the change in function of the top
door from an auxiliary inlet at takeoff and low Mach number to a bypass exit for
supersonic flight conditions.
10.4.2 Exhaust Nozzle Design--AAF Engine
The performance of the exhaust nozzle was modeled by one-dimensional adia-
batic flow with constant total pressure ratio (zrn) for both the parametric and per-
formance cycle analyses of the AAF engine. Also, the nozzle area ratio (A9/A8)
and nozzle installation loss (q~nozzte) at each flight condition were based on ideal
expansion (P9/Po = 1). The results of these preceding analyses are listed in
Table 10.E5 for reference and serve as a starting point in the design of the AAF
exhaust nozzle. The preliminary design of the AAF exhaust nozzle involves se-
lection of the nozzle area schedule, design of the nozzle geometry, estimation of
nozzle performance based on gross thrust coefficient, and determination of the
installation losses.
10.4.2.1 Nozzle area schedule. Providing the required throat area is a pri-
mary function of the nozzle control system. Working in conjunction with the after-
burner fuel control, powered actuators are used to position the walls of
the nozzle as shown in Fig. 10.61 to provide the desired nozzle throat area (A8).
The walls of the divergent section are mechanically linked to the remainder of the
nozzle and thus the nozzle exit
area (A9)
is determined by this linkage. The net
effect of the actuator and linkage is an area ratio schedule for the exhaust nozzle
like that shown in Fig. 10.E7. The nozzle design that follows assumes that the
nozzle control system positions the nozzle throat at the required area (As). The
schedule of nozzle area ratio (A9/A8) will be selected for the AAE
The first task at hand is determining the desired nozzle schedule for the AAF
engine. The logical starting point is to plot the required nozzle area ratio (Ag/As)
versus throat area (A8) from the data of Table 10.E5 to see if there are any general
trends, as has been done in Fig. 10.ES. The mission flight legs that consume more
than 400 lbf fuel are marked with a square and a triangle is used for those legs
using less than 400 lbf fuel and these symbols are filled and unfilled for subsonic
and supersonic flight conditions, respectively. Notice that this plot (Fig. 10.E8) for
the AAF seems to be more of a random scattering of data points than a recognizable
pattern--however supersonic flight conditions do generally require larger nozzle
area ratios (A9/A8). A nozzle area ratio of about 1.28 is desired for subsonic
cruise and a value of 1.96 is desired for supersonic cruise. For simplicity, a single
value of the nozzle area ratio is first sought in the following section.