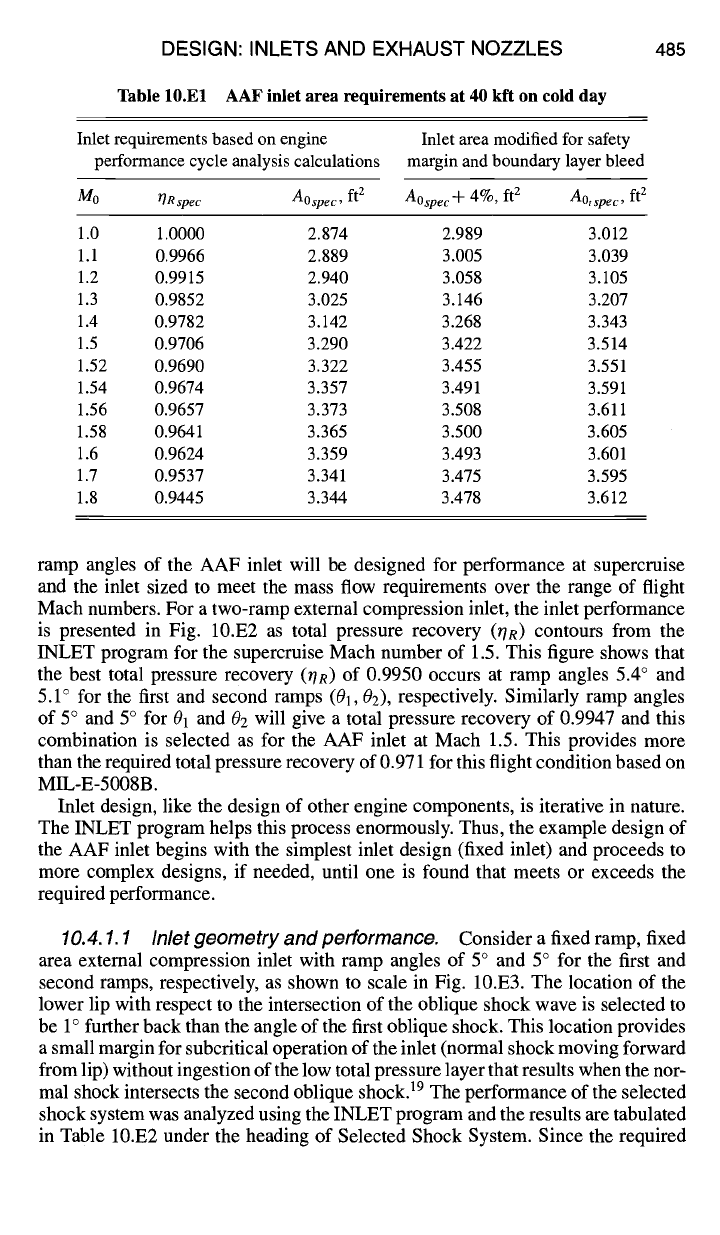
DESIGN: INLETS AND EXHAUST NOZZLES
Table 10.El AAF inlet area requirements at 40 kft on cold day
485
Inlet requirements based on engine
performance cycle analysis calculations
Inlet area modified for safety
margin and boundary layer bleed
mo ORspec
Aospec,
ft2
Aospec +
4%,
ft 2
Aotspec,
ft2
1.0 1.0000 2.874 2.989 3.012
1.1 0.9966 2.889 3.005 3.039
1.2 0.9915 2.940 3.058 3.105
1.3 0.9852 3.025 3.146 3.207
1.4 0.9782 3.142 3.268 3.343
1.5 0.9706 3.290 3.422 3.514
1.52 0.9690 3.322 3.455 3.551
1.54 0.9674 3.357 3.491 3.591
1.56 0.9657 3.373 3.508 3.611
1.58 0.9641 3.365 3.500 3.605
1.6 0.9624 3.359 3.493 3.601
1.7 0.9537 3.341 3.475 3.595
1.8 0.9445 3.344 3.478 3.612
ramp angles of the AAF inlet will be designed for performance at supercruise
and the inlet sized to meet the mass flow requirements over the range of flight
Mach numbers. For a two-ramp external compression inlet, the inlet performance
is presented in Fig. 10.E2 as total pressure recovery (OR) contours from the
INLET program for the supercruise Mach number of 1.5. This figure shows that
the best total pressure recovery (OR) of 0.9950 occurs at ramp angles 5.4 ° and
5.1 ° for the first and second ramps
(01, Oz),
respectively. Similarly ramp angles
of 5 ° and 5 ° for 01 and 02 will give a total pressure recovery of 0.9947 and this
combination is selected as for the AAF inlet at Mach 1.5. This provides more
than the required total pressure recovery of 0.971 for this flight condition based on
MIL-E-5008B.
Inlet design, like the design of other engine components, is iterative in nature.
The INLET program helps this process enormously. Thus, the example design of
the AAF inlet begins with the simplest inlet design (fixed inlet) and proceeds to
more complex designs, if needed, until one is found that meets or exceeds the
required performance.
10.4.1.1 Inlet geometry and performance.
Consider a fixed ramp, fixed
area external compression inlet with ramp angles of 5 ° and 5 ° for the first and
second ramps, respectively, as shown to scale in Fig. 10.E3. The location of the
lower lip with respect to the intersection of the oblique shock wave is selected to
be 1 ° further back than the angle of the first oblique shock. This location provides
a small margin for subcritical operation of the inlet (normal shock moving forward
from lip) without ingestion of the low total pressure layer that results when the nor-
mal shock intersects the second oblique shock) 9 The performance of the selected
shock system was analyzed using the INLET program and the results are tabulated
in Table 10.E2 under the heading of Selected Shock System. Since the required