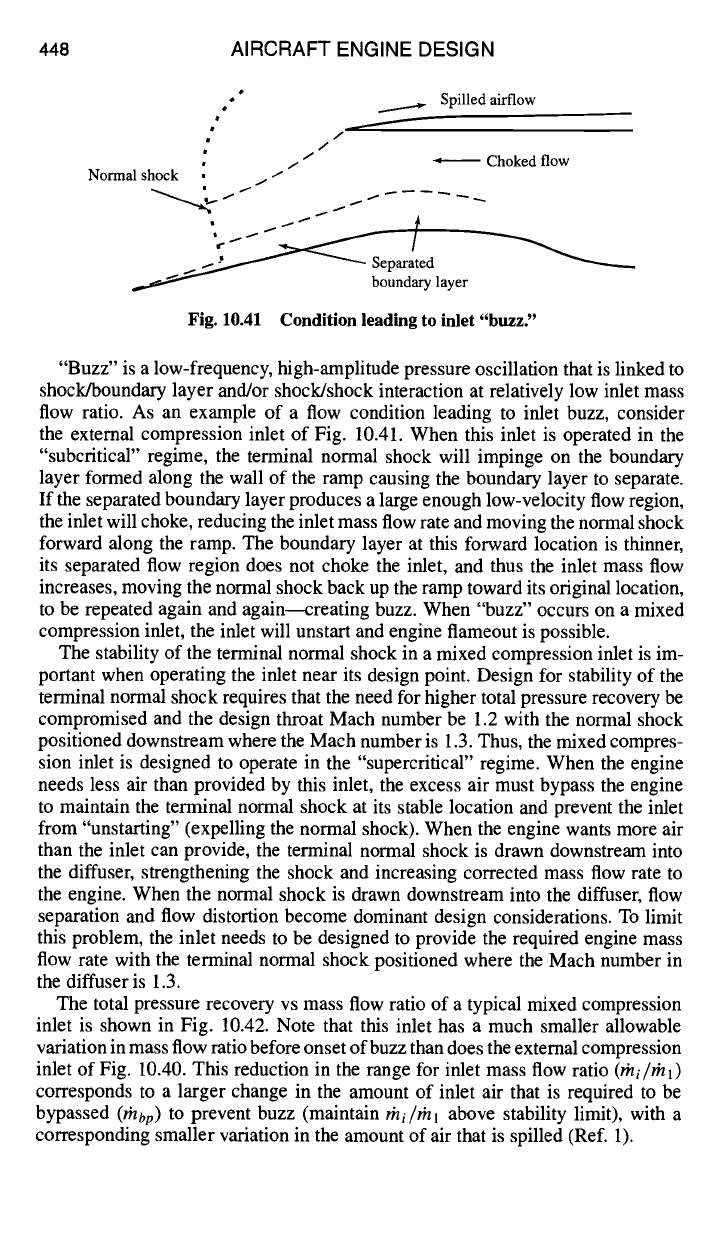
448 AIRCRAFT ENGINE DESIGN
,* ~ Spilled airflow
•
_..._._----
°
• f
J
• / • Choked flow
• J
Normal shock , ..- .t
....~ ~ Separated
boundary layer
Fig. 10.41 Condition leading to inlet "buzz"
"Buzz" is a low-frequency, high-amplitude pressure oscillation that is linked to
shock/boundary layer and/or shock/shock interaction at relatively low inlet mass
flow ratio. As an example of a flow condition leading to inlet buzz, consider
the external compression inlet of Fig. 10.41. When this inlet is operated in the
"subcriticar' regime, the terminal normal shock will impinge on the boundary
layer formed along the wall of the ramp causing the boundary layer to separate.
If the separated boundary layer produces a large enough low-velocity flow region,
the inlet will choke, reducing the inlet mass flow rate and moving the normal shock
forward along the ramp. The boundary layer at this forward location is thinner,
its separated flow region does not choke the inlet, and thus the inlet mass flow
increases, moving the normal shock back up the ramp toward its original location,
to be repeated again and again--creating buzz. When "buzz" occurs on a mixed
compression inlet, the inlet will unstart and engine flameout is possible.
The stability of the terminal normal shock in a mixed compression inlet is im-
portant when operating the inlet near its design point. Design for stability of the
terminal normal shock requires that the need for higher total pressure recovery be
compromised and the design throat Mach number be 1.2 with the normal shock
positioned downstream where the Mach number is 1.3. Thus, the mixed compres-
sion inlet is designed to operate in the "supercritical" regime. When the engine
needs less air than provided by this inlet, the excess air must bypass the engine
to maintain the terminal normal shock at its stable location and prevent the inlet
from "unstarting" (expelling the normal shock). When the engine wants more air
than the inlet can provide, the terminal normal shock is drawn downstream into
the diffuser, strengthening the shock and increasing corrected mass flow rate to
the engine. When the normal shock is drawn downstream into the diffuser, flow
separation and flow distortion become dominant design considerations. To limit
this problem, the inlet needs to be designed to provide the required engine mass
flow rate with the terminal normal shock positioned where the Mach number in
the diffuser is 1.3.
The total pressure recovery vs mass flow ratio of a typical mixed compression
inlet is shown in Fig. 10.42. Note that this inlet has a much smaller allowable
variation in mass flow ratio before onset of buzz than does the external compression
inlet of Fig. 10.40. This reduction in the range for inlet mass flow ratio
(rhi/rhl)
corresponds to a larger change in the amount of inlet air that is required to be
bypassed
(r~lbp)
to prevent buzz (maintain
#/i//#/1
above stability limit), with a
corresponding smaller variation in the amount of air that is spilled (Ref. 1).