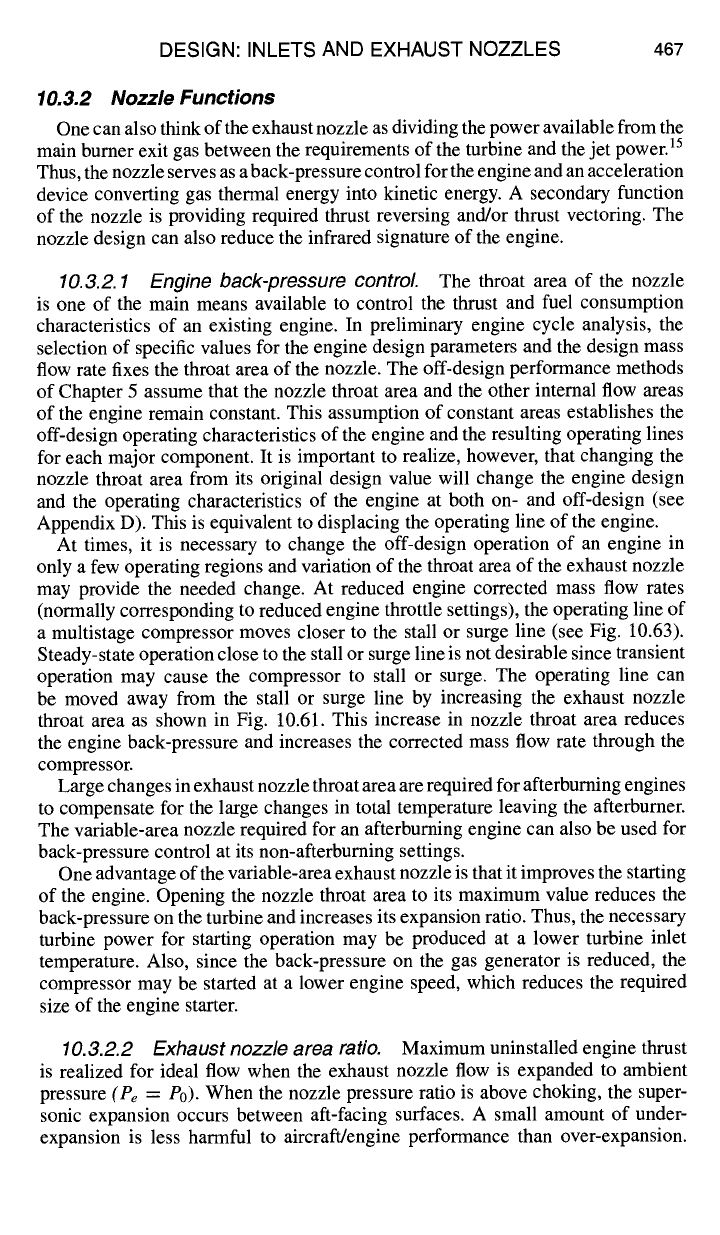
DESIGN: INLETS AND EXHAUST NOZZLES 467
10.3.2 Nozzle Functions
One can also think of the exhaust nozzle as dividing the power available from the
main burner exit gas between the requirements of the turbine and the jet power. 15
Thus, the nozzle serves as a back-pressure control for the engine and an acceleration
device converting gas thermal energy into kinetic energy. A secondary function
of the nozzle is providing required thrust reversing and/or thrust vectoring. The
nozzle design can also reduce the infrared signature of the engine.
10.3.2. 1 Engine back-pressure control
The throat area of the nozzle
is one of the main means available to control the thrust and fuel consumption
characteristics of an existing engine. In preliminary engine cycle analysis, the
selection of specific values for the engine design parameters and the design mass
flow rate fixes the throat area of the nozzle. The off-design performance methods
of Chapter 5 assume that the nozzle throat area and the other internal flow areas
of the engine remain constant. This assumption of constant areas establishes the
off-design operating characteristics of the engine and the resulting operating lines
for each major component. It is important to realize, however, that changing the
nozzle throat area from its original design value will change the engine design
and the operating characteristics of the engine at both on- and off-design (see
Appendix D). This is equivalent to displacing the operating line of the engine.
At times, it is necessary to change the off-design operation of an engine in
only a few operating regions and variation of the throat area of the exhaust nozzle
may provide the needed change. At reduced engine corrected mass flow rates
(normally corresponding to reduced engine throttle settings), the operating line of
a multistage compressor moves closer to the stall or surge line (see Fig. 10.63).
Steady-state operation close to the stall or surge line is not desirable since transient
operation may cause the compressor to stall or surge. The operating line can
be moved away from the stall or surge line by increasing the exhaust nozzle
throat area as shown in Fig. 10.6l. This increase in nozzle throat area reduces
the engine back-pressure and increases the corrected mass flow rate through the
compressor.
Large changes in exhaust nozzle throat area are required for afterburning engines
to compensate for the large changes in total temperature leaving the afterburner.
The variable-area nozzle required for an afterburning engine can also be used for
back-pressure control at its non-afterburning settings.
One advantage of the variable-area exhaust nozzle is that it improves the starting
of the engine. Opening the nozzle throat area to its maximum value reduces the
back-pressure on the turbine and increases its expansion ratio. Thus, the necessary
turbine power for starting operation may be produced at a lower turbine inlet
temperature. Also, since the back-pressure on the gas generator is reduced, the
compressor may be started at a lower engine speed, which reduces the required
size of the engine starter.
10.3.2.2 Exhaust nozzle area ratio. Maximum uninstalled engine thrust
is realized for ideal flow when the exhaust nozzle flow is expanded to ambient
pressure (Pe = P0). When the nozzle pressure ratio is above choking, the super-
sonic expansion occurs between aft-facing surfaces. A small amount of under-
expansion is less harmful to aircraft/engine performance than over-expansion.