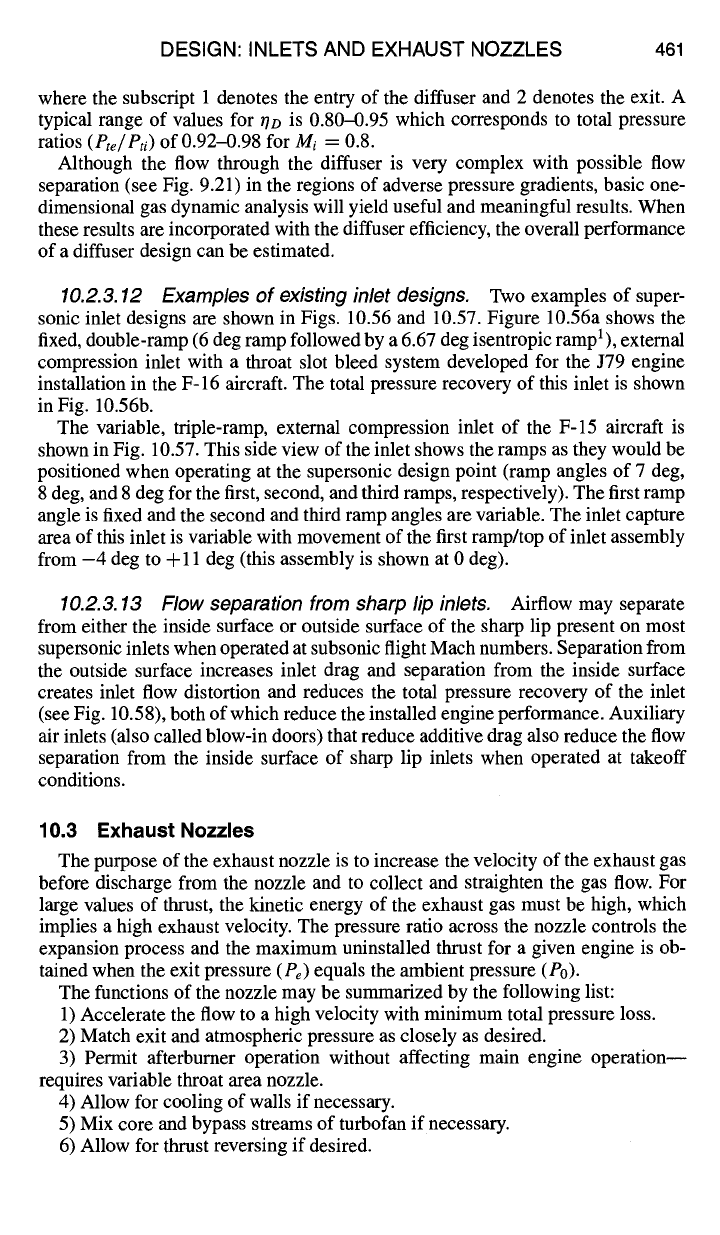
DESIGN: INLETS AND EXHAUST NOZZLES 461
where the subscript 1 denotes the entry of the diffuser and 2 denotes the exit. A
typical range of values for 7o is 0.80-0.95 which corresponds to total pressure
ratios
(Pte/Pti)
of 0.92-0.98 for
Mi
= 0.8.
Although the flow through the diffuser is very complex with possible flow
separation (see Fig. 9.21) in the regions of adverse pressure gradients, basic one-
dimensional gas dynamic analysis will yield useful and meaningful results. When
these results are incorporated with the diffuser efficiency, the overall performance
of a diffuser design can be estimated.
10.2.3.12 Examples of existing inlet designs.
Two examples of super-
sonic inlet designs are shown in Figs. 10.56 and 10.57. Figure 10.56a shows the
fixed, double-ramp (6 deg ramp followed by a 6.67 deg isentropic ramp 1), external
compression inlet with a throat slot bleed system developed for the J79 engine
installation in the F-16 aircraft. The total pressure recovery of this inlet is shown
in Fig. 10.56b.
The variable, triple-ramp, external compression inlet of the F-15 aircraft is
shown in Fig. 10.57. This side view of the inlet shows the ramps as they would be
positioned when operating at the supersonic design point (ramp angles of 7 deg,
8 deg, and 8 deg for the first, second, and third ramps, respectively). The first ramp
angle is fixed and the second and third ramp angles are variable. The inlet capture
area of this inlet is variable with movement of the first ramp/top of inlet assembly
from -4 deg to 4-11 deg (this assembly is shown at 0 deg).
10.2.3.13 Flow separation from sharp lip inlets.
Airflow may separate
from either the inside surface or outside surface of the sharp lip present on most
supersonic inlets when operated at subsonic flight Mach numbers. Separation from
the outside surface increases inlet drag and separation from the inside surface
creates inlet flow distortion and reduces the total pressure recovery of the inlet
(see Fig. 10.58), both of which reduce the installed engine performance. Auxiliary
air inlets (also called blow-in doors) that reduce additive drag also reduce the flow
separation from the inside surface of sharp lip inlets when operated at takeoff
conditions.
10.3 Exhaust Nozzles
The purpose of the exhaust nozzle is to increase the velocity of the exhaust gas
before discharge from the nozzle and to collect and straighten the gas flow. For
large values of thrust, the kinetic energy of the exhaust gas must be high, which
implies a high exhaust velocity. The pressure ratio across the nozzle controls the
expansion process and the maximum uninstalled thrust for a given engine is ob-
tained when the exit pressure
(Pe)
equals the ambient pressure (P0).
The functions of the nozzle may be summarized by the following list:
1) Accelerate the flow to a high velocity with minimum total pressure loss.
2) Match exit and atmospheric pressure as closely as desired.
3) Permit afterburner operation without affecting main engine operation--
requires variable throat area nozzle.
4) Allow for cooling of walls if necessary.
5) Mix core and bypass streams of turbofan if necessary.
6) Allow for thrust reversing if desired.