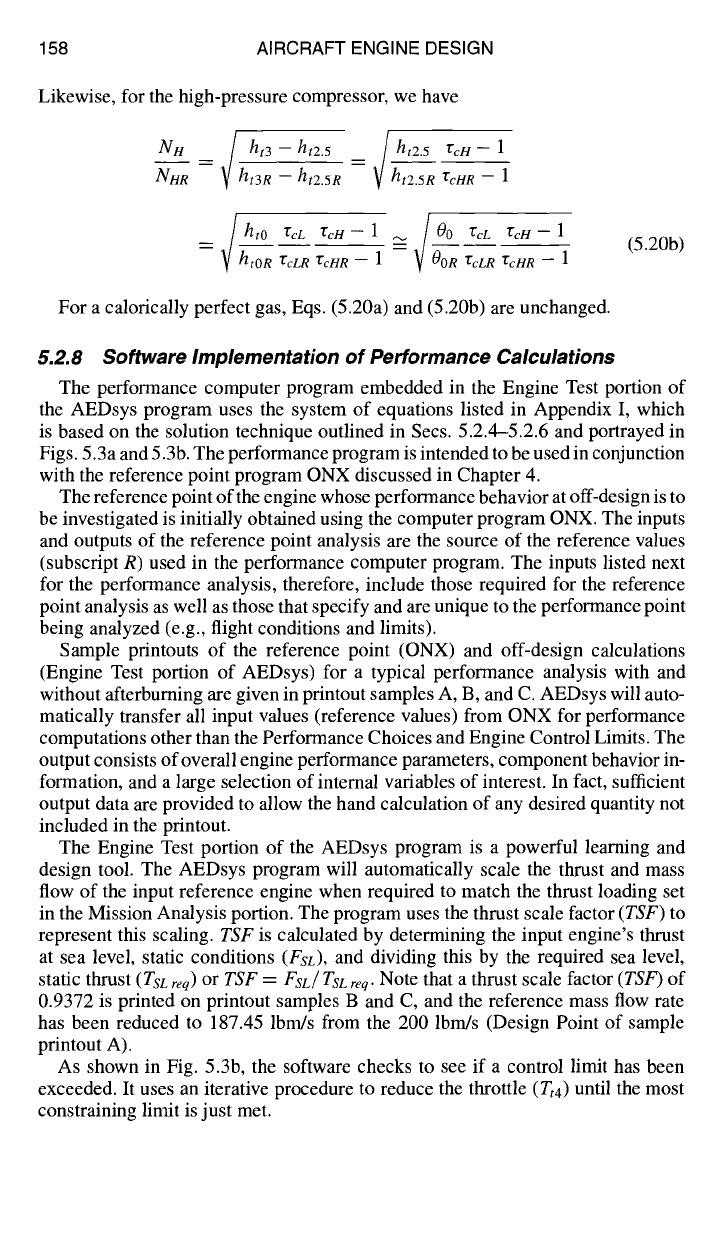
158 AIRCRAFT ENGINE DESIGN
Likewise, for the high-pressure compressor, we have
[
/
NIt / ht3
- ht2.5 [ ht2.5
"rcH -- 1
V V
NoR ht3R --ht2.5R ht2.5R
rcl~R - 1
~ hto rcL rcH -- 1 ~ / O0 tel rcH -- 1
t
-- ht0~ rcLR rc/4R- 1 -- V00R rcLa rc,qR -- 1 (5.20b)
For a calorically perfect gas, Eqs. (5.20a) and (5.20b) are unchanged.
5.2.8 Software Implementation of Performance Calculations
The performance computer program embedded in the Engine Test portion of
the AEDsys program uses the system of equations listed in Appendix I, which
is based on the solution technique outlined in Secs. 5.2.4-5.2.6 and portrayed in
Figs. 5.3a and 5.3b. The performance program is intended to be used in conjunction
with the reference point program ONX discussed in Chapter 4.
The reference point of the engine whose performance behavior at off-design is to
be investigated is initially obtained using the computer program ONX. The inputs
and outputs of the reference point analysis are the source of the reference values
(subscript R) used in the performance computer program. The inputs listed next
for the performance analysis, therefore, include those required for the reference
point analysis as well as those that specify and are unique to the performance point
being analyzed (e.g., flight conditions and limits).
Sample printouts of the reference point (ONX) and off-design calculations
(Engine Test portion of AEDsys) for a typical performance analysis with and
without afterburning are given in printout samples A, B, and C. AEDsys will auto-
matically transfer all input values (reference values) from ONX for performance
computations other than the Performance Choices and Engine Control Limits. The
output consists of overall engine performance parameters, component behavior in-
formation, and a large selection of internal variables of interest. In fact, sufficient
output data are provided to allow the hand calculation of any desired quantity not
included in the printout.
The Engine Test portion of the AEDsys program is a powerful learning and
design tool. The AEDsys program will automatically scale the thrust and mass
flow of the input reference engine when required to match the thrust loading set
in the Mission Analysis portion. The program uses the thrust scale factor
(TSF)
to
represent this scaling.
TSF
is calculated by determining the input engine's thrust
at sea level, static conditions
(FsL),
and dividing this by the required sea level,
static thrust
(Tsc
req)
or
TSF -= FsL/TsL req.
Note that a thrust scale factor
(TSF)
of
0.9372 is printed on printout samples B and C, and the reference mass flow rate
has been reduced to 187.45 lbm/s from the 200 lbm/s (Design Point of sample
printout A).
As shown in Fig. 5.3b, the software checks to see if a control limit has been
exceeded. It uses an iterative procedure to reduce the throttle (Tt4) until the most
constraining limit is just met.