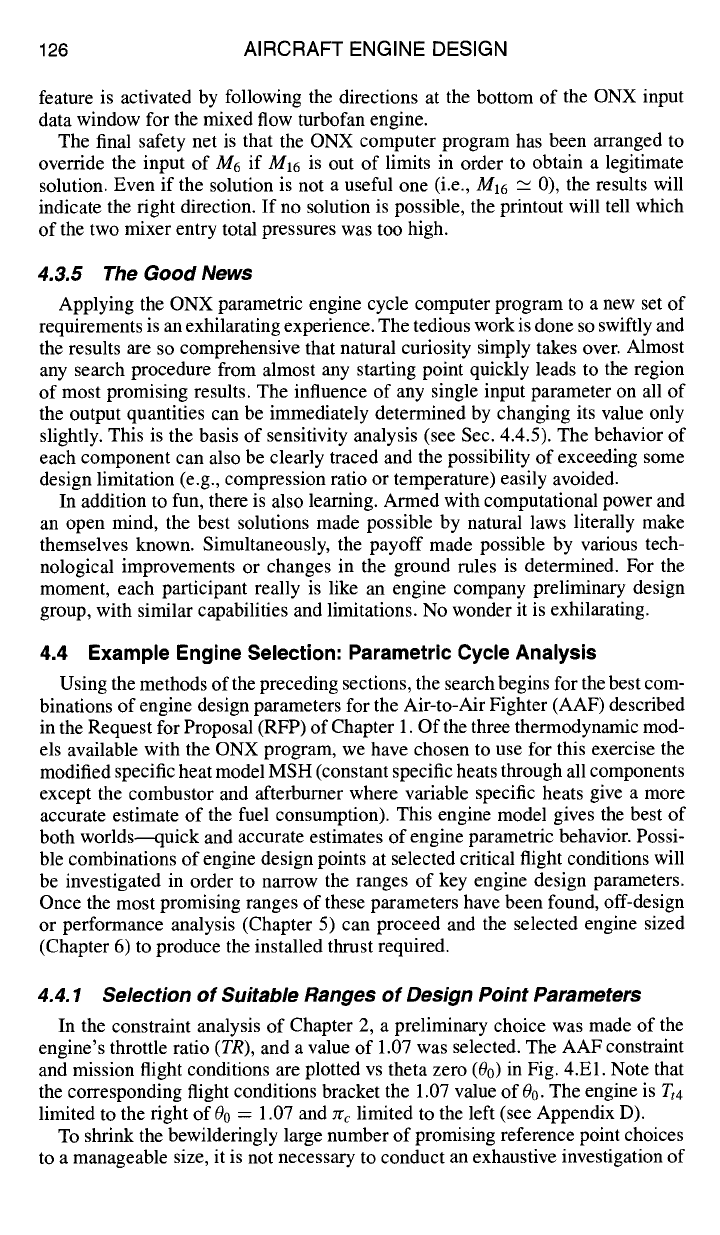
126 AIRCRAFT ENGINE DESIGN
feature is activated by following the directions at the bottom of the ONX input
data window for the mixed flow turbofan engine.
The final safety net is that the ONX computer program has been arranged to
override the input of M6 if M16 is out of limits in order to obtain a legitimate
solution. Even if the solution is not a useful one (i.e., M16 "~ 0), the results will
indicate the right direction. If no solution is possible, the printout will tell which
of the two mixer entry total pressures was too high.
4.3.5 The Good News
Applying the ONX parametric engine cycle computer program to a new set of
requirements is an exhilarating experience. The tedious work is done so swiftly and
the results are so comprehensive that natural curiosity simply takes over. Almost
any search procedure from almost any starting point quickly leads to the region
of most promising results. The influence of any single input parameter on all of
the output quantities can be immediately determined by changing its value only
slightly. This is the basis of sensitivity analysis (see Sec. 4.4.5). The behavior of
each component can also be clearly traced and the possibility of exceeding some
design limitation (e.g., compression ratio or temperature) easily avoided.
In addition to fun, there is also learning. Armed with computational power and
an open mind, the best solutions made possible by natural laws literally make
themselves known. Simultaneously, the payoff made possible by various tech-
nological improvements or changes in the ground rules is determined. For the
moment, each participant really is like an engine company preliminary design
group, with similar capabilities and limitations. No wonder it is exhilarating.
4.4 Example Engine Selection: Parametric Cycle Analysis
Using the methods of the preceding sections, the search begins for the best com-
binations of engine design parameters for the Air-to-Air Fighter (AAF) described
in the Request for Proposal (RFP) of Chapter 1. Of the three thermodynamic mod-
els available with the ONX program, we have chosen to use for this exercise the
modified specific heat model MSH (constant specific heats through all components
except the combustor and afterburner where variable specific heats give a more
accurate estimate of the fuel consumption). This engine model gives the best of
both worlds--quick and accurate estimates of engine parametric behavior. Possi-
ble combinations of engine design points at selected critical flight conditions will
be investigated in order to narrow the ranges of key engine design parameters.
Once the most promising ranges of these parameters have been found, off-design
or performance analysis (Chapter 5) can proceed and the selected engine sized
(Chapter 6) to produce the installed thrust required.
4.4.1 Selection of Suitable Ranges of Design Point Parameters
In the constraint analysis of Chapter 2, a preliminary choice was made of the
engine's throttle ratio
(TR),
and a value of 1.07 was selected. The AAF constraint
and mission flight conditions are plotted vs theta zero (00) in Fig. 4.El. Note that
the corresponding flight conditions bracket the 1.07 value of 00. The engine is
Tt4
limited to the right of 00 = 1.07 and zrc limited to the left (see Appendix D).
To shrink the bewilderingly large number of promising reference point choices
to a manageable size, it is not necessary to conduct an exhaustive investigation of