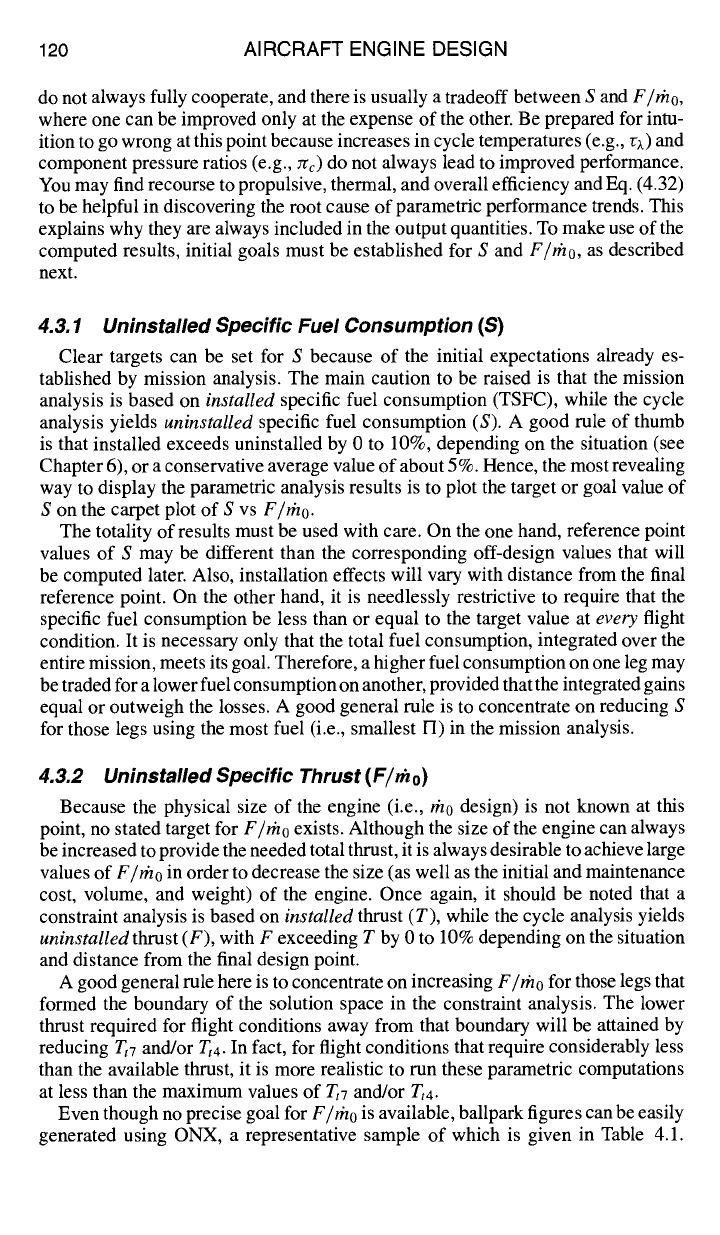
120 AIRCRAFT ENGINE DESIGN
do not always fully cooperate, and there is usually a tradeoff between S and
F/rho,
where one can be improved only at the expense of the other. Be prepared for intu-
ition to go wrong at this point because increases in cycle temperatures (e.g., rz) and
component pressure ratios (e.g., zrc) do not always lead to improved performance.
You may find recourse to propulsive, thermal, and overall efficiency and Eq. (4.32)
to be helpful in discovering the root cause of parametric performance trends. This
explains why they are always included in the output quantities. To make use of the
computed results, initial goals must be established for S and
F/rho,
as described
next.
4.3.1 Uninstalled Specific Fuel Consumption (S)
Clear targets can be set for S because of the initial expectations already es-
tablished by mission analysis. The main caution to be raised is that the mission
analysis is based on
installed
specific fuel consumption (TSFC), while the cycle
analysis yields
uninstalled
specific fuel consumption (S). A good rule of thumb
is that installed exceeds uninstalled by 0 to 10%, depending on the situation (see
Chapter 6), or a conservative average value of about 5%. Hence, the most revealing
way to display the parametric analysis results is to plot the target or goal value of
S on the carpet plot of S vs
F/rho.
The totality of results must be used with care. On the one hand, reference point
values of S may be different than the corresponding off-design values that will
be computed later. Also, installation effects will vary with distance from the final
reference point. On the other hand, it is needlessly restrictive to require that the
specific fuel consumption be less than or equal to the target value at
every
flight
condition. It is necessary only that the total fuel consumption, integrated over the
entire mission, meets its goal. Therefore, a higher fuel consumption on one leg may
be traded for a lower fuel consumption on another, provided that the integrated gains
equal or outweigh the losses. A good general rule is to concentrate on reducing S
for those legs using the most fuel (i.e., smallest 17) in the mission analysis.
4.3.2 Uninstalled Specific Thrust (F/mo)
Because the physical size of the engine (i.e., rho design) is not known at this
point, no stated target for
F/rho
exists. Although the size of the engine can always
be increased to provide the needed total thrust, it is always desirable to achieve large
values of
F/rho
in order to decrease the size (as well as the initial and maintenance
cost, volume, and weight) of the engine. Once again, it should be noted that a
constraint analysis is based on
installed
thrust (T), while the cycle analysis yields
uninstalled
thrust (F), with F exceeding T by 0 to 10% depending on the situation
and distance from the final design point.
A good general rule here is to concentrate on increasing
F/rho
for those legs that
formed the boundary of the solution space in the constraint analysis. The lower
thrust required for flight conditions away from that boundary will be attained by
reducing Tt7 and/or Tt4. In fact, for flight conditions that require considerably less
than the available thrust, it is more realistic to run these parametric computations
at less than the maximum values of Tt7 and/or Tt4.
Even though no precise goal for
F/rho
is available, ballpark figures can be easily
generated using ONX, a representative sample of which is given in Table 4.1.