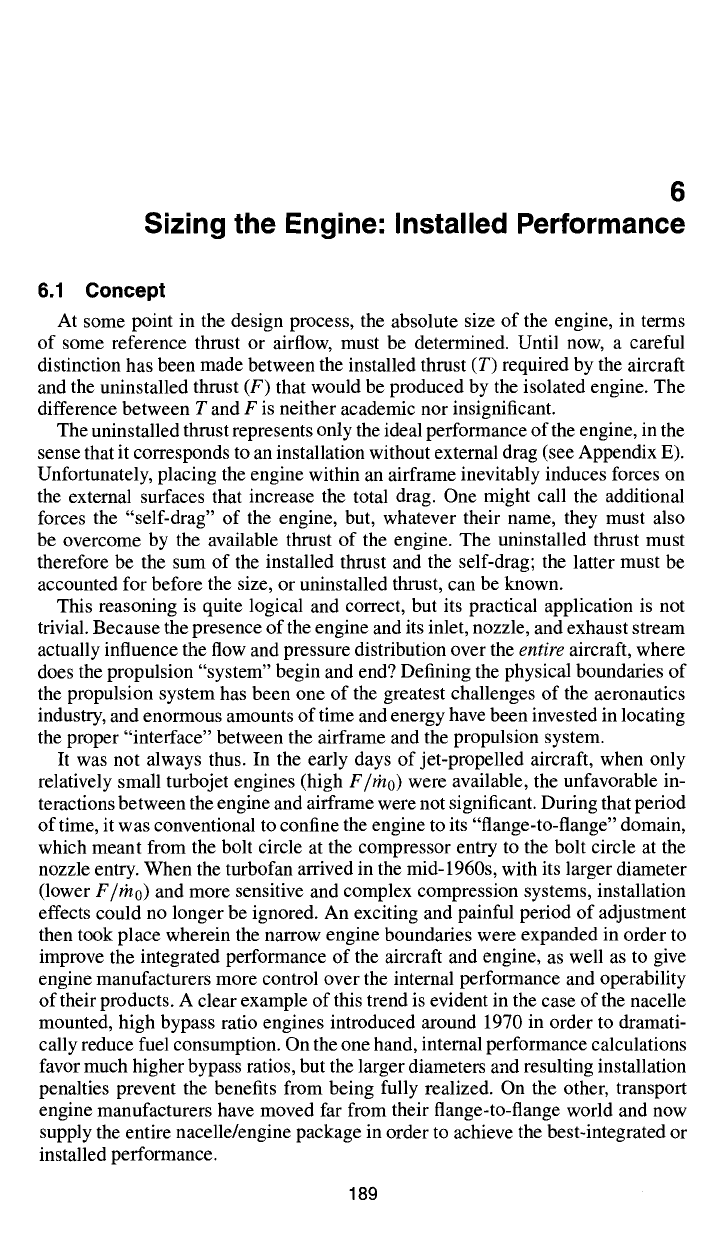
6
Sizing the Engine: Installed Performance
6.1 Concept
At some point in the design process, the absolute size of the engine, in terms
of some reference thrust or airflow, must be determined. Until now, a careful
distinction has been made between the installed thrust (T) required by the aircraft
and the uninstalled thrust (F) that would be produced by the isolated engine. The
difference between T and F is neither academic nor insignificant.
The uninstalled thrust represents only the ideal performance of the engine, in the
sense that it corresponds to an installation without external drag (see Appendix E).
Unfortunately, placing the engine within an airframe inevitably induces forces on
the external surfaces that increase the total drag. One might call the additional
forces the "self-drag" of the engine, but, whatever their name, they must also
be overcome by the available thrust of the engine. The uninstalled thrust must
therefore be the sum of the installed thrust and the self-drag; the latter must be
accounted for before the size, or uninstalled thrust, can be known.
This reasoning is quite logical and correct, but its practical application is not
trivial. Because the presence of the engine and its inlet, nozzle, and exhaust stream
actually influence the flow and pressure distribution over the entire aircraft, where
does the propulsion "system" begin and end? Defining the physical boundaries of
the propulsion system has been one of the greatest challenges of the aeronautics
industry, and enormous amounts of time and energy have been invested in locating
the proper "interface" between the airframe and the propulsion system.
It was not always thus. In the early days of jet-propelled aircraft, when only
relatively small turbojet engines (high F/mo) were available, the unfavorable in-
teractions between the engine and airframe were not significant. During that period
of time, it was conventional to confine the engine to its "flange-to-flange" domain,
which meant from the bolt circle at the compressor entry to the bolt circle at the
nozzle entry. When the turbofan arrived in the mid-1960s, with its larger diameter
(lower F/tho) and more sensitive and complex compression systems, installation
effects could no longer be ignored. An exciting and painful period of adjustment
then took place wherein the narrow engine boundaries were expanded in order to
improve the integrated performance of the aircraft and engine, as well as to give
engine manufacturers more control over the internal performance and operability
of their products. A clear example of this trend is evident in the case of the nacelle
mounted, high bypass ratio engines introduced around 1970 in order to dramati-
cally reduce fuel consumption. On the one hand, internal performance calculations
favor much higher bypass ratios, but the larger diameters and resulting installation
penalties prevent the benefits from being fully realized. On the other, transport
engine manufacturers have moved far from their flange-to-flange world and now
supply the entire nacelle/engine package in order to achieve the best-integrated or
installed performance.
189