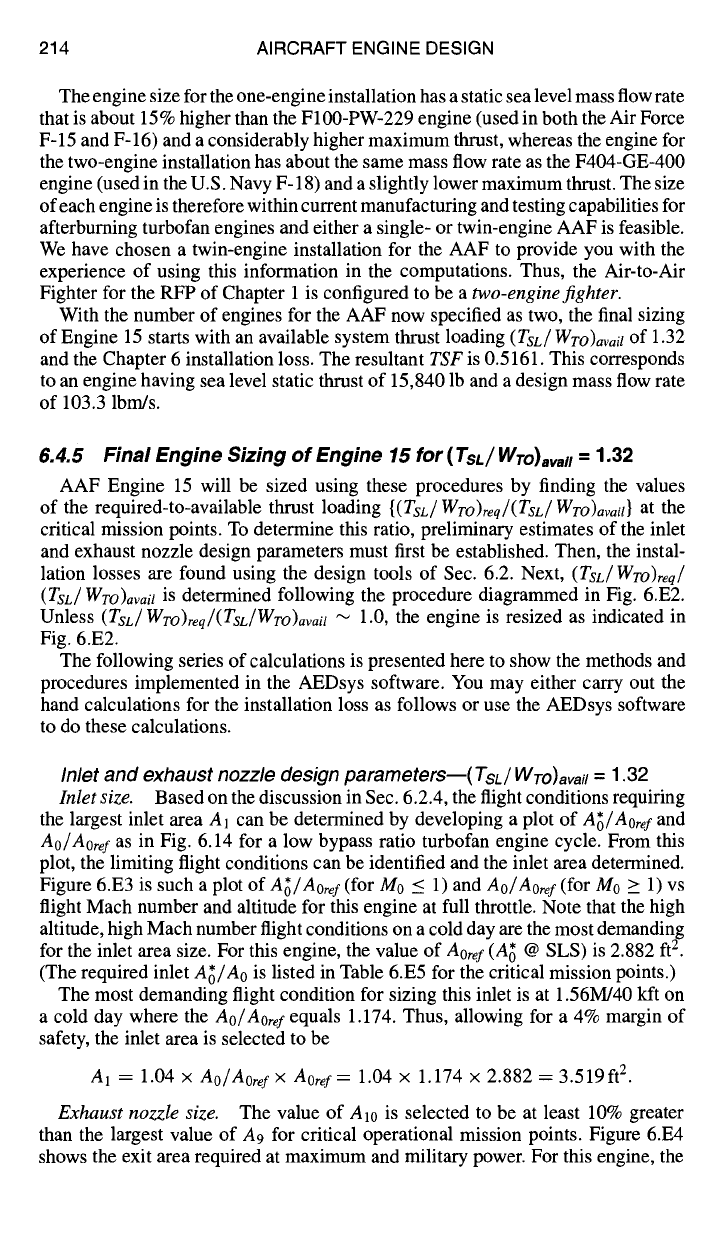
214 AIRCRAFT ENGINE DESIGN
The engine size for the one-engine installation has a static sea level mass flow rate
that is about 15% higher than the F100-PW-229 engine (used in both the Air Force
F-15 and F-16) and a considerably higher maximum thrust, whereas the engine for
the two-engine installation has about the same mass flow rate as the F404-GE-400
engine (used in the U.S. Navy F- 18) and a slightly lower maximum thrust. The size
of each engine is therefore within current manufacturing and testing capabilities for
afterburning turbofan engines and either a single- or twin-engine AAF is feasible.
We have chosen a twin-engine installation for the AAF to provide you with the
experience of using this information in the computations. Thus, the Air-to-Air
Fighter for the RFP of Chapter 1 is configured to be a
two-enginefighter.
With the number of engines for the AAF now specified as two, the final sizing
of Engine 15 starts with an available system thrust loading
(TsL/WTo)av,~il
of 1.32
and the Chapter 6 installation loss. The resultant
TSF
is 0.5161. This corresponds
to an engine having sea level static thrust of 15,840 lb and a design mass flow rate
of 103.3 lbm/s.
6.4.5 Final Engine Sizing of Engine 15 for ( TsL/ WTO)avail --
1.32
AAF Engine 15 will be sized using these procedures by finding the values
of the required-to-available thrust loading
{(TsL/Wro)req/(Tsj Wro)avait}
at the
critical mission points. To determine this ratio, preliminary estimates of the inlet
and exhaust nozzle design parameters must first be established. Then, the instal-
lation losses are found using the design tools of Sec. 6.2. Next,
(TsL/Wro)req/
(TsL/WTO)avail
is determined following the procedure diagrammed in Fig. 6.E2.
Unless
(TsL/WTO)req/(ZsL/WTO)avail
'~
1.0, the engine is resized as indicated in
Fig. 6.E2.
The following series of calculations is presented here to show the methods and
procedures implemented in the AEDsys software. You may either carry out the
hand calculations for the installation loss as follows or use the AEDsys software
to do these calculations.
Inlet and exhaust nozzle design parameters--( TsL/ WTO)avail
=
1.32
Inlet size.
Based on the discussion in Sec. 6.2.4, the flight conditions requiring
the largest inlet area A1 can be determined by developing a plot of
A~/Aoref
and
Ao/Aoref
as in Fig. 6.14 for a low bypass ratio turbofan engine cycle. From this
plot, the limiting flight conditions can be identified and the inlet area determined.
Figure 6.E3 is such a plot of
A~/Aoref
(for M0 < 1) and
Ao/Aoref
(for M0 _> 1) vs
flight Mach number and altitude for this engine at full throttle. Note that the high
altitude, high Mach number flight conditions on a cold day are the most demanding
for the inlet area size. For this engine, the value of
Aoref
(A~ @ SLS) is 2.882 fte.
(The required inlet
A~/Ao
is listed in Table 6.E5 for the critical mission points.)
The most demanding flight condition for sizing this inlet is at 1.56M/40 kft on
a cold day where the
Ao/Aoref
equals 1.174. Thus, allowing for a 4% margin of
safety, the inlet area is selected to be
A1 = 1.04 x
Ao/Aoref× Aoref=
1.04 x 1.174 × 2.882 = 3.519ft e.
Exhaust nozzle size.
The value of A10 is selected to be at least 10% greater
than the largest value of A9 for critical operational mission points. Figure 6.E4
shows the exit area required at maximum and military power. For this engine, the