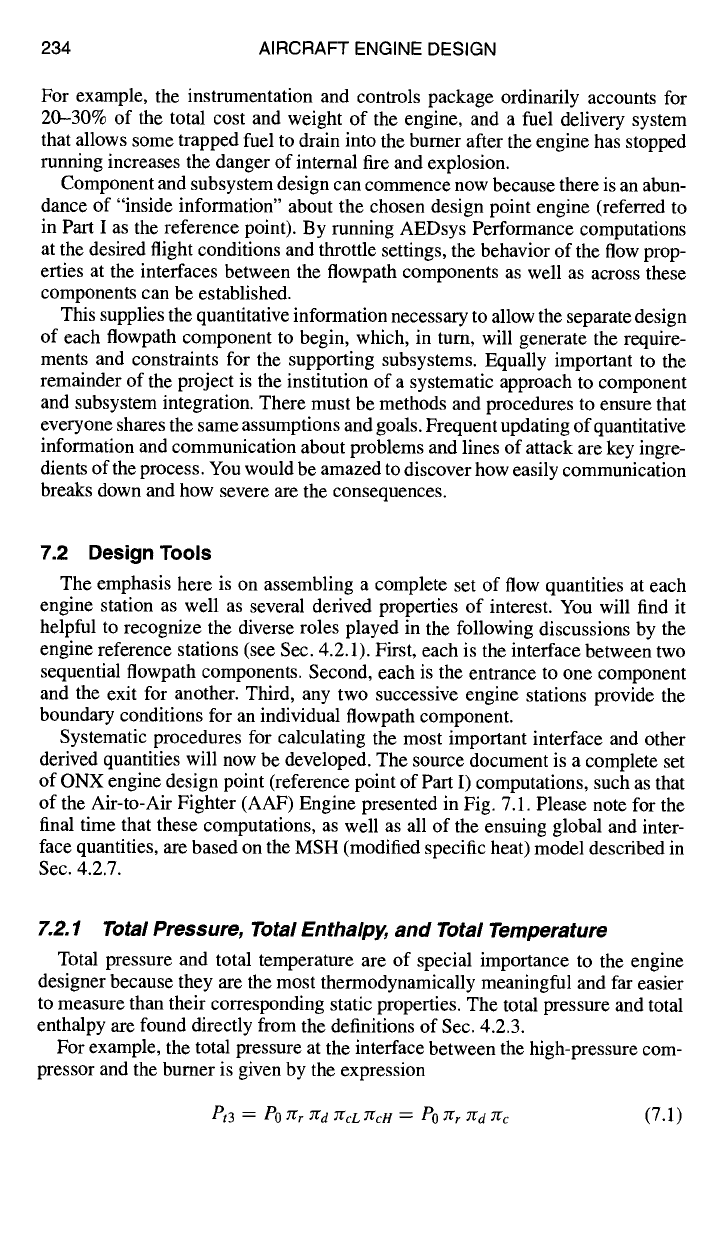
234 AIRCRAFT ENGINE DESIGN
For example, the instrumentation and controls package ordinarily accounts for
20-30% of the total cost and weight of the engine, and a fuel delivery system
that allows some trapped fuel to drain into the burner after the engine has stopped
running increases the danger of internal fire and explosion.
Component and subsystem design can commence now because there is an abun-
dance of "inside information" about the chosen design point engine (referred to
in Part I as the reference point). By running AEDsys Performance computations
at the desired flight conditions and throttle settings, the behavior of the flow prop-
erties at the interfaces between the flowpath components as well as across these
components can be established.
This supplies the quantitative information necessary to allow the separate design
of each flowpath component to begin, which, in turn, will generate the require-
ments and constraints for the supporting subsystems. Equally important to the
remainder of the project is the institution of a systematic approach to component
and subsystem integration. There must be methods and procedures to ensure that
everyone shares the same assumptions and goals. Frequent updating of quantitative
information and communication about problems and lines of attack are key ingre-
dients of the process. You would be amazed to discover how easily communication
breaks down and how severe are the consequences.
7.2 Design Tools
The emphasis here is on assembling a complete set of flow quantities at each
engine station as well as several derived properties of interest. You will find it
helpful to recognize the diverse roles played in the following discussions by the
engine reference stations (see Sec. 4.2.1). First, each is the interface between two
sequential flowpath components. Second, each is the entrance to one component
and the exit for another. Third, any two successive engine stations provide the
boundary conditions for an individual flowpath component.
Systematic procedures for calculating the most important interface and other
derived quantities will now be developed. The source document is a complete set
of ONX engine design point (reference point of Part I) computations, such as that
of the Air-to-Air Fighter (AAF) Engine presented in Fig. 7.1. Please note for the
final time that these computations, as well as all of the ensuing global and inter-
face quantities, are based on the MSH (modified specific heat) model described in
Sec. 4.2.7.
7.2.1 Total Pressure, Total Enthalpy, and Total Temperature
Total pressure and total temperature are of special importance to the engine
designer because they are the most thermodynamically meaningful and far easier
to measure than their corresponding static properties. The total pressure and total
enthalpy are found directly from the definitions of Sec. 4.2.3.
For example, the total pressure at the interface between the high-pressure com-
pressor and the burner is given by the expression
Pt3 = P0 rer red reel Zrcn = P0 rer Jrd rec (7.1)