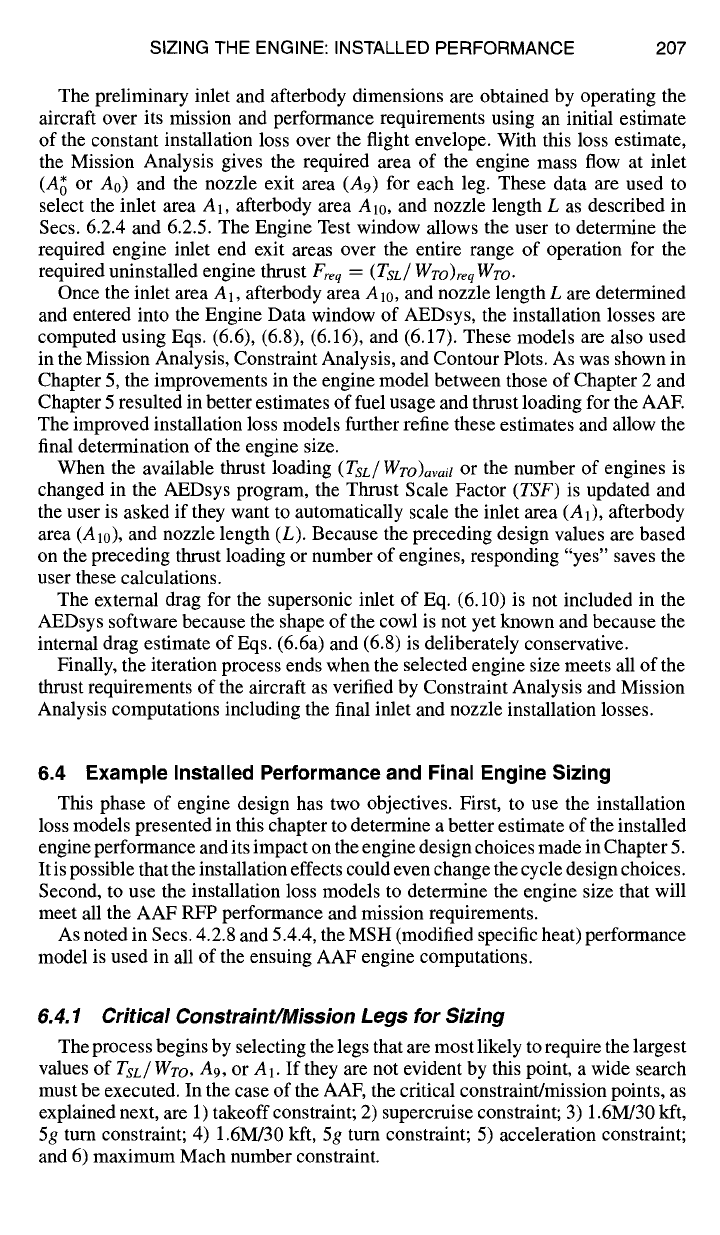
SIZING THE ENGINE: INSTALLED PERFORMANCE 207
The preliminary inlet and afterbody dimensions are obtained by operating the
aircraft over its mission and performance requirements using an initial estimate
of the constant installation loss over the flight envelope. With this loss estimate,
the Mission Analysis gives the required area of the engine mass flow at inlet
(A~ or A0) and the nozzle exit area (A9) for each leg. These data are used to
select the inlet area A1, afterbody
area A10,
and nozzle length L as described in
Sees. 6.2.4 and 6.2.5. The Engine Test window allows the user to determine the
required engine inlet end exit areas over the entire range of operation for the
required uninstalled engine thrust
Ere q = ( TsL // WTO )req WTO.
Once the inlet area A1, afterbody area A10, and nozzle length L are determined
and entered into the Engine Data window of AEDsys, the installation losses are
computed using Eqs. (6.6), (6.8), (6.16), and (6.17). These models are also used
in the Mission Analysis, Constraint Analysis, and Contour Plots. As was shown in
Chapter 5, the improvements in the engine model between those of Chapter 2 and
Chapter 5 resulted in better estimates of fuel usage and thrust loading for the AAF.
The improved installation loss models further refine these estimates and allow the
final determination of the engine size.
When the available thrust loading
(TsL/Wro)avaa
or the number of engines is
changed in the AEDsys program, the Thrust Scale Factor
(TSF)
is updated and
the user is asked if they want to automatically scale the inlet area (A1), afterbody
area (A10), and nozzle length (L). Because the preceding design values are based
on the preceding thrust loading or number of engines, responding "yes" saves the
user these calculations.
The external drag for the supersonic inlet of Eq. (6.10) is not included in the
AEDsys software because the shape of the cowl is not yet known and because the
internal drag estimate of Eqs. (6.6a) and (6.8) is deliberately conservative.
Finally, the iteration process ends when the selected engine size meets all of the
thrust requirements of the aircraft as verified by Constraint Analysis and Mission
Analysis computations including the final inlet and nozzle installation losses.
6,4 Example Installed Performance and Final Engine Sizing
This phase of engine design has two objectives. First, to use the installation
loss models presented in this chapter to determine a better estimate of the installed
engine performance and its impact on the engine design choices made in Chapter 5.
It is possible that the installation effects could even change the cycle design choices.
Second, to use the installation loss models to determine the engine size that will
meet all the AAF RFP performance and mission requirements.
As noted in Sees. 4.2.8 and 5.4.4, the MSH (modified specific heat) performance
model is used in all of the ensuing AAF engine computations.
6.4.1 Critical Constraint~Mission Legs for Sizing
The process begins by selecting the legs that are most likely to require the largest
values of
TsL/Wro, A9,
or A1. If they are not evident by this point, a wide search
must be executed. In the case of the AAF, the critical constraint/mission points, as
explained next, are 1) takeoff constraint; 2) supercruise constraint; 3) 1.6M/30 kft,
5g turn constraint; 4) 1.6M/30 kft, 5g turn constraint; 5) acceleration constraint;
and 6) maximum Mach number constraint.