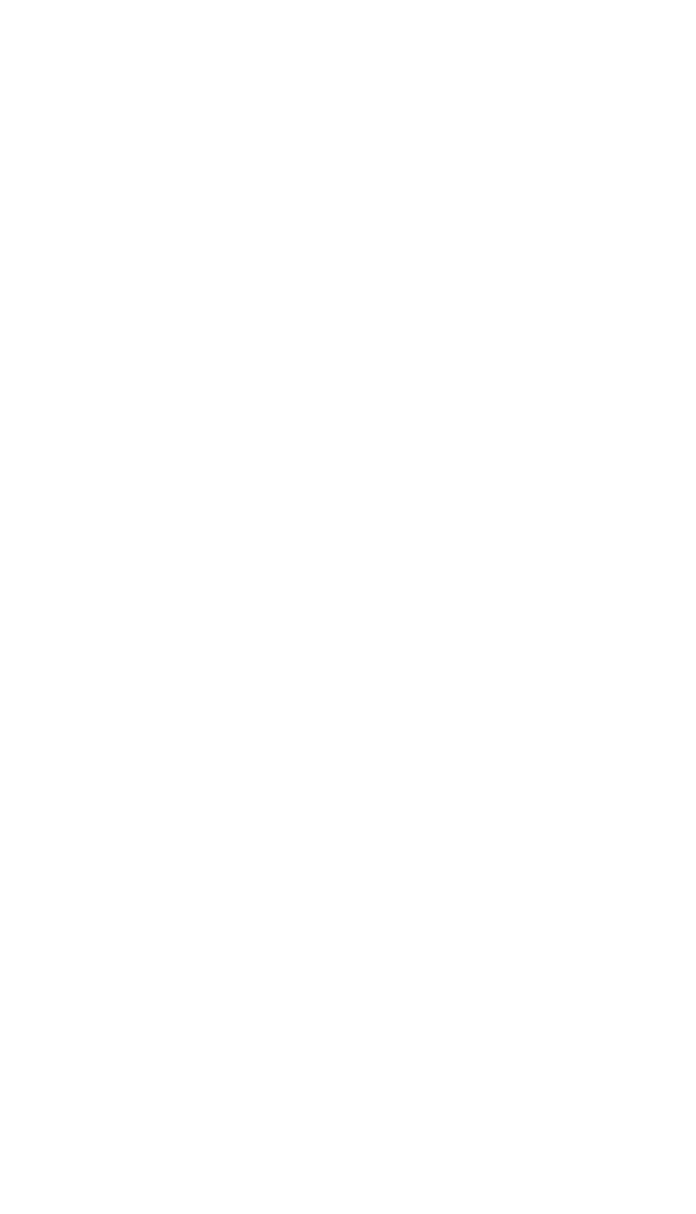
1092 COMPOSITES FABRICATION PROCESSES
changing the shaped clamping pads. Caterpillar traction is suitable for handling
flat products but is generally not as versatile as the reciprocating system. The
reinforcement may be impregnated by passing it through a bath of resin, as with
filament winding, or by injecting resin into the entry portion of the die. These
points are all illustrated in Figs. 35–38.
Solid and hollow sections may be manufactured and virtually any external
profile that can be contained in a window approximately 2
⫻ 1 m. Pultrusion
speeds are quite low, seldom more than 2–3 m/min. The speed is dictated by
the length of the die and the necessary cure time, which is temperature depen-
dent. In practice die temperature and pulling rate are adjusted so that the section
is sufficiently cured when it emerges from the die. The process may be speeded
up by preheating the charge as it enters the die or by partly curing in the die
and then postcuring. There are shape restrictions, which are discussed below.
There are also several options in choice of reinforcement and some possibilities
for making curved sections and accommodating section changes along the length
of the product. There is considerable interest in pultruding composites with ther-
moplastic matrices. In this case the reinforcement must either be preimpregnated
or consist of one of the commingled forms, the resin in the form of fibers or
strips of tape, interspersed with the reinforcement fibers. The charge must be
heated to melt the matrix before or during entry into the first section of the die,
which is hot. The charge then passes through a hot consolidation stage and
finally through a cooled exit stage so that the matrix has solidified by the exit
point. This is a developing technology and is not yet standard practice.
10.2 Reinforcement Options for Pultrusion
The basic requirement is that the reinforcement is continuous or at least in
sufficiently long lengths that batches may be joined to maintain the continuous
operation of the pultruder. The most obvious feedstocks are continuous rovings.
The logistics of the process warrant some consideration. Individual packages
(cheeses) of roving are generally supplied in weights of up to
⬇25 kg. For a
typical roving density of 2500 tex, this translates to a continuous length of 10
km, sufficient to keep the process running for about 100 h. One E-glass roving
of 2500 tex corresponds to approximately 1 mm
2
cross-sectional area when
molded. Thus, to pultrude a hollow section 100 mm
2
and of 3 mm wall thickness,
i.e., cross-sectional area of approximately 1200 mm
2
, 1200 individual roving
packages, or creels, would need to be set up to feed into the die. Setting up the
machine is therefore a significant logistical exercise. But, having set up the
process, 10 km of the section could be manufactured in a single campaign, with
very little supervision being required beyond maintaining the flow of resin and
disposing of the product. One problem with using just roving as feedstock is
that the product is composed entirely of uniaxial fibers. This may be acceptable
for a limited range of products but some cross reinforcement is usually required.
Alternative forms of feedstock are tapes of any of the standard sheet forms
of reinforcements. Chopped strand and continuous random mats are widely used
together with woven and braided fabrics. These are invariably prepared as rolls
of tape, trimmed to widths to suit the part being manufactured. These may be
folded as they enter the die to form angle, channel, Tee and H sections, ribbed
tubes, and a wide range of special sections, as illustrated in Fig. 37. Typical
cross sections for pultruded products are shown in Fig. 38. Pultrusions may be