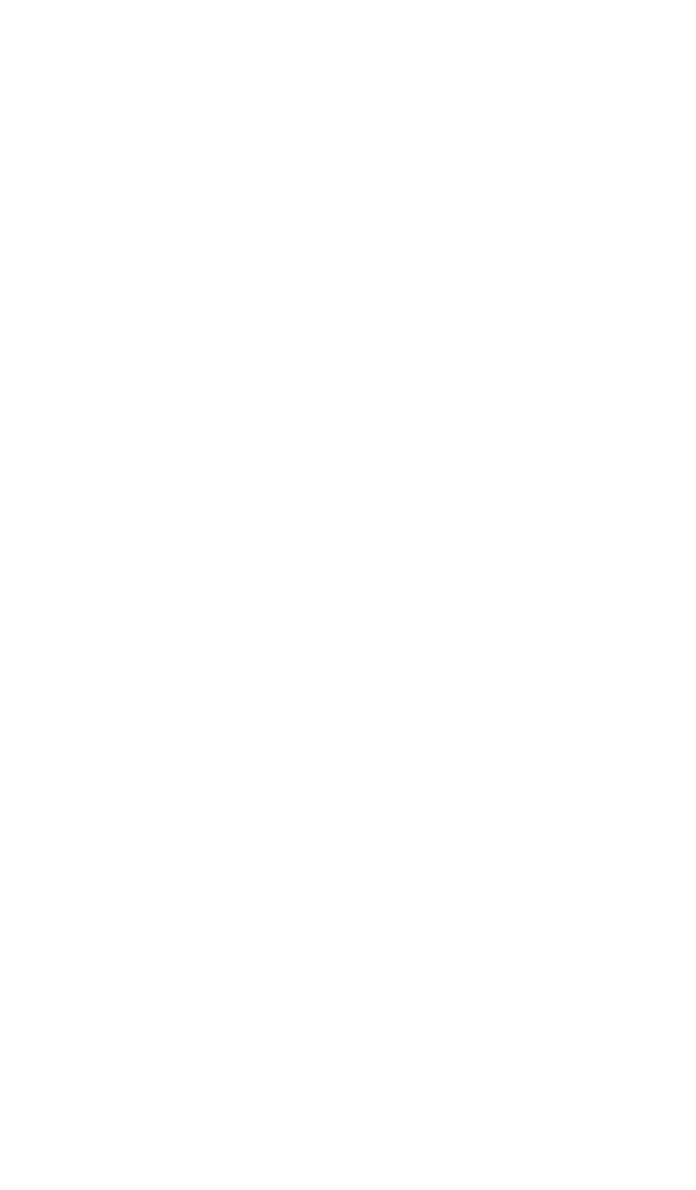
5 AUTOCLAVE PROCESSING OF PREPREG 1069
5.4 Cutting the Prepreg
Prepreg may be hand or machine cut. The latter is adopted for all but the smallest
operations. The prepreg rolls must first be withdrawn from cold storage and
allowed to equilibrate to shop temperature. This may take up to 24 h. The roll
must not be removed from its protective bag or unrolled while it is cold, oth-
erwise moisture may condense from the atmosphere onto the cold prepreg. This
would lead to water absorption and processing problems, e.g., porosity. Cutting
should be carried out in a clean room with temperature and humidity controlled
[20
⬚C and 50% relative humidity (RH) is common]. For hand cutting shears, a
Stanley knife, or a cutting wheel may be used. It is usual to make templates for
each ply from card, plastic, or sheet metal to provide a cutting guide. Each
template must also indicate the fiber orientation (e.g., 0
⬚,90⬚, Ⳳ45⬚) so that the
template may be correctly positioned on the roll of prepreg. When the width of
the part exceeds the width of the prepreg, it may be necessary to cut several
pieces to make up a single ply. Many moldings are of varying thickness. This
involves ply drops, which are preferably located toward the center thickness so
that there are no steps on the outside surfaces. It will be apparent that the
logistics of laying up a complex laminate of, say, 48 plies, with a specified
configuration, (e.g., the quasi-isotropic [0
⬚,90⬚, Ⳳ45⬚]s), will be quite complex.
Each ply will require a drawing, part number, and template. The plies must then
be cut from the roll of prepreg, with due regard to minimizing wastage; each
ply must be identified and then stacked to form a kit of plies in the correct order
for the lay-up operation. If necessary positional index marks must be placed on
the cover film of each ply to facilitate precise positioning. These are the argu-
ments for using an automated cutting system.
The automatic prepreg cutter consists of a flat bed, typically 2 m wide by 10
m long. The prepreg sheets are unrolled along the bed, butting two or more
together if a wider strip is required and, sometimes, more than one layer. They
are retained in place by suction from under the bed. The cutter head is mounted
on a gantry that moves along the bed in the length direction and may also
traverse in the width and vertical directions. The cutting method may be a re-
ciprocating knife, ultrasonic knife, or water jet. The cutting operation is con-
trolled by a computer that is linked to the CAD system. Thus, each ply is defined
in the software, so neither drawings or templates are required. The software also
incorporates a nesting program that adjusts the cutting sequence to minimize
waste. The software and the machines have been developed from those used in
the garment industry. A small automatic prepreg cutter is shown in Fig. 17. The
cutting operation is initiated and the cutter automatically cuts all the plies defined
on the bed. There is also a printing head that numbers each piece and can print
index marks that are used to facilitate precise lay-up. At the end of the run the
cut plies are gathered and collated, either by hand or by a robotic device that
automatically collects and collates the plies into kits ready for lay-up. Although
the cost of such equipment is high, the benefits in terms of precise cutting, speed,
elimination of hand operations, waste minimization, and improved quality as-
surance are very considerable.
5.5 Hand Lay-up
The tool is prepared and a release agent and/or release film applied across the
molding surfaces. The prepreg kit is delivered to the lay-up location. At this