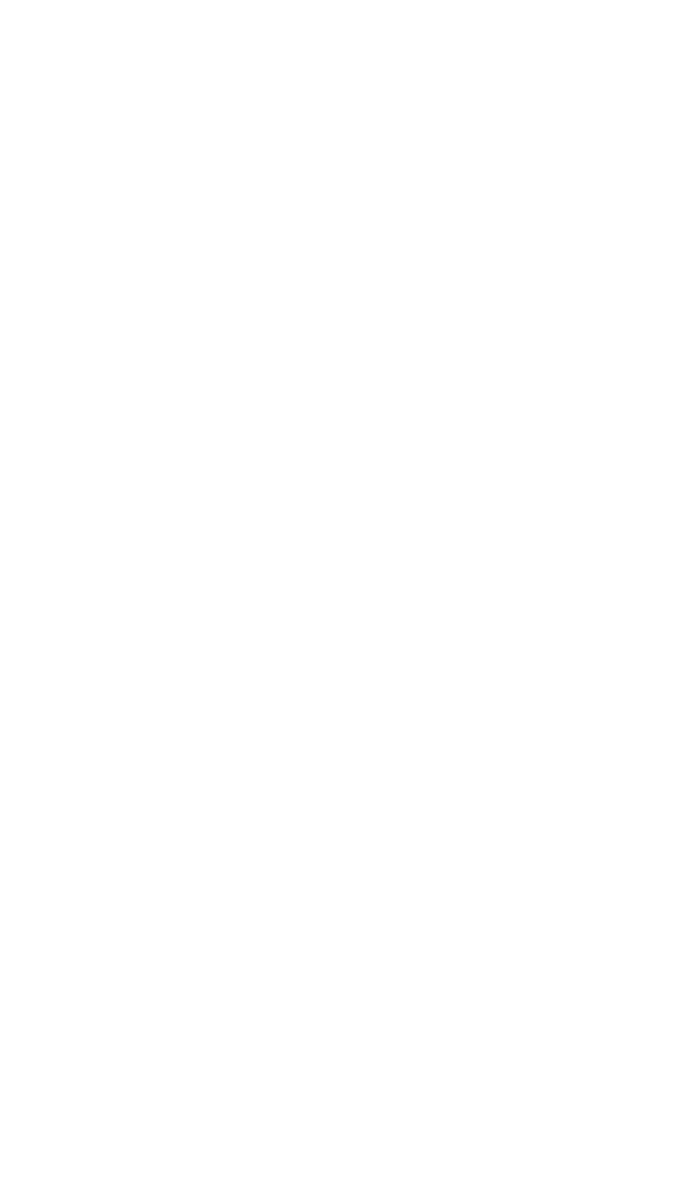
1102 COMPOSITES FABRICATION PROCESSES
woven impregnated tape, and as impregnated tow. The normal reinforcement is
carbon fiber as it is not generally cost effective to use lower performance fibers
with such expensive matrices. The only exceptions would be where specific
physical properties, such as radar transparency, were required.
The tape materials are produced in thicknesses comparable with that of con-
ventional prepreg, e.g., 0.125–0.25 mm, much thinner than GMT. Impregnated
tow is typically a single tow of 6000 or 10,000 carbon fibers. The sheets are
stiff and boardlike at room temperature and cannot be draped at all without
heating. The tows may be coiled.
14.3 Processing Principles
The principles for processing high-performance thermoplastic composites are
similar to those for GMT. The material must be heated to a temperature that
melts the matrix; it can then be shaped and must be chilled in the formed shape
to freeze the matrix. There are, however, a number of additional considerations.
First, the continuous fiber, high V
ƒ
, feedstock material will not flow to any
extent when molded. Its drape possibilities are similar to those of prepreg, except
that the thermoplastic form must be heated before it can be draped at all. A
second consideration is that the melting points of some of the matrices approach
400
⬚C, so that any tooling that needs to be heated to the melt temperature must
be steel. Other materials can be used where the hot feedstock is stamped between
cold dies. A third point is that some of the thermoplastics are semicrystalline,
e.g., PEEK, and their properties are strongly sensitive to the degree of crystal-
linity. This means that the cooling rate from the melt temperature to below the
crystallization temperature must be controlled. Finally, when using high-
performance materials, very close control of V
ƒ
, fiber architecture, and dimen-
sions is required so that optimum performance is achieved. These factors
combine to make processing a more complex operation. The simple preheat and
cold stamp process used for GMT is sometimes adequate but, in general, these
prepreg-like feedstocks require a more extended period for consolidation while
hot.
14.4 Autoclave and Press Processing
Panels of moderate single curvature and low complexity may be molded using
either an autoclave or a press. The thin sheets of feedstock are cut to the required
profile and stacked in sequence, as for prepreg. The difference is that the material
has no tack to retain each ply in position. This may be accomplished by thermal
tacking. A soldering iron or similar implement is used to spot weld the sheets
together as they are laid. When the laminate has been completed, it is placed
on the tool and covered with a vacuum membrane. Owing to the high processing
temperature, this may need to be a high-temperature stable polymer or elastomer,
or even aluminum foil. The assembly is then subjected to vacuum and placed
in the autoclave. The temperature and pressure may then be raised so that the
matrix melts, typically in the range 250–400
⬚C, and the pressure consolidates
the laminate. This process can take longer than for thermoset systems due to
the higher viscosity of the molten thermoplastic. Once consolidation has been
completed, the whole assembly must be cooled, under pressure, until the matrix
has solidified. Furthermore the cooling rate must be controlled through the crit-