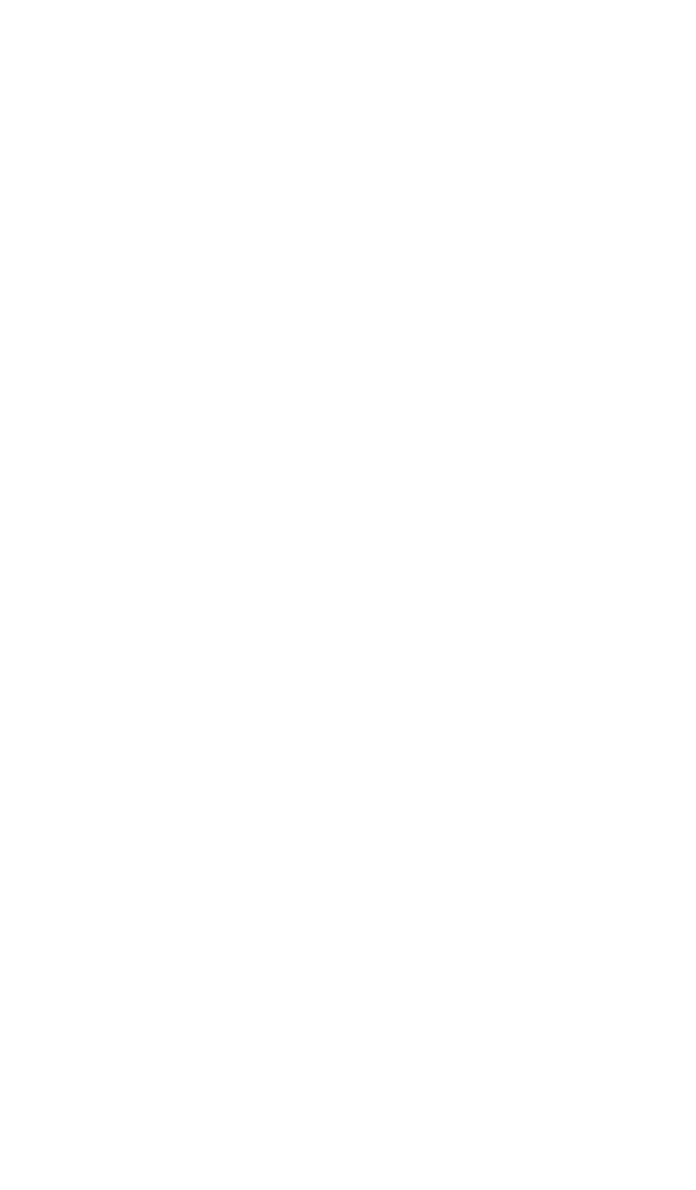
3 ADVANCED PROCESSING 1117
3 ADVANCED PROCESSING
When it comes to advanced ceramics, we can assume that there is value added
in the product that justifies advanced processing. If there is no value added, then
we might as well follow the methods developed thousands of years ago for
pottery. It would be foolish to suggest that we are abandoning pottery and
whitewares or that we ever will. To the contrary, whitewares constitute a major
part of the ceramic industry, and there are continuing improvements in their
manufacture, with respect to increasing their environmental friendliness, recy-
cling, performance, and economics.
The need for improving conventional processing has been well served [see,
e.g., Lange (1989), Lewis (2000), Sigmund et al. (2000)]. When it comes to
conventional powder processing, the needs are water-based systems to replace
organic-solvent-based systems, denser suspensions, better powder stabilization
schemes, and more in situ diagnostics. While addressing these issues is critical
to the health of the ceramic industry, the long-term survival and growth of ce-
ramics require some radical new processing schemes. The new technologies are
the basis for the remainder of this chapter. The interested reader will find that
conventional ceramics are treated thoroughly in many excellent textbooks [see,
e.g., Reed (1995)] and there is not enough room in this review for a full treat-
ment.
In looking for what is new in ceramic processing, three directions appear.
One can look for new energy sources for processing, such as microwave heating,
self-propagating reactions, mechanochemical processes, or reaction bonding.
One can look for new ways to control particle characteristics, such as size (e.g.,
nanoparticles), shape (e.g., equiaxed particles), metastable phases (e.g., rapid
solidification), or templating (e.g., seeding). Alternatively, one can look for new
building blocks, such as polymer precursors or sol–gel processing.
3.1 New Energy Sources
Microwave Processing
What is microwave processing? From the initial attempts in around 1979 to sinter
ferrites with microwaves, it has been know that certain materials show heating
effects through dielectric loss when irradiated with microwaves at a frequency
of 2.45 GHz. Ordinarily, microwaves, which are located on the electromagnetic
spectrum between infrared and radio waves, correspond to energies characteristic
of molecular rotation. This explains the usefulness of microwaves in reheating
food, which contains water molecules. In addition, selected ceramic composi-
tions show rapid heating through the use of microwaves. While materials with
low loss tangents are transparent to microwaves and materials, such as metals,
with high loss tangents reflect microwaves, it is the materials with intermediate
loss tangents that can benefit from microwave treatment. In the case of ceramics,
where an ion jump relaxation mechanism gives rise to polarization in an applied
electric field, there is the possibility to use microwaves to assist sintering [see,
e.g., Katz (1992), Clark and Sutton (1996)]. The advantages of microwave heat-
ing are experienced through volumetric heating, and rapid heating, resulting in
increased kinetics. The danger of microwave heating in ceramics is nonuniform
susceptibility, leading to localized hotspots, nonuniform grain growth, or ag-