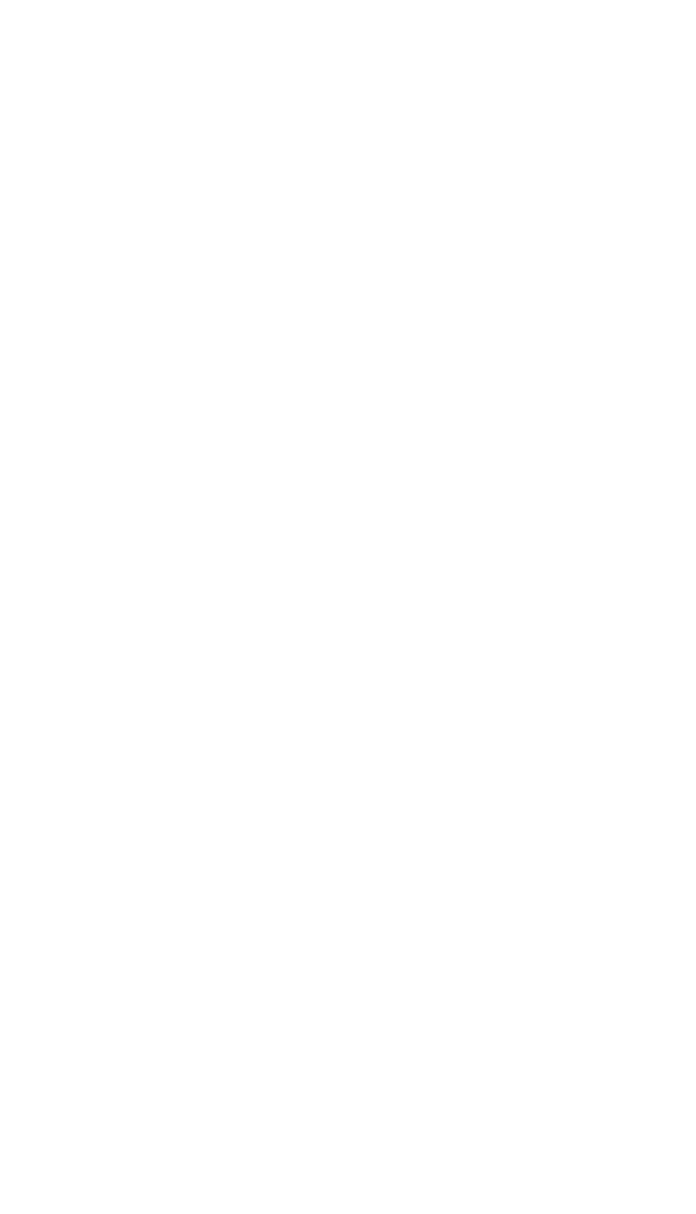
1154 SPACECRAFT APPLICATIONS OF ADVANCED COMPOSITE MATERIALS
wiring boards and electrical components in place. Composite enclosures can be
made significantly lighter than machined aluminum enclosures and may be pro-
duced at a lower unit cost while possessing equal or better mechanical and
thermal performance. Three groups of functional requirements—mechanical
loading and physical attachment specifications, thermal control for installed elec-
tronic components, and environmental shielding—must be satisfied in the design
process for electronics enclosures.
Both physical support and protection for electronic components (often printed
wiring boards) are provided by electronics enclosures. Design considerations
must include the accurate alignment of printed wiring boards (PWBs) to a moth-
erboard or input/output connection area, and provisions for mechanical attach-
ment to the spacecraft bus. The enclosure must be stiff enough to meet internal
deflection specifications during launch conditions, and alignment and support
must be maintained over thermal extremes. Designs usually include a removable
cover to facilitate installation, removal, and exchange of enclosed components.
Mechanical loads from launch or thermal expansion are the primary drivers
for the structural design requirements. Static equivalent of dynamic loads are
calculated from a curve of power spectral density of random vibration, and
launch loads are generally used to represent loadings for mechanical analysis,
as described by Steinberg.
19
The walls of the enclosure can then be sized by
analyzing them as individual orthotropic flat plates with simply supported bound-
aries. This method greatly simplifies initial sizing and enables the designer to
create a more optimum structure. This method is superior to the standard ‘‘black
aluminum’’ design process where metals are simply replaced with dimensionally
equivalent quasi-isotropic composites. Roberts
20
has shown that a reasonable, if
somewhat conservative, approximation of actual static deflections and natural
modes can be produced with orthotropic analysis.
The thermal environment inside the electronics enclosure must be controlled
to ensure the safety of sensitive internal electronics, so some provision must be
made to expel heat generated by electronic components. The thermal dissipation
path may consist of several parts. Paths begin at individual electronic compo-
nents, but all must end at the final heat sink or thermal reservoir, usually space.
A typical thermal path may be subdivided as follows: electronic component to
PWB, PWB to card guide, PWB and card guide to the enclosure wall, wall to
mounting feet, and feet to base or enclosure wall to space. Conduction is the
chief mode of thermal flow in electronics enclosures with the exception of ra-
diation from the enclosure walls to space.
The composite fiber properties rather than the resin properties are the main
contributors to values for in-plane thermal conductivity. Carbon fiber composites
can be made that have equal or better in-plane thermal conduction than solid
aluminum.
21
However, through-the-thickness thermal conduction is limited by
the polymer matrix and is generally several orders of magnitude less than in-
plane conduction. As such, careful attention must be given to the design of
thermal attachments to ensure adequate thermal conduction across joints and
connections. Metallic inserts or coatings are commonly used for thermal load
distribution through-the-thickness of composite panels.
22
Electronics enclosures must provide radiation and electromagnetic shielding
to preserve and to protect the electronics within the housing. This requirement
has received the majority of attention because composites have much higher