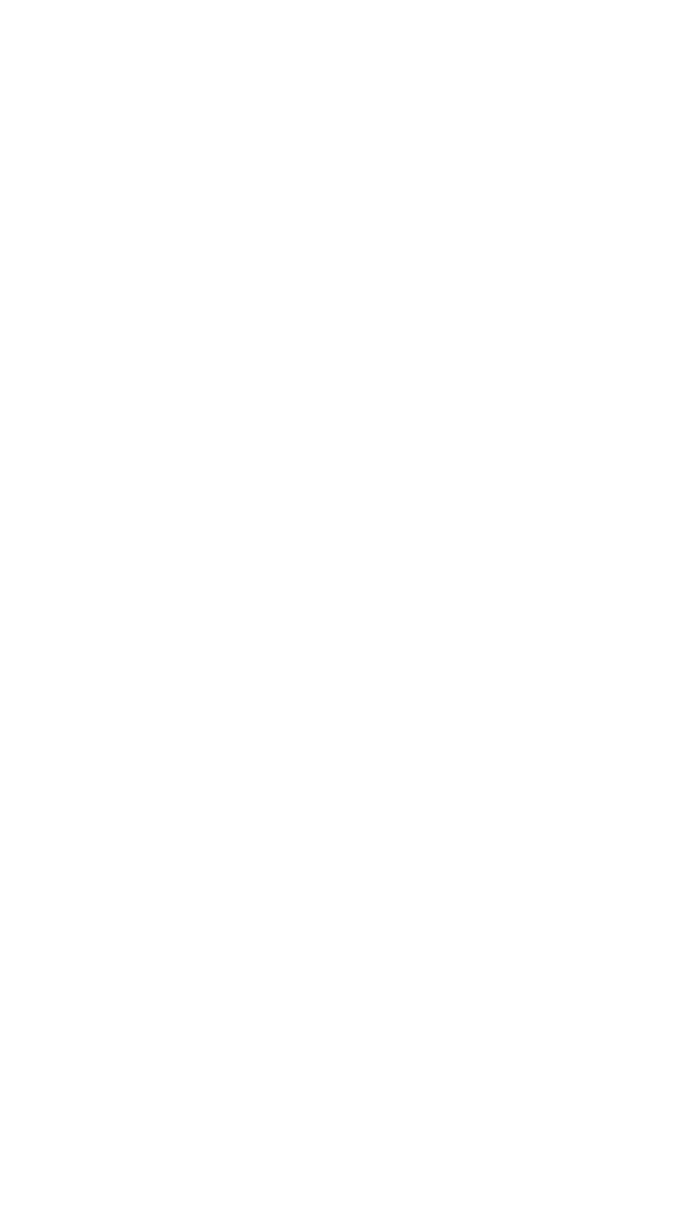
8 RESIN TRANSFER MOLDING 1083
sufficiently low, typically ⬍100 Pa/s, for the time interval necessary for full
infiltration to occur. The consequence of this is that gel time will normally need
to be at least double the infiltration time and that the time to demoulding will
be of the order of 5 times the infiltration time. The cure process may be speeded
up by the application of heat after the mold has been filled. Small molds may
be placed in an oven and large molds may be heated by radiant heaters or blown
hot air. With composite tooling the maximum cure temperature is unlikely to be
much more than 100
⬚C. If metal tools are used and buried heaters are used, the
molds may be heated directly to higher cure temperatures, typically 120–180
⬚C.
Electric cartridge heaters, circulating hot oil, and steam heating can be success-
fully used for mold heating. In general with thermoset resins the parts may be
ejected hot. To avoid having to cool the molds between cycles, it is advantageous
to keep them continuously at the cure temperature. The reinforcement is placed
into the hot, open mold, and after closure the resin is injected. The danger with
this system, especially if there are long flow paths, is that the resin should gel
before infiltration is complete. A further strategy is to preheat the resin to a
temperature lower than the cure temperature, e.g., 50–70
⬚C. This lowers its vis-
cosity allowing faster infiltration. Clearly great care must be exercised to for-
mulate the resin and control the temperatures so that full infiltration is ensured
and cure is achieved in the shortest reasonable time, so that productivity is
maximized.
8.3 Low-Pressure, Ambient Cure RTM
This is the longest established version of the process. In most cases two-part
matched tooling is used. For short runs composite molds are used, but the sup-
porting structure needs to be more robust than for ordinary contact molding.
According to the size and complexity of the part, the reinforcement is either laid
directly into the mold or a preform is separately made up and simply placed in
the open mold. The mold is then closed and the resin infiltrated into the rein-
forcement. There are several strategies for resin infiltration: The attraction of the
system is that very large moldings can be economically made this way with
relatively cheap and simple tooling. Using matched tools means that dimensions,
especially thickness, is more precisely defined and all surfaces are fair. A gel
coat may be used to enhance surface finish, or color, if required in the same
way as with contact molding. In large moldings, e.g., the hull of a 10-m sailing
yacht, the reinforcement is laid in the mold. This may take several days. A
variety of inserts, such as foamed sheet to form sandwich sections or timber
pads for reinforcing mounting points, may be incorporated into the reinforce-
ment. Pressure infiltration is not usually an option with large moldings but a
combination of preevacuation with gravity-assisted infiltration, i.e., maintaining
a hydrostatic head of resin, can be used.
For smaller moldings it is common to use preforms, as this reduces the length
of time that the molds are being prepared. Composite tooling is adequate for
short runs, but metal is preferred for larger numbers of moldings. The tools may
be mounted in a press, which facilitates opening and closing and also enables
the injection system to be permanently connected. Higher pressures may be used
and, since resin flow paths will be much shorter, infiltration time will be faster,
so that faster curing resins may be used with, consequently faster, mold turn-
around time. A combination of low pressure, 1–5 bars, with vacuum is typical.