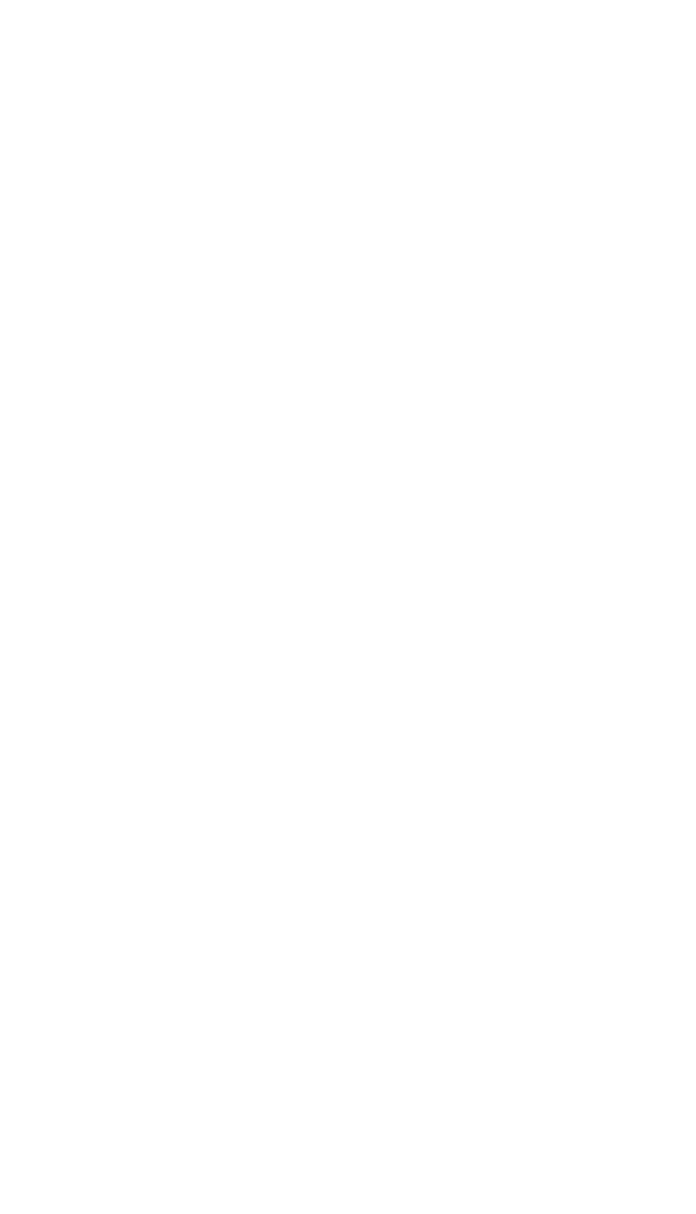
1050 COMPOSITES FABRICATION PROCESSES
results in a rise in temperature, referred to as the cure exotherm. A consequence
of this temperature rise is that the viscosity of the resin will be decreased, which
assists the processes of infiltration and consolidation. The next stage is gelation:
At this point the resin ceases to be liquid and transforms to a solid, initially it
is rubbery but then becomes progressively harder. The evolution of heat is gen-
erally most intense during the period around gelation. As the cure proceeds the
exotherm becomes weaker and the resin becomes fully hardened or vitrified.
Raising the initial cure temperature by heating will accelerate the cure process.
Gelation will occur sooner and the exotherm will be more intense. Care must
be exercised to ensure that the exothermic heat does not lead to the resin/
laminate becoming excessively hot so that degradation occurs. This is often
observed as burnt regions in the thicker sections of a molding where heat transfer
out of the laminate is less favorable. In extreme cases the molding can com-
pletely disintegrate, or even explode, as a result of excess exotherm! It is for-
tunate that the reinforcement, which does not participate in the reactions, acts
to some degree as an internal heat sink.
Three temperature, viscosity and cure profiles for a laminate cured at different
temperatures are shown in Figs. 7a,7b, and 7 c. Note how the time to gelation
is reduced by raising the cure temperature. For reasons of productivity it is
generally desirable to cure as fast as possible, provided excessive exotherm can
be controlled. However, it is also necessary that the resin is at low viscosity for
a sufficient time interval to allow any infiltration or consolidation processes to
be completed. This may be achieved by balancing the cure temperature profile
and the consolidation pressure.
Processing Thermoplastic Matrix Systems
Thermoplastics, with the exception of the monomer polymerization systems, are
not cured but are processed through melt–freeze cycles. Thermoplastics are ei-
ther amorphous or semicrystalline, with degrees of crystallinity of up to about
75%. On heating to above the melting temperature, T
m
, amorphous polymers
soften over a range of temperatures while the semicrystalline materials melt more
sharply and generally to melts of lower viscosity. Overheating leads to degra-
dation, discoloration, and loss of properties. On cooling back through the freez-
ing temperature, the amorphous materials become gradually more rigid, but the
semicrystalline polymers freeze more sharply and recrystallize. The extent of
crystallinity is dependent on the rate of cooling through the critical region. Fast
cooling leads to a fine substructure but lower overall crystallinity, while slow
cooling has the converse effect. In most cases optimum mechanical performance
of the composite requires that the crystallite size and degree of crystallinity be
controlled. It is therefore necessary to exercise control over cooling rates when
processing thermoplastic systems. A further property of amorphous thermoplas-
tics is the glass transition temperature, T
g
. This transition occurs below the
melting point and at T
⬍ T
g
the polymer behaves as a glass. It is hard, often
brittle, and does not creep significantly under load. At T
⬎ T
g
the polymer is
rubbery and much softer, extendible, and creeps under load. The temperature T
g
effectively defines the upper service temperature for amorphous thermoplastics.
In the case of the semicrystalline thermoplastics only the amorphous portion is
affected by T
g
, so the effect is less severe. Semicrystalline polymers therefore
have higher useful service temperatures and in the temperature interval between