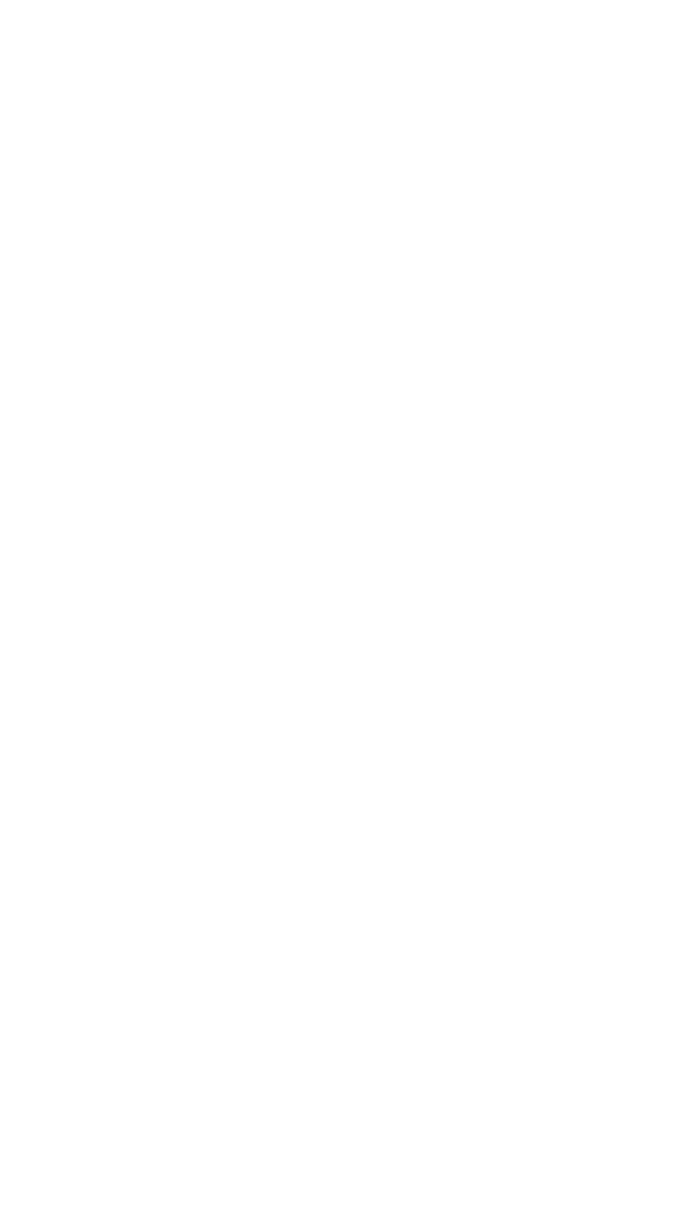
9 MELT INJECTION MOLDING 1023
A complete analytical solution to the plaque filling step was obtained by
dividing the problem into (i) diverging flow in a cylindrical wedge for the fan
gate and initial entry into the plaque cavity, followed by (ii) rectangular flow
between parallel plates for the remainder of the cavity. The resulting velocity
profiles were necessary to determine the shear rate profiles, from which the
viscosities were specified.
Richard’s
50
primary interest was in comparing destructive and nondestructive
properties of the parts in order that the latter might be used instead of the former.
Plaque volume and weight revealed ‘‘global’’ variations in density, part to part.
Optical birefringence revealed local variations within each part due to process
orientation. The attempt to use dielectric properties was unsuccessful because
the electrodes were the same size as the plaque; hence, no detail ‘‘within a part’’
could be obtained.
In preparation for further experimental studies, Moore
51
and Hudson
52
deter-
mined the rheological properties of a single lot of high-density polyethylene
(HDPE). O’Nan
10
used these data to compare the ability of various shear vis-
cosity models to describe the shear rate and temperature dependencies. Peter-
son
53
contributed additional data and correlations using the Arrhenius equation.
Taghizadegan
54
then carried out an extensive experimental study of the ASTM
plaque and tensile bar mold used in the Richards dissertation with the HDPE
characterized by Moore,
51
Hudson,
52
and Peterson.
53
Utilizing a ‘‘composite de-
sign’’ with 16 treatment combinations—eight corners of a cube plus six star
points and a replicated center point—response surface analysis of the data
yielded equations that related processing conditions to part thickness as well as
tensile and impact strength. Then, computer simulations demonstrated the po-
tential effectiveness of employing statistical process control (SPC) as part of a
feedback loop to decrease part-to-part variations. This was an extension of prior
work by the team of Wright,
55
Ralston et al.,
56
Stoll, and Harper. Lee
57
continued
the application of SPC by using the correlations discovered by Taghizadegan.
Henz
58
simulated the cooling phase of the injection-molding process and ver-
ified the model experimentally. He used a finite-element program called C-
COOL, developed by AC Technology of Ithaca, New York (now dba Mold-Flow,
Louisville, Kentucky), to predict the cooling of a rectangular plaque,
21
⫻ 11 ⫻ 0.1 in. The experimental phase used polystyrene and 20% talc-filled
polypropylene. Henz concluded that the predicted temperature distribution in the
part was within 10% of the measured values. The wall temperatures of the mold
were less accurately predicted; he attributed this to some imperfect assumptions
in the software that ‘‘should be . . . easy to remedy.’’
Barbarito
59
showed that the hold pressure affected the impact strength of
thermally aged polycarbonate plaques. Notched Izod specimens were aged in a
silicone oil bath at 110
⬚C, and slow cooled them before testing. For a lower hold
pressure of 250 psi, the ductile-to-brittle transition ran from 10 to 29 min,
whereas, for a higher hold pressure of 1000 psi, this transition was delayed as
long as 40 min. The average transition times were 15.3 and 16.2 min for the
low and high values, respectively.
In Section 3 the work of Cecil
42
was cited to point out that reprocessing
material, as in the pelletizing and reuse of the sprue and runners, can affect the
properties of the final parts. Experimental studies with total recycling of molded
parts are often used to determine the percentage of acceptable regrind. That is: