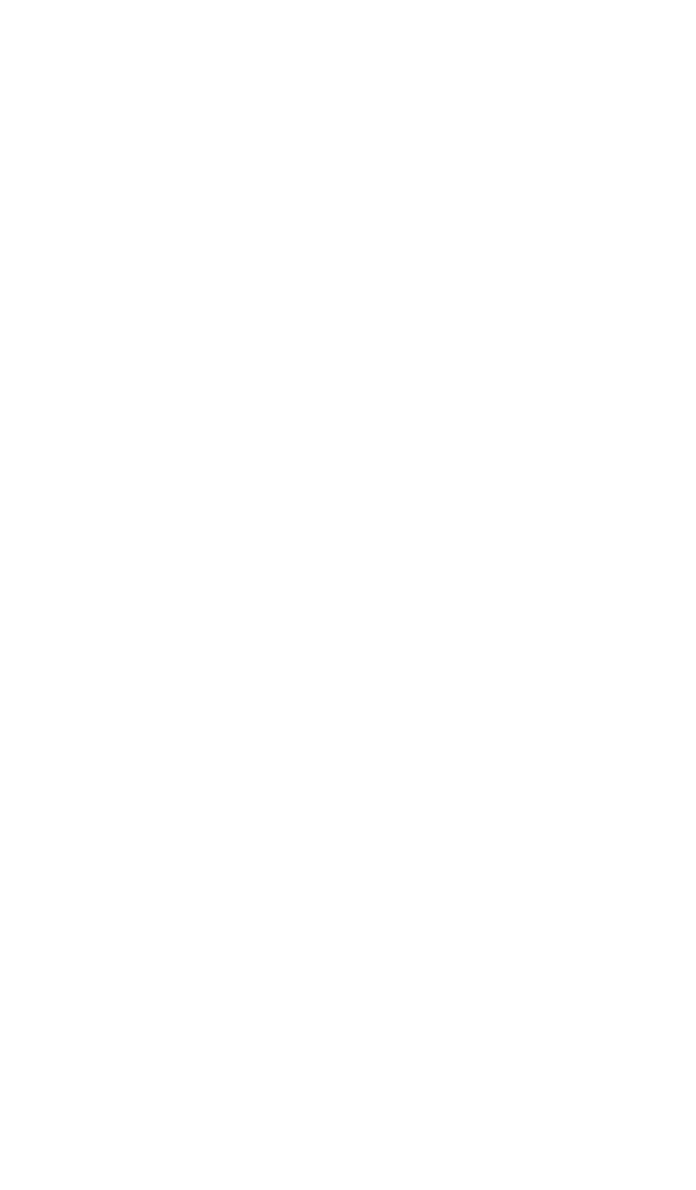
4 EXTRUSION: TWIN SCREW 1015
annulus, and a rectangular conduit. Three different thermal conditions were
considered: isothermal, constant wall temperature, and adiabatic. The density,
thermal conductivity, overall heat transfer coefficient, low-shear-rate-limiting
viscosity, as well as the Carreau parameter, may be temperature dependent.
These programs solve for the velocity and (for the nonisothermal cases) tem-
perature profiles.
Ishmael
41
has modeled the postextrusion cooling and freezing process as the
extruded melt is turned into a solid rod and chopped into pellets. The successive
heat transfers are from the extrudate to (i) air, (ii) water, (iii) air, (iv) puller-
rollers, and (v) air; this sequence is followed by the pelletizer. Required data
include the polymer density, viscosity, thermal conductivity, heat capacity, and
thermal expansion, each as a function of temperature.
The model predicts the length of the water bath, the final temperature, and
the final inner and outer diameters of the extruded strands. These strands are
hollow because the outer surface is frozen first, and subsequent cooling and
contraction creates a vacuum on the inside. The model is applicable to crystalline
and amorphous polymers; it was confirmed by industrial experiments with iso-
tactic and atactic polypropylene. Although Ishmael
41
used spreadsheet software,
the equations are given and permit one to use an alternative means of calculation.
Cecil
42
showed that repeated processing, as experienced by ‘‘regrind’’—
otherwise scrap material chopped into pellets and sent back to be reextruded—
in the feed, affected the color stability of extruded parts. (Reprocessing also
occurs in injection molding, vide infra.) Cecil measured the yellowness index
(YI) of five grades of polypropylene, without and with various additives, sub-
jected to two or five additional passes through an extruder. The results showed
that: (1) repeated processing increased the YI; (2) small amounts of antioxi-
dant—0.10% for two additional ‘‘cycles’’ and 0.05% for five—reduced the YI,
but larger amounts increased it; (4) other changes in the recipe, such as the
inclusion of a filler deactivator, a secondary stabilizer, and/or pigment, also had
an affect on YI.
4 EXTRUSION: TWIN SCREW
Twin-screw extruders are constructed in a variety of ways: they may be co-
rotating (in the same clockwise or counterclockwise direction) or counterrotating
(opposite directions); they may be nonintermeshing (which means that looking
in the axial direction, the flights of the two screws never overlap), partially
intermeshing, or fully intermeshing. (The book by Janssen, cited in the bibli-
ography, shows examples of these configurations on pp. 6–9; the book by Mar-
telli, also cited in the bibliography, has a more complete classification scheme
on pp. 9–12.)
Tolliver
43
successfully modeled a vented nonintermeshing counterrotating
twin-screw extruder used for the final polymerization of an industrial polymer.
The screws were 6 in. in diameter and 50 ft. long, followed by a short single
screw that produced the extrudate. His FORTRAN program requires knowledge
of (a) the type of element, its flight land width, its volume, and its cross-sectional
area, (b) the screw geometry data (barrel diameter, flight clearance, and helical
angle), and (c) locations of the heating zones. ‘‘Rework and additive ports are
defined in separate [program] statements.’’