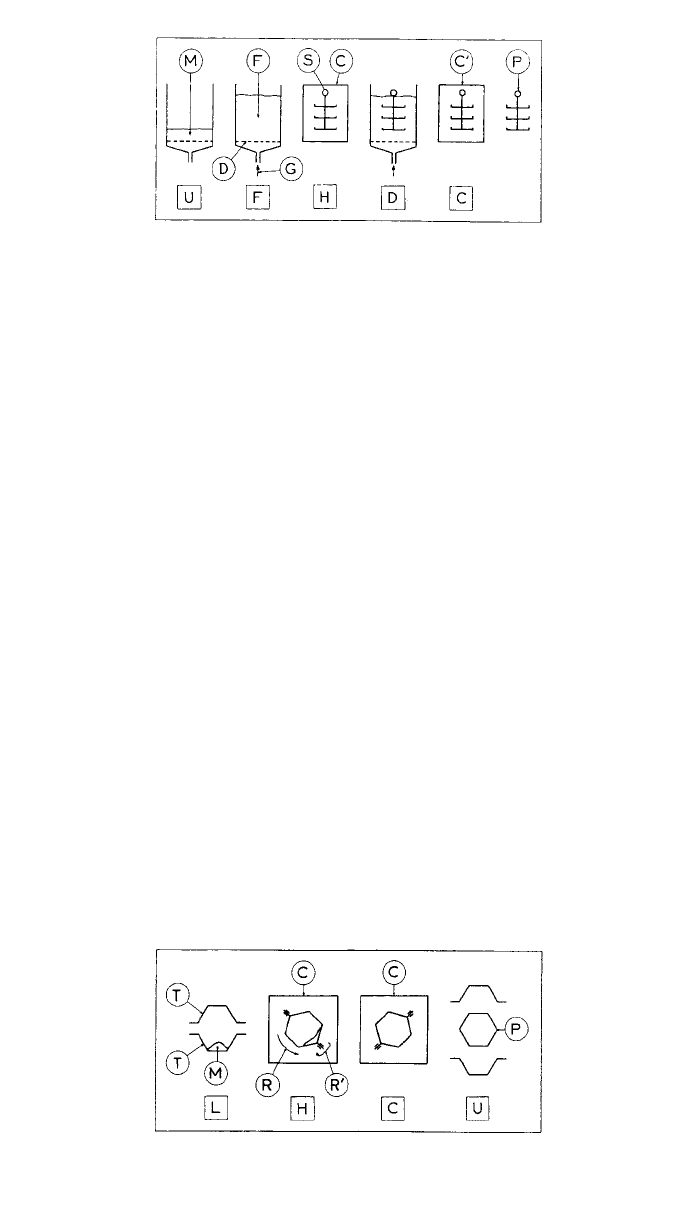
9 ROTATIONAL MOLDING 981
Fig. 18 Fluidized-bed dip coating: , unfluidized bed; , fluidized bed; , substrate heating;UFH
䡺䡺䡺
, dipping; , conditioning; M, powdered coating material; F, fluidized particles; D, porousDC
䡺䡺
diaphragm; G, gas inlet; S, substrate; C, heating chamber; C⬘, conditioning chamber;
P, product. (From Charrier, J.-M., Polymeric Materials and Processing: Plastics, Elastomers
and Composites, Hanser Publishers, Munich, 1990.)
Fig. 19 Rotational molding process: , loading; , heating; , cooling; , unloading; T, T⬘,LHCU
䡺䡺䡺䡺
mold halves; M, material charge; R, R⬘, axes of rotation; C, conditioning chamber; P, product.
(From Charrier, J.-M., Polymeric Materials and Processing: Plastics, Elastomers
and Composites, Hanser Publishers, Munich, 1990.)
mold (mold halves T and T⬘). The mold is then closed and mounted on a holding
device, which permits its double, biaxial, rotation around two perpendicular axes
(R and R
⬘) to produce a tumbling action. A heating stage follows in whichH
䡺
the exterior of the mold is subjected to a high temperature in a suitable chamber,
while being roasted. Heat transfer through the mold wall eventually raises the
temperature of the inner mold surface to a level sufficient to cause superficial
melting of the thermoplastic particles and their sticking to the mold surface.
Equipment
The mold-handling device, which is capable of imparting double rotation, is the
central element of rotational molding equipment. There are two major types of
equipment: (1) the ‘‘shuttle cart system’’ and (2) the ‘‘swing/rotary arm system.’’
The shuttle cart system, shown in Fig. 20, features a cart (wagon), incorporating
the mold rotation device, which can be rolled in and out of the heating or cooling
chamber (bay). The swing/rotary arm system, illustrated in Fig. 21, features
arms or spindles that rotate in a horizontal plane around a hub.
Tooling
Molds for rotational molding are normally split (two-half, two-piece) negative
molds, with built-in mechanical locking. The need for rapid heat transfer, and
minimum weight to facilitate rotation, calls for relatively thin walls, which are
acceptable in view of the low pressures involved. Large molds are generally