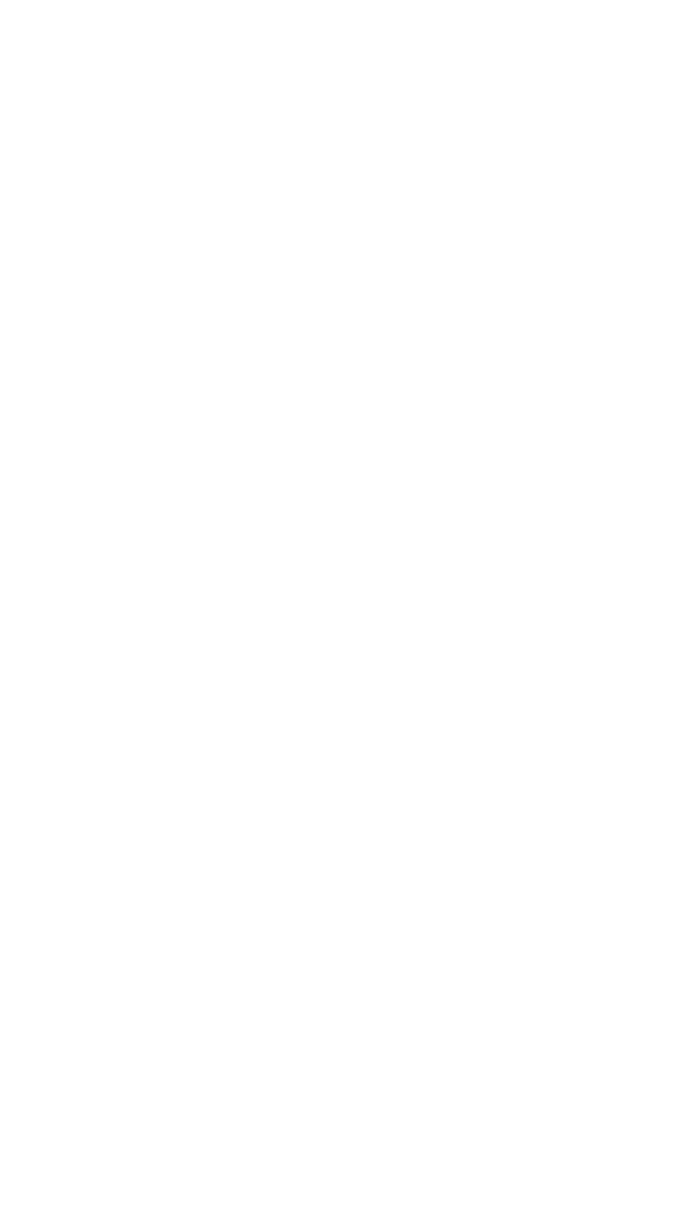
6 POWDER METALLURGY 959
6 POWDER METALLURGY
In powder metallurgy (P/M), fine metal powders are pressed into a desired
shape, usually in a metal die and under high pressure, and the compacted powder
is then heated (sintered), with a protective atmosphere. The density of sintered
compacts may be increased by repressing. Repressing is also performed to im-
prove the dimensional accuracy, either concurrently or subsequently, for a period
of time at a temperature below the melting point of the major constituent. P/M
has a number of distinct advantages that account for its rapid growth in recent
years, including (1) no material is wasted, (2) usually no machining is required,
(3) only semiskilled labor is required, and (4) some unique properties can be
obtained, such as controlled degrees of porosity and built-in lubrication.
A crude form of powder metallurgy appears to have existed in Egypt as early
as 3000
BC
, using particles of sponge iron. In the nineteenth century, P/M was
used for producing platinum and tungsten wires. However, its first significant
use related to general manufacturing was in Germany, following World War I,
for making tungsten carbide cutting-tool tips. Since 1945 the process has been
highly developed, and large quantities of a wide variety of P/M products are
made annually, many of which could not be made by any other process. Most
are under 2 in. (50.8 mm) in size, but many are larger, some weighing up to 50
lb (22.7 kg) and measuring up to 20 in. (508 mm).
Powder metallurgy normally consists of four basic steps:
1. Producing a fine metallic powder
2. Mixing and preparing the powder for use
3. Pressing the powder into the desired shape
4. Heating (sintering) the shape at an elevated temperature
Other operations can be added to obtain special results.
The pressing and sintering operations are of special importance. The pressing
and repressing greatly affect the density of the product, which has a direct re-
lationship to the strength properties. Sintering strips contaminants from the sur-
face of the powder particles, permitting diffusion bonding to occur and resulting
in a single piece of material. Sintering usually is done in a controlled, inert
atmosphere, but sometimes it is done by the discharge of spark through the
powder while it is under compaction in the mold.
6.1 Properties of P/M Products
Because the strength properties of powder metallurgy products depend on so
many variables—type and size of powder, pressing pressure, sintering temper-
ature, finishing treatments, and so on—it is difficult to give generalized infor-
mation. In general, the strength properties of products that are made from pure
metals (unalloyed) are about the same as those made from the same wrought
metals. As alloying elements are added, the resulting strength properties of P/
M products fall below those of wrought products by varying, but usually sub-
stantial, amounts. The ductility usually is markedly less, as might be expected
because of the lower density. However, tensile strengths of 40,000–50,000 psi
(275.8–344.8 MPa) are common, and strengths above 100,000 psi (689.5 MPa)
can be obtained. As larger presses and forging combined with P/M preforms