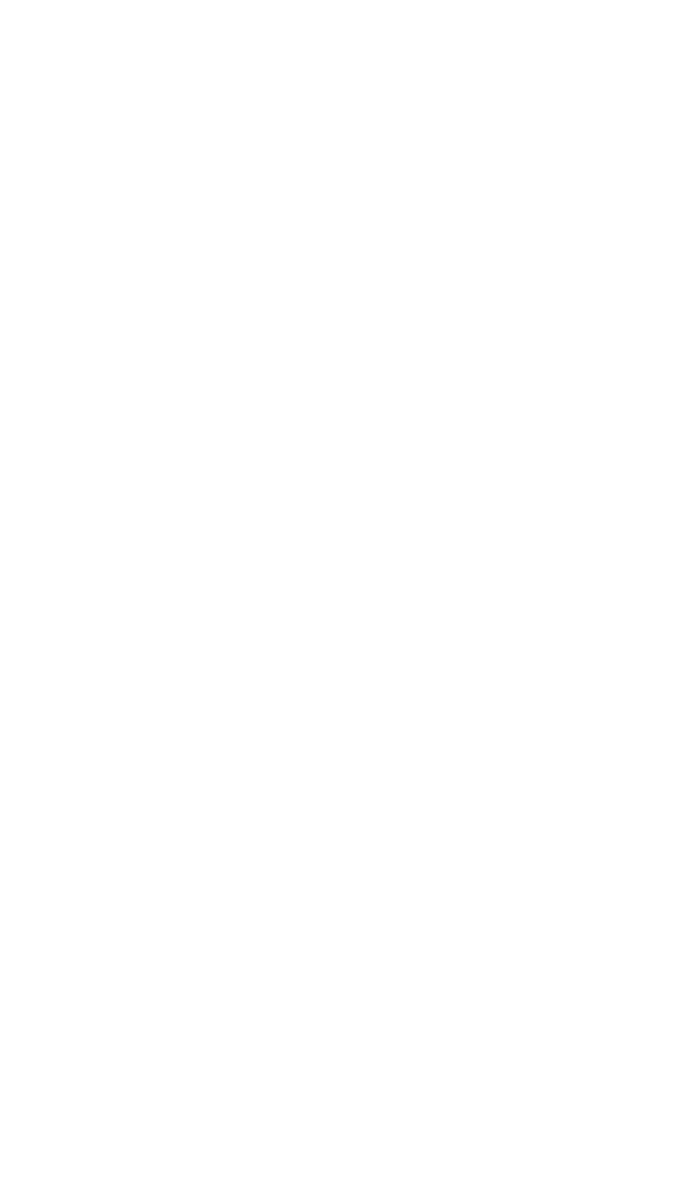
1 INTRODUCTION 1043
at least one month. However, many require them to be stored at subzero tem-
peratures, typically
⫺15⬚C, when they have a storage life of up to one year. This
complicates the logistics of processing and inevitably adds to the costs.
Compounded reinforcements are available as impregnated tows or rovings, as
preimpregnated warp sheet, or prepreg, preimpregnated woven fabrics and mats,
and preimpregnated random fiber compounds such as sheet molding compound
(SMC) and bulk molding compound (BMC). The processing principles are com-
mon. The material contains all the fiber and resin (possibly an excess) for man-
ufacture of the component. After assembly by laying tows or laminating sheet
forms, the material is subjected to heat and pressure. First the resin softens,
allowing consolidation, elimination of trapped gases, and any resin excess, then
the resin cures to form the solid part. In some cases, e.g., prepreg, which is
comprised of continuous fibers, no lateral flow of the fibers can occur. So the
plies have to be precisely tailored to the shape of the part. In other processes,
e.g., SMC, there is considerable flow of both resin and fiber so that complex
shapes including stiffening ribs and other features may be formed from blanks
of simple shapes. Prepreg consists of a uniaxial array of continuous fibers pro-
duced as a continuous roll up to about 2 m in width. The resin is applied to the
web of fiber and the compounded material then consolidated between two rolls
of protective film. One is usually a silicone-coated paper and the other a poly-
olefin film. The finished standard prepreg has an areal density of 100–200 g/
m
2
and when cured is designed to have a thickness of 0.125 mm per ply. Thus
8 plies are required to form a laminate 1 mm thick. While this would be in-
convenient for the manufacture of thick structures, it does allow very precise
tailoring of the laminate properties by varying the lay-up sequence. A quasi-
isotropic laminate may be formed by the 8-ply sequence [0
⬚, Ⳳ45⬚,90⬚]
s
, the
subscript ‘‘s’’ indicating symmetric. Alternative sequences, usually symmetric,
give a different balance of longitudinal, transverse and in-plane shear properties.
Prepreg is also manufactured in thinner formats and also using fine woven fabrics
of plain or satin weave which typically laminate to 0.25 mm/ply.
There has recently been much interest in developing prepreg-like materials
more suitable for manufacturing thick laminates. These are based on combina-
tions of woven and noncrimp fabrics and mats, impregnated with suitable ther-
mosetting resins, usually vinyl-ester or epoxies. Areal densities exceeding 6000
g/m
2
have been produced. The same problems of handling and shelf life apply
but, outside the aerospace industry, subzero storage is seldom acceptable and
shelf lives exceeding 3 months are demanded. This limits the range of resin
systems but satisfactory systems are now available. A concern with all precom-
pounded materials is the degree of tack or stickiness. Too little tack means that
lamina do not stay in place as the laminate is laid up. Too much tack renders
the material difficult to handle as it sticks to everything it contacts. Aerospace
prepregs are manufactured to a precisely controlled tack, but even this tends to
lessen as the material approaches the end of its shelf life. A technique recently
introduced for heavier reinforcements is to make a multiple layer material but
to confine the resin impregnation to the central layers, shown in Fig. 4. Such a
material handles like a dry reinforcement, although it tends to be much less
springy; when subjected to heat and pressure, the resin content softens to a low
viscosity and flows uniformly throughout the reinforcement. Developments such