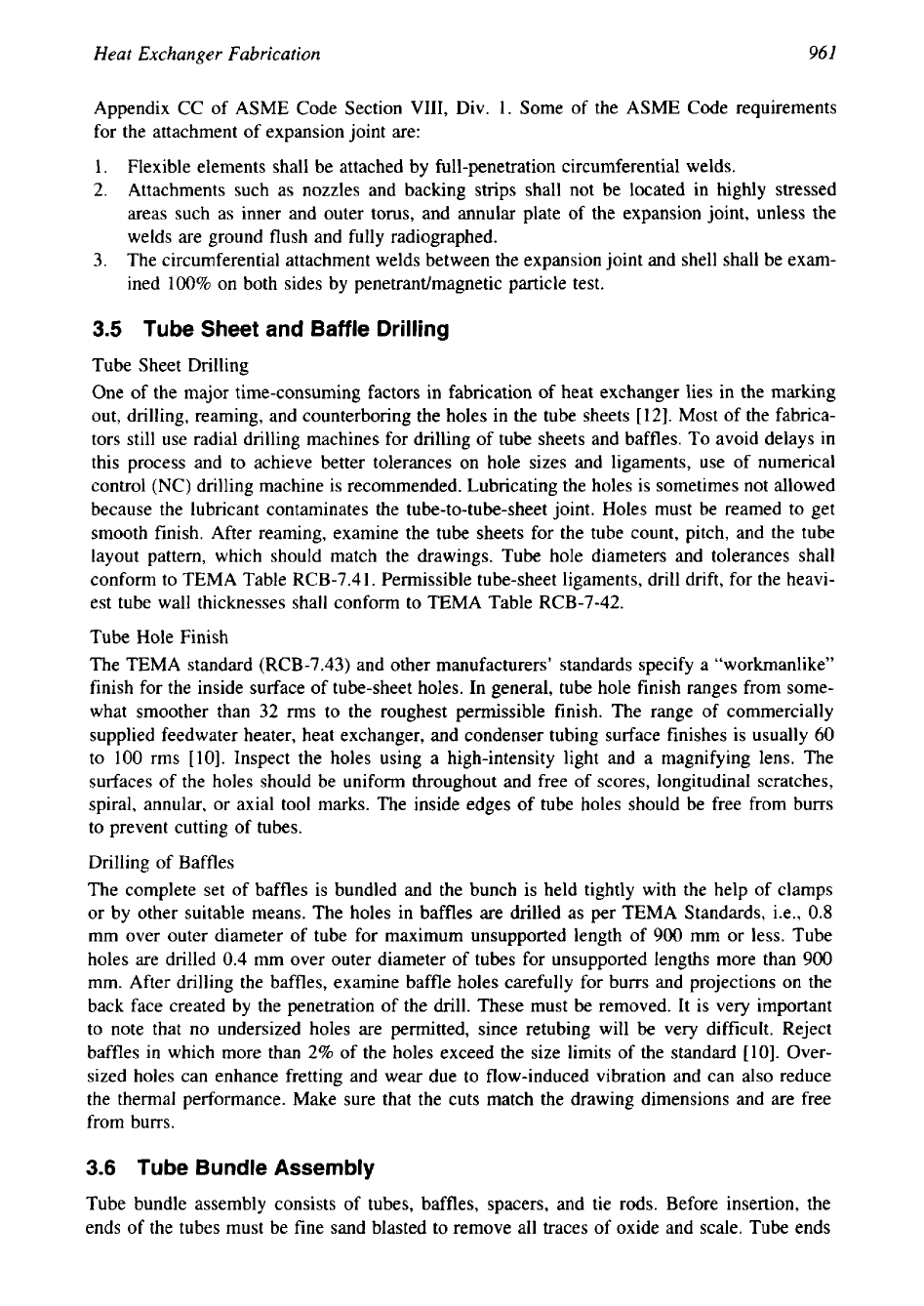
Heat Exchanger Fabrication
961
Appendix CC of ASME Code Section VIII, Div. 1. Some of the ASME Code requirements
for the attachment of expansion joint are:
1.
Flexible elements shall be attached by full-penetration circumferential welds.
2.
Attachments such as nozzles and backing strips shall not be located in highly stressed
areas such as inner and outer torus, and annular plate of the expansion joint, unless the
welds are ground flush and fully radiographed.
3.
The circumferential attachment welds between the expansion joint and shell shall be exam-
ined
100%
on both sides by penetranumagnetic particle test.
3.5
Tube Sheet and Baffle Drilling
Tube Sheet Drilling
One of the major time-consuming factors in fabrication of heat exchanger lies in the marking
out, drilling, reaming, and counterboring the holes in the tube sheets
[12].
Most of the fabrica-
tors still use radial drilling machines for drilling of tube sheets and baffles. To avoid delays in
this process and
to
achieve better tolerances on hole sizes and ligaments, use of numerical
control
(NC)
drilling machine is recommended. Lubricating the holes is sometimes not allowed
because the lubricant contaminates the tube-to-tube-sheet joint. Holes must be reamed to get
smooth finish. After reaming, examine the tube sheets for the tube count, pitch, and the tube
layout pattern, which should match the drawings. Tube hole diameters and tolerances shall
conform to TEMA Table RCB-7.41. Permissible tube-sheet ligaments, drill drift, for the heavi-
est tube wall thicknesses shall conform to TEMA Table RCB-7-42.
Tube Hole Finish
The TEMA standard (RCB-7.43) and other manufacturers’ standards specify a “workmanlike”
finish for the inside surface of tube-sheet holes. In general, tube hole finish ranges from some-
what smoother than
32
rms to the roughest permissible finish. The range of commercially
supplied feedwater heater, heat exchanger, and condenser tubing surface finishes is usually
60
to 100
rms
[lO].
Inspect the holes using a high-intensity light and a magnifying lens. The
surfaces of the holes should be uniform throughout and free of scores, longitudinal scratches,
spiral, annular, or axial tool marks. The inside edges of tube holes should be free from burrs
to prevent cutting of tubes.
Drilling of Baffles
The complete set of baffles is bundled and the bunch is held tightly with the help of clamps
or by other suitable means. The holes in baffles are drilled as per TEMA Standards, i.e.,
0.8
mm over outer diameter of tube for maximum unsupported length of
900
mm or less. Tube
holes are drilled 0.4
mm
over outer diameter of tubes for unsupported lengths more than
900
mm. After drilling the baffles, examine baffle holes carefully for burrs and projections on the
back face created by the penetration of the drill. These must be removed. It is very important
to note that no undersized holes are permitted, since retubing will be very difficult. Reject
baffles in which more than 2% of the holes exceed the size limits of the standard [lO]. Over-
sized holes can enhance fretting and wear due to flow-induced vibration and can also reduce
the thermal performance. Make sure that the cuts match the drawing dimensions and are free
from burrs.
3.6
Tube Bundle Assembly
Tube bundle assembly consists of tubes, baffles, spacers, and tie rods. Before insertion, the
ends of the tubes must be fine sand blasted to remove all traces of oxide and scale. Tube ends