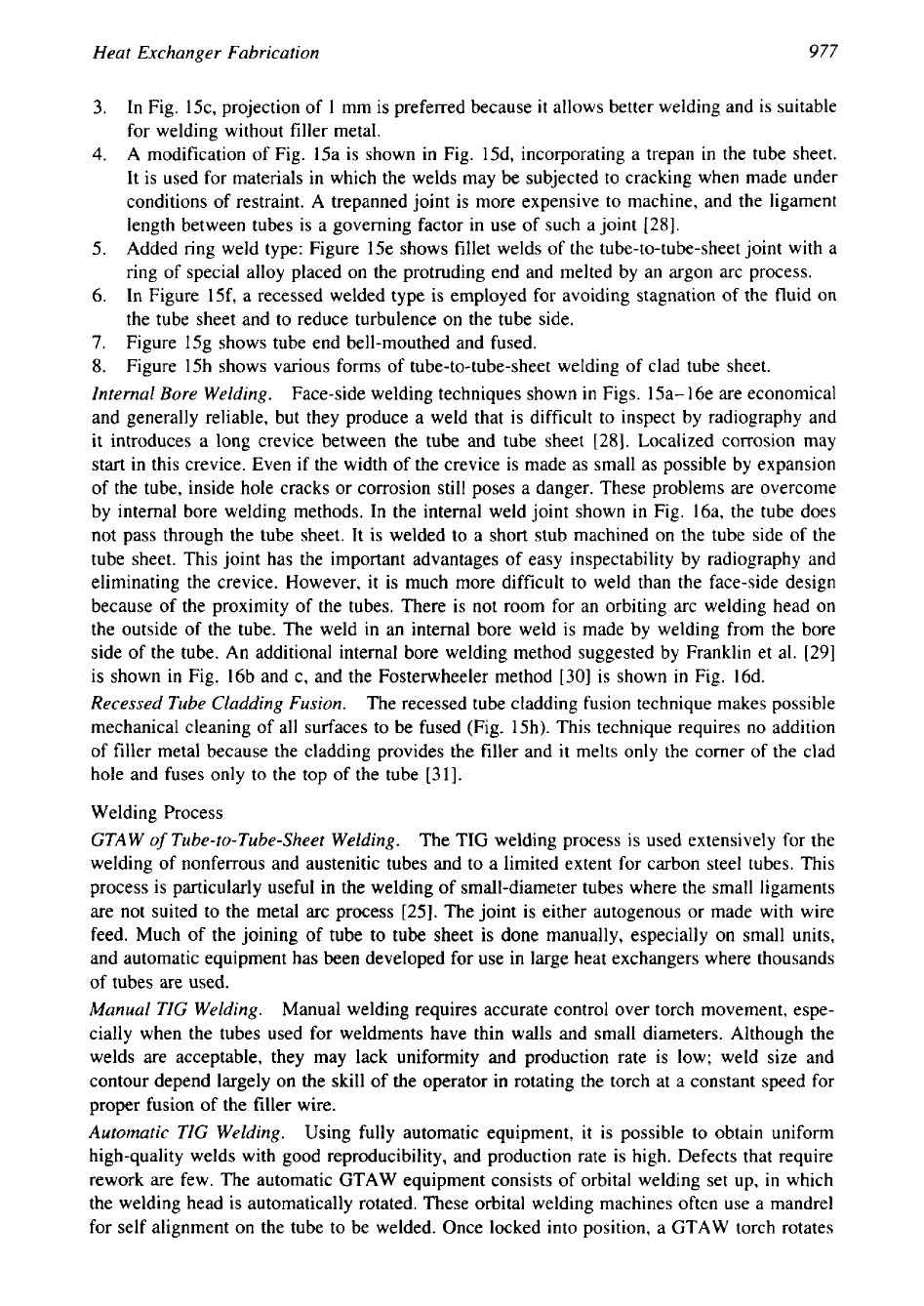
977
Heat Exchanger Fabrication
3.
In Fig. 15c, projection of
1
mm is preferred because
it
allows better welding and is suitable
for welding without filler metal.
4.
A modification of Fig. 15a is shown in Fig. 15d, incorporating a trepan in the tube sheet.
It is used for materials in which the welds may be subjected to cracking when made under
conditions of restraint. A trepanned joint is more expensive to machine, and the ligament
length between tubes is a governing factor in use of such a joint
[28].
5.
Added ring weld type: Figure 15e shows fillet welds of the tube-to-tube-sheet joint with a
ring of special alloy placed on the protruding end and melted by an argon arc process.
6.
In Figure 15f, a recessed welded type is employed for avoiding stagnation of the fluid on
the tube sheet and to reduce turbulence on the tube side.
7.
Figure 15g shows tube end bell-mouthed and fused.
8.
Figure 15h shows various forms of tube-to-tube-sheet welding of clad tube sheet.
Internal
Bore
Welding.
Face-side welding techniques shown
in
Figs. 15a- 16e are economical
and generally reliable, but they produce a weld that is difficult to inspect by radiography and
it introduces a long crevice between the tube and tube sheet
[28].
Localized corrosion may
start in this crevice. Even if the width of the crevice is made as small as possible by expansion
of the tube, inside hole cracks or corrosion still poses a danger. These problems are overcome
by internal bore welding methods. In the internal weld joint shown
in
Fig. 16a, the tube does
not pass through the tube sheet. It is welded to a short stub machined on the tube side of the
tube sheet. This joint has the important advantages of easy inspectability by radiography and
eliminating the crevice. However, it is much more difficult to weld than the face-side design
because of the proximity of the tubes. There is not room for an orbiting arc welding head on
the outside of the tube. The weld in an internal bore weld is made by welding from the bore
side of the tube. An additional internal bore welding method suggested by Franklin et al.
[29]
is shown in Fig. 16b and c, and the Fosterwheeler method
[30]
is shown
in
Fig. 16d.
Recessed Tube Cladding Fusion.
The recessed tube cladding fusion technique makes possible
mechanical cleaning of all surfaces to be fused (Fig. 15h). This technique requires no addition
of filler metal because the cladding provides the filler and it melts only the corner of the clad
hole and fuses only to the top
of
the tube
[31].
Welding Process
GTAW
of
Tube-to-Tube-Sheet Welding.
The TIG welding process is used extensively for the
welding of nonferrous and austenitic tubes and to a limited extent for carbon steel tubes. This
process is particularly useful in the welding of small-diameter tubes where the small ligaments
are not suited to the metal arc process
[25].
The joint is either autogenous or made with wire
feed. Much of the joining
of
tube to tube sheet is done manually, especially on small units,
and automatic equipment has been developed for use in large heat exchangers where thousands
of tubes are used.
Manual TIG Welding.
Manual welding requires accurate control over torch movement, espe-
cially when the tubes used for weldments have thin walls and small diameters. Although the
welds are acceptable, they may lack uniformity and production rate is low; weld size and
contour depend largely on the
skill
of the operator in rotating the torch at a constant speed for
proper fusion of the filler wire.
Automatic TIG Welding.
Using fully automatic equipment, it is possible to obtain uniform
high-quality welds with good reproducibility, and production rate is high. Defects that require
rework are few. The automatic GTAW equipment consists of orbital welding set up, in which
the welding head is automatically rotated. These orbital welding machines often use a mandrel
for self alignment on the tube to be welded. Once locked into position, a GTAW torch rotates