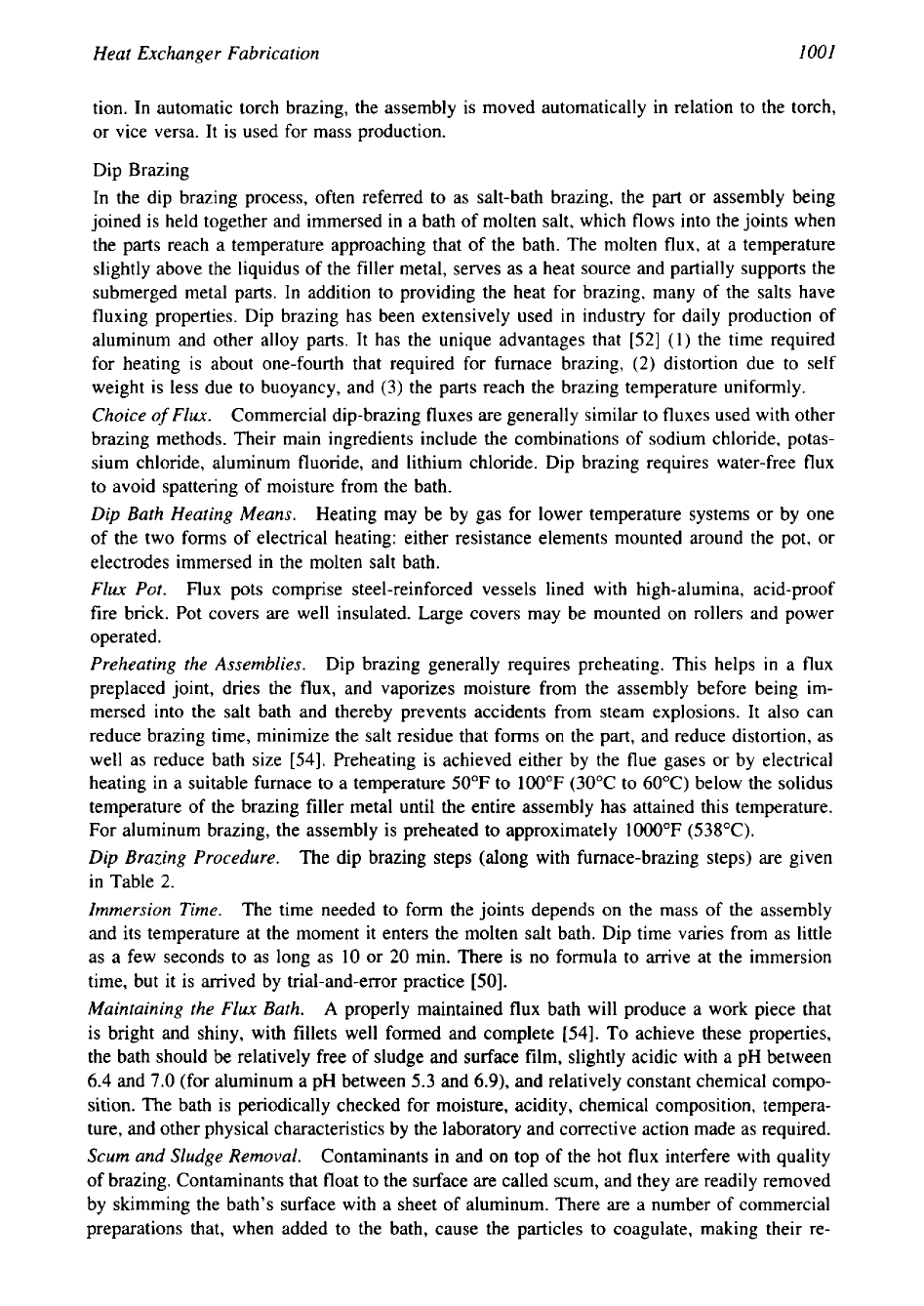
1001
Heat Exchanger Fabrication
tion. In automatic torch brazing, the assembly is moved automatically in relation to the torch,
or vice versa. It is used for mass production.
Dip Brazing
In the dip brazing process, often referred to as salt-bath brazing, the part or assembly being
joined is held together and immersed in a bath of molten salt, which flows into the joints when
the parts reach a temperature approaching that of the bath. The molten
flux,
at a temperature
slightly above the liquidus of the filler metal, serves as a heat source and partially supports the
submerged metal parts. In addition to providing the heat for brazing, many of the salts have
fluxing properties. Dip brazing has been extensively used in industry for daily production of
aluminum and other alloy parts. It has the unique advantages that
[52]
(1)
the time required
for heating is about one-fourth that required for furnace brazing,
(2)
distortion due to self
weight is less due to buoyancy, and
(3)
the parts reach the brazing temperature uniformly.
Choice
of
Flux.
Commercial dip-brazing fluxes are generally similar to fluxes used with other
brazing methods. Their main ingredients include the combinations of sodium chloride, potas-
sium chloride, aluminum fluoride, and lithium chloride. Dip brazing requires water-free flux
to avoid spattering of moisture from the bath.
Dip Bath Heating Means.
Heating may be by gas for lower temperature systems or by one
of the two forms of electrical heating: either resistance elements mounted around the pot, or
electrodes immersed in the molten salt bath.
Flux Pot.
Flux pots comprise steel-reinforced vessels lined with high-alumina, acid-proof
fire brick. Pot covers are well insulated. Large covers may be mounted on rollers and power
operated.
Preheating the Assemblies.
Dip brazing generally requires preheating. This helps in a flux
preplaced joint, dries the flux, and vaporizes moisture from the assembly before being im-
mersed into the salt bath and thereby prevents accidents from steam explosions. It also can
reduce brazing time, minimize the salt residue that forms on the part, and reduce distortion, as
well as reduce bath size
[54].
Preheating is achieved either by the flue gases or by electrical
heating in a suitable furnace to a temperature
50°F
to
100°F
(30°C
to
60°C)
below the solidus
temperature of the brazing filler metal until the entire assembly has attained this temperature.
For aluminum brazing, the assembly is preheated to approximately
1000°F
(538°C).
Dip Brazing Procedure.
The dip brazing steps (along with furnace-brazing steps) are given
in Table
2.
Immersion Time.
The time needed to form the joints depends on the mass of the assembly
and its temperature at the moment it enters the molten salt bath. Dip time varies from as little
as a few seconds to as long as
10
or
20
min. There is
no
formula to arrive at the immersion
time, but it is arrived by trial-and-error practice
[50].
Maintaining the Flux Bath.
A
properly maintained flux bath will produce a work piece that
is bright and shiny, with fillets well formed and complete
[54].
To achieve these properties,
the bath should be relatively free of sludge and surface film, slightly acidic with a pH between
6.4
and
7.0
(for aluminum a pH between
5.3
and
6.9),
and relatively constant chemical compo-
sition. The bath is periodically checked for moisture, acidity, chemical composition, tempera-
ture, and other physical characteristics by the laboratory and corrective action made as required.
Scum and Sludge Removal.
Contaminants in and on top of the hot flux interfere with quality
of brazing. Contaminants that float to the surface are called scum, and they are readily removed
by skimming the bath’s surface with a sheet of aluminum. There are a number of commercial
preparations that, when added to the bath, cause the particles to coagulate, making their re-