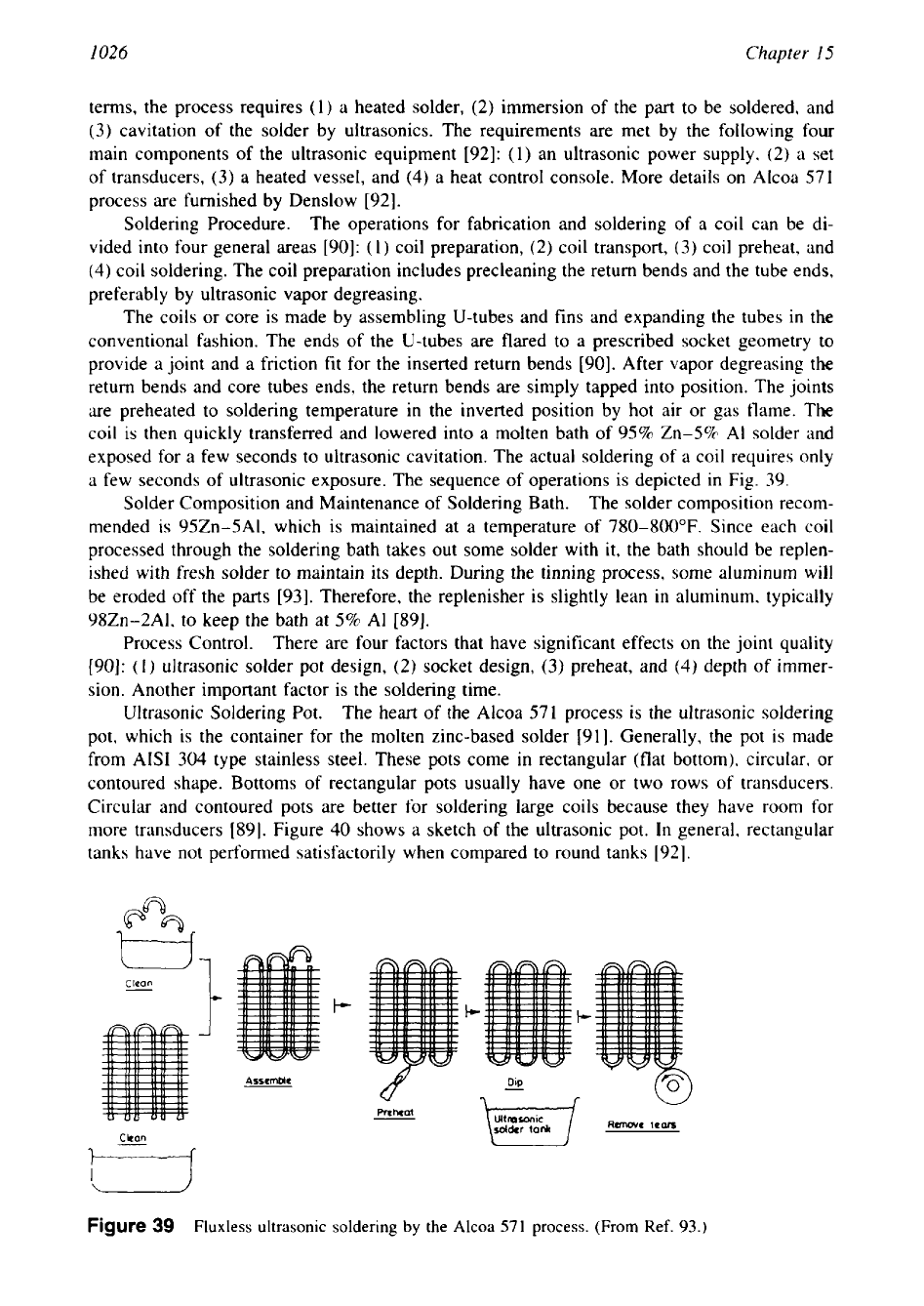
1026
Chapter
15
terms, the process requires
(I)
a heated solder,
(2)
immersion of the part to be soldered, and
(3) cavitation of the solder by ultrasonics. The requirements are met by the following four
main components of the ultrasonic equipment [92]:
(1)
an ultrasonic power supply, (2) a set
of transducers, (3) a heated vessel, and (4) a heat control console. More details on Alcoa 571
process are furnished by Denslow [92].
Soldering Procedure. The operations for fabrication and soldering of a coil can be di-
vided into four general areas
[90]:
(1)
coil preparation, (2) coil transport, (3) coil preheat, and
(4)
coil soldering. The coil preparation includes precleaning the return bends and the tube ends,
preferably by ultrasonic vapor degreasing.
The coils or core is made by assembling U-tubes and fins and expanding the tubes
in
the
conventional fashion. The ends of the U-tubes are flared to a prescribed socket geometry to
provide a joint and a friction fit for the inserted return bends [90]. After vapor degreasing
the
return bends and core tubes ends, the return bends are simply tapped into position. The joints
are preheated to soldering temperature in the inverted position by hot air or gas flame.
The
coil is then quickly transferred and lowered into a molten bath of 95% Zn-5%
A1
solder and
exposed for a few seconds to ultrasonic cavitation. The actual soldering of a coil requires only
a few seconds of ultrasonic exposure. The sequence of operations is depicted in Fig. 39.
Solder Composition and Maintenance of Soldering Bath. The solder composition recom-
mended is 95Zn-5A1, which is maintained at a temperature of
780-800°F.
Since each coil
processed through the soldering bath takes out some solder with
it,
the bath should be replen-
ished with fresh solder to maintain its depth. During the tinning process, some aluminum will
be eroded off the parts [93]. Therefore, the replenisher is slightly lean
in
aluminum, typically
98Zn-2A1, to keep the bath at
5%
A1 [89].
Process Control. There are four factors
that have significant effects on the joint quality
1901:
(I)
ultrasonic solder pot design, (2) socket design, (3) preheat, and (4) depth of immer-
sion. Another important factor is the soldering time.
Ultrasonic Soldering Pot. The
heart of the Alcoa
571
process is the ultrasonic soldering
pot, which is the container for the molten zinc-based solder [91]. Generally, the pot is made
from
AISI
304 type stainless steel. These pots come in rectangular (flat bottom), circular, or
contoured shape. Bottoms of rectangular pots usually have one
or
two rows of transducers.
Circular and contoured pots are better for soldering large coils because they have room for
more transducers [89]. Figure
40
shows a sketch of the ultrasonic pot.
In
general, rectangular
tanks have not performed satisfactorily when compared to round tanks [92].
Clean
-
F
Assemble
Dip
U
Pnheot
U(t
m
son
ic
solder
tank
Rmwe
teats
Figure
39
Fluxless ultrasonic soldering
by
the Alcoa
571
process. (From Ref.
93.)