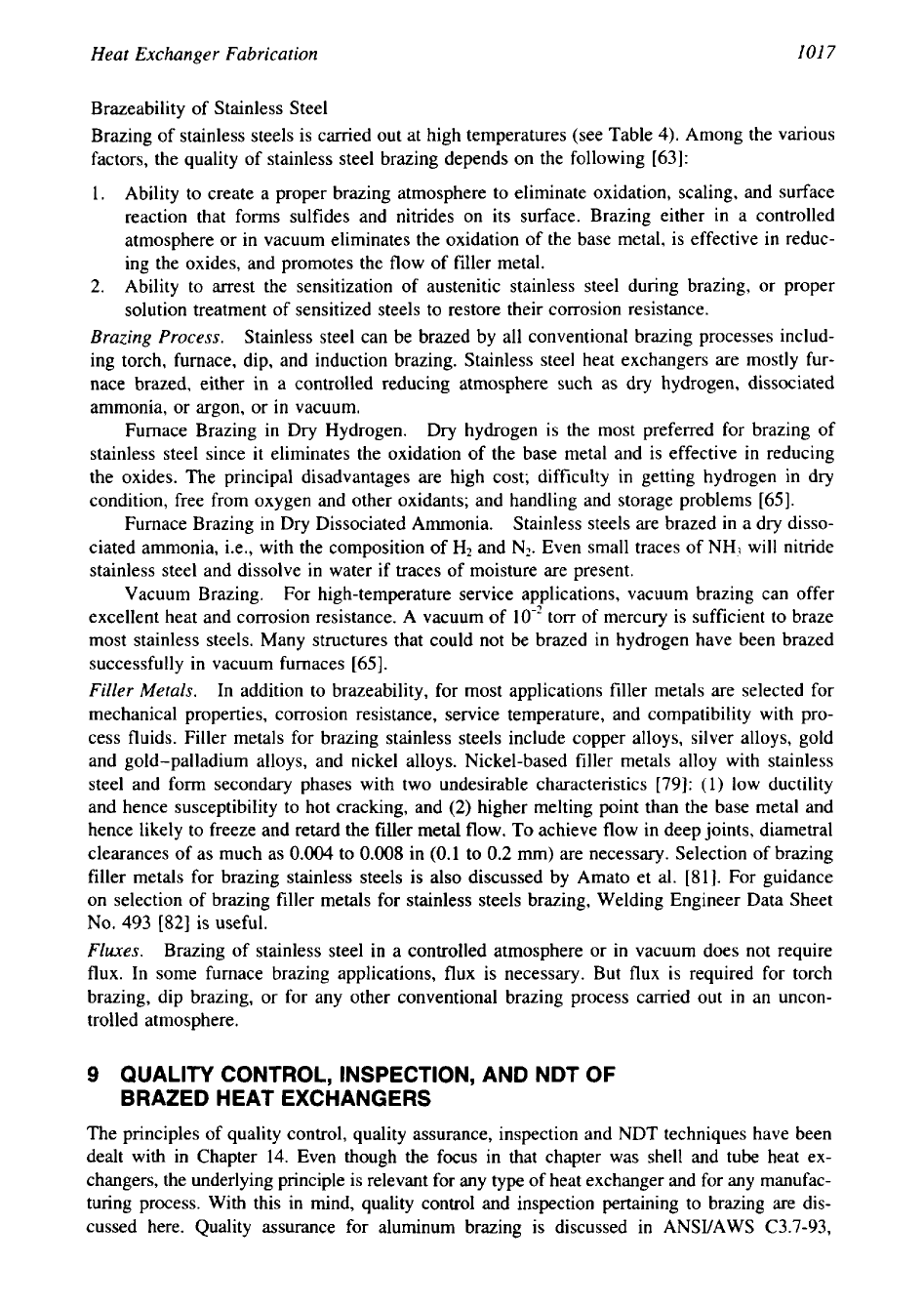
Heat Exchanger Fabrication
101
7
Brazeability of Stainless Steel
Brazing of stainless steels is carried out at high temperatures (see Table 4). Among the various
factors, the quality of stainless steel brazing depends on the following
[63]:
1.
Ability to create a proper brazing atmosphere to eliminate oxidation, scaling, and surface
reaction that forms sulfides and nitrides on its surface. Brazing either in a controlled
atmosphere or in vacuum eliminates the oxidation of the base metal, is effective in reduc-
ing the oxides, and promotes the flow of filler metal.
2.
Ability to arrest the sensitization of austenitic stainless steel during brazing, or proper
solution treatment of sensitized steels to restore their corrosion resistance.
Brazing Process.
Stainless steel can be brazed by all conventional brazing processes includ-
ing torch, furnace, dip, and induction brazing. Stainless steel heat exchangers are mostly fur-
nace brazed, either in a controlled reducing atmosphere such as dry hydrogen, dissociated
ammonia, or argon, or in vacuum.
Furnace Brazing in Dry Hydrogen.
Dry hydrogen is the most preferred for brazing of
stainless steel since it eliminates the oxidation of the base metal and is effective in reducing
the oxides. The principal disadvantages are high cost; difficulty in getting hydrogen in dry
condition, free from oxygen and other oxidants; and handling and storage problems
[65].
Furnace Brazing in Dry Dissociated Ammonia.
Stainless steels are brazed in a dry disso-
ciated ammonia, i.e., with the composition of H2 and N2. Even small traces of NH3 will nitride
stainless steel and dissolve in water if traces of moisture are present.
Vacuum Brazing.
For high-temperature service applications, vacuum brazing can offer
excellent heat and corrosion resistance. A vacuum of
10-*
torr of mercury is sufficient to braze
most stainless steels. Many structures that could not be brazed in hydrogen have been brazed
successfully in vacuum furnaces
[65].
Filler Metals.
In addition
to
brazeability, for most applications filler metals are selected for
mechanical properties, corrosion resistance, service temperature, and compatibility with pro-
cess fluids. Filler metals for brazing stainless steels include copper alloys, silver alloys, gold
and gold-palladium alloys, and nickel alloys. Nickel-based filler metals alloy with stainless
steel and form secondary phases with two undesirable characteristics
[79]:
(1)
low ductility
and hence susceptibility to hot cracking, and
(2)
higher melting point than the base metal and
hence likely to freeze and retard the filler metal
flow.
To achieve flow in deep joints, diametral
clearances of as much as
0.004
to
0.008
in (0.1 to
0.2
mm)
are necessary. Selection of brazing
filler metals for brazing stainless steels is
also
discussed by Amato et al. [81]. For guidance
on selection of brazing filler metals for stainless steels brazing, Welding Engineer Data Sheet
No.
493
[82]
is useful.
Flues.
Brazing of stainless steel in a controlled atmosphere or in vacuum does not require
flux. In some furnace brazing applications, flux is necessary. But flux is required for torch
brazing, dip brazing, or for any other conventional brazing process carried out in an uncon-
trolled atmosphere.
9
QUALITY CONTROL, INSPECTION, AND NDT
OF
BRAZEDHEATEXCHANGERS
The principles of quality control, quality assurance, inspection and NDT techniques have been
dealt with in Chapter 14. Even though the focus in that chapter was shell and tube heat ex-
changers, the underlying principle is relevant for any type of heat exchanger and for any manufac-
turing process. With this in mind, quality control and inspection pertaining to brazing are dis-
cussed here. Quality assurance for aluminum brazing is discussed in ANSVAWS
C3.7-93,