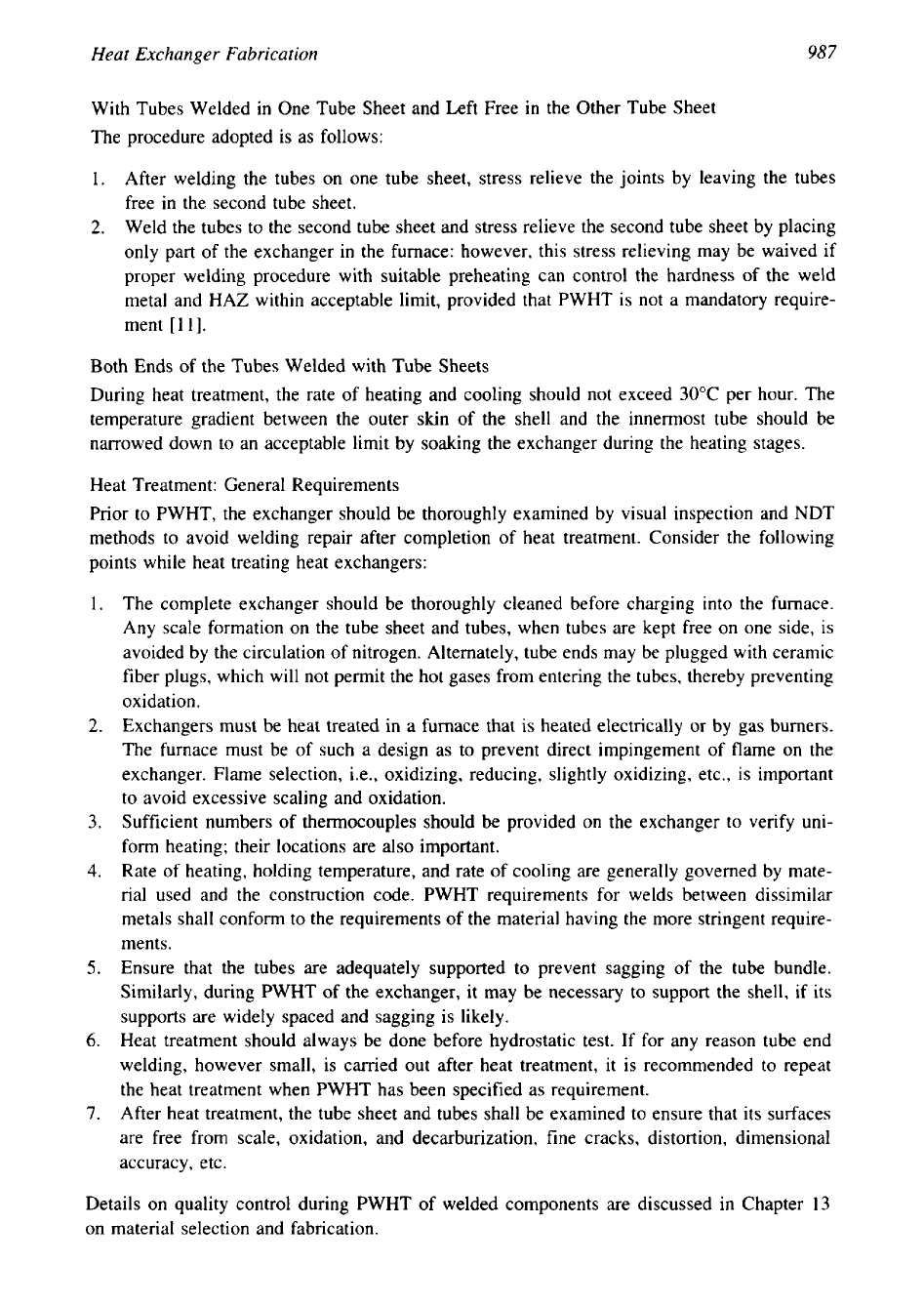
987
Heat Exchanger Fabrication
With Tubes Welded in One Tube Sheet and Left Free in the Other Tube Sheet
The procedure adopted is as follows:
1.
After welding the tubes on one tube sheet, stress relieve the joints by leaving the tubes
free in the second tube sheet.
2.
Weld the tubes to the second tube sheet and stress relieve the second tube sheet by placing
only part of the exchanger in the furnace: however, this stress relieving may be waived if
proper welding procedure with suitable preheating can control the hardness of the weld
metal and HAZ within acceptable limit, provided that PWHT is not a mandatory require-
ment [ll].
Both Ends of the Tubes Welded with Tube Sheets
During heat treatment, the rate of heating and cooling should not exceed 30°C per hour. The
temperature gradient between the outer skin of the shell and the innermost tube should be
narrowed down to an acceptable limit by soaking the exchanger during the heating stages.
Heat Treatment: General Requirements
Prior to PWHT, the exchanger should be thoroughly examined by visual inspection and NDT
methods to avoid welding repair after completion of heat treatment. Consider the following
points while heat treating heat exchangers:
1.
The complete exchanger should be thoroughly cleaned before charging into the furnace.
Any scale formation on the tube sheet and tubes, when tubes are kept free on one side, is
avoided by the circulation of nitrogen. Alternately, tube ends may be plugged with ceramic
fiber plugs, which will not permit the hot gases from entering the tubes, thereby preventing
oxidation.
2.
Exchangers must be heat treated in a furnace that is heated electrically or by
gas
burners.
The furnace must be of such a design as to prevent direct impingement of flame on the
exchanger. Flame selection, i.e., oxidizing, reducing, slightly oxidizing, etc.,
is
important
to avoid excessive scaling and oxidation.
3.
Sufficient numbers of thermocouples should be provided on the exchanger to verify uni-
form heating; their locations are also important.
4.
Rate of heating, holding temperature, and rate of cooling are generally governed by mate-
rial used and the construction code. PWHT requirements for welds between dissimilar
metals shall conform to the requirements of the material having the more stringent require-
ments.
5.
Ensure that the tubes are adequately supported to prevent sagging of the tube bundle.
Similarly, during PWHT of the exchanger, it may be necessary to support the shell, if its
supports are widely spaced and sagging is likely.
6.
Heat treatment should always be done before hydrostatic test. If for any reason tube end
welding, however small, is carried out after heat treatment, it is recommended to repeat
the heat treatment when PWHT has been specified as requirement.
7.
After heat treatment, the tube sheet and tubes shall be examined to ensure that its surfaces
are free from scale, oxidation, and decarburization, fine cracks, distortion, dimensional
accuracy, etc.
Details on quality control during PWHT of welded components are discussed in Chapter 13
on material selection and fabrication.