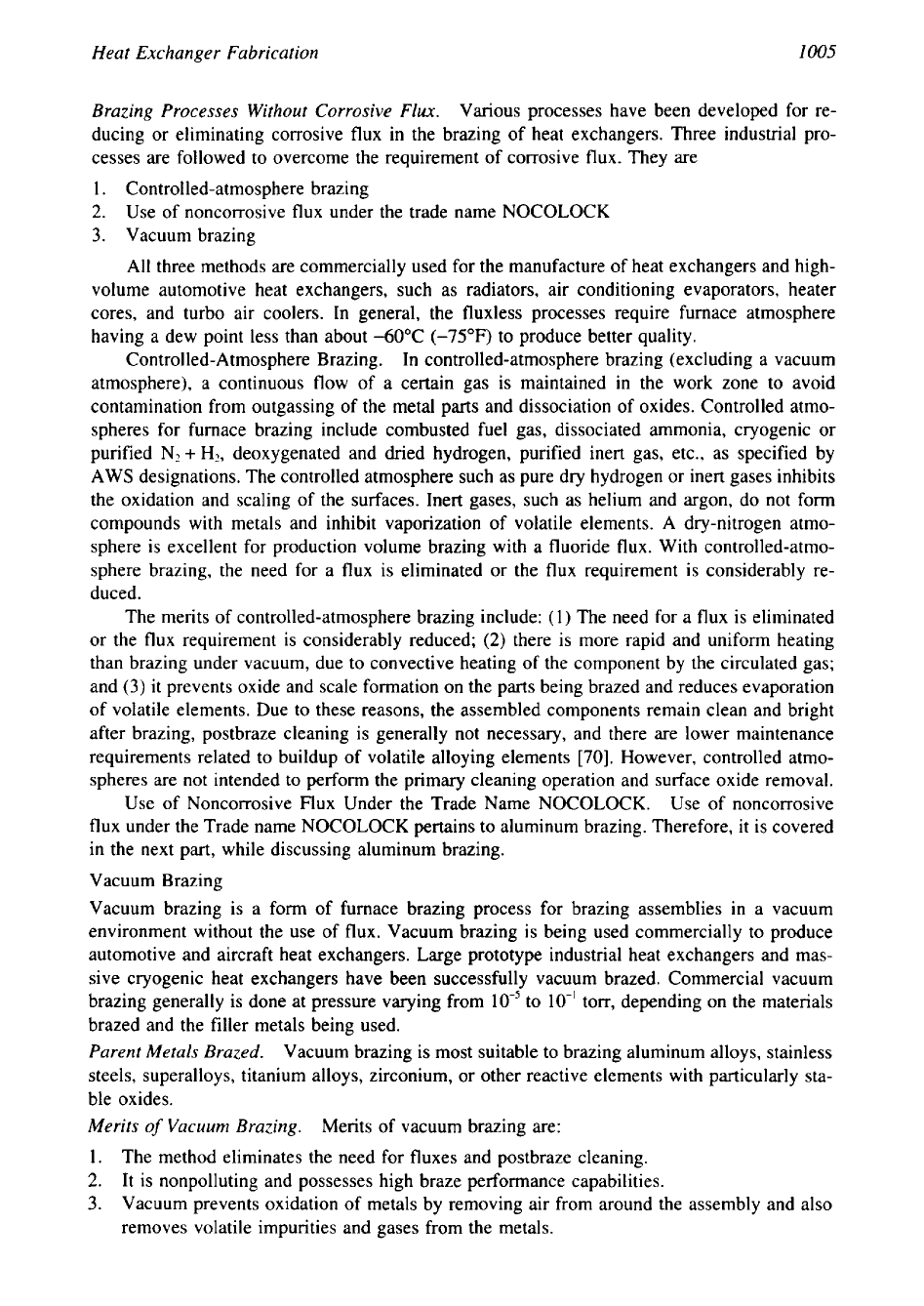
Heat Exchanger Fabrication
I005
Brazing Processes Without Corrosive
Flux.
Various processes have been developed for re-
ducing or eliminating corrosive
flux
in the brazing of heat exchangers. Three industrial pro-
cesses are followed to overcome the requirement of corrosive flux. They are
1.
Controlled-atmosphere brazing
2.
Use of noncorrosive flux under the trade name NOCOLOCK
3.
Vacuum brazing
All three methods are commercially used for the manufacture of heat exchangers and high-
volume automotive heat exchangers, such as radiators, air conditioning evaporators, heater
cores, and turbo air coolers. In general, the fluxless processes require furnace atmosphere
having a dew point less than about
-60°C
(-75°F)
to produce better quality.
Controlled-Atmosphere Brazing.
In controlled-atmosphere brazing (excluding a vacuum
atmosphere), a continuous flow of a certain gas is maintained in the work zone to avoid
contamination from outgassing of the metal parts and dissociation of oxides. Controlled atmo-
spheres for furnace brazing include combusted fuel gas, dissociated ammonia, cryogenic or
purified N2
+
HZ, deoxygenated and dried hydrogen, purified inert gas, etc., as specified by
AWS designations. The controlled atmosphere such as pure dry hydrogen or inert gases inhibits
the oxidation and scaling of the surfaces. Inert gases, such as helium and argon, do not form
compounds with metals and inhibit vaporization of volatile elements. A dry-nitrogen atmo-
sphere is excellent for production volume brazing with a fluoride flux. With controlled-atmo-
sphere brazing, the need for a
flux
is eliminated or the flux requirement is considerably re-
duced.
The merits of controlled-atmosphere brazing include:
(1)
The need for a flux is eliminated
or the flux requirement is considerably reduced;
(2)
there is more rapid and uniform heating
than brazing under vacuum, due to convective heating of the component by the circulated gas;
and
(3)
it prevents oxide and scale formation on the parts being brazed and reduces evaporation
of volatile elements. Due to these reasons, the assembled components remain clean and bright
after brazing, postbraze cleaning is generally not necessary, and there are lower maintenance
requirements related to buildup of volatile alloying elements
[70].
However, controlled atmo-
spheres are not intended
to
perform the primary cleaning operation and surface oxide removal.
Use of Noncorrosive
Flux
Under the Trade Name NOCOLOCK.
Use of noncorrosive
flux under the Trade name NOCOLOCK pertains to aluminum brazing. Therefore, it is covered
in the next part, while discussing aluminum brazing.
Vacuum Brazing
Vacuum brazing is a form of furnace brazing process for brazing assemblies in a vacuum
environment without the use of flux. Vacuum brazing is being used commercially to produce
automotive and aircraft heat exchangers. Large prototype industrial heat exchangers and mas-
sive cryogenic heat exchangers have been successfully vacuum brazed. Commercial vacuum
brazing generally is done at pressure varying from
10-5
to
10-'
torr, depending on the materials
brazed and the filler metals being used.
Parent Metals Brazed.
Vacuum brazing
is
most suitable to brazing aluminum alloys, stainless
steels, superalloys, titanium alloys, zirconium, or other reactive elements with particularly sta-
ble oxides.
Merits
of
Vacuum Brazing.
Merits of vacuum brazing are:
1.
The method eliminates the need for fluxes and postbraze cleaning.
2.
It is nonpolluting and possesses high braze performance capabilities.
3.
Vacuum prevents oxidation of metals by removing air from around the assembly and also
removes volatile impurities and gases from the metals.