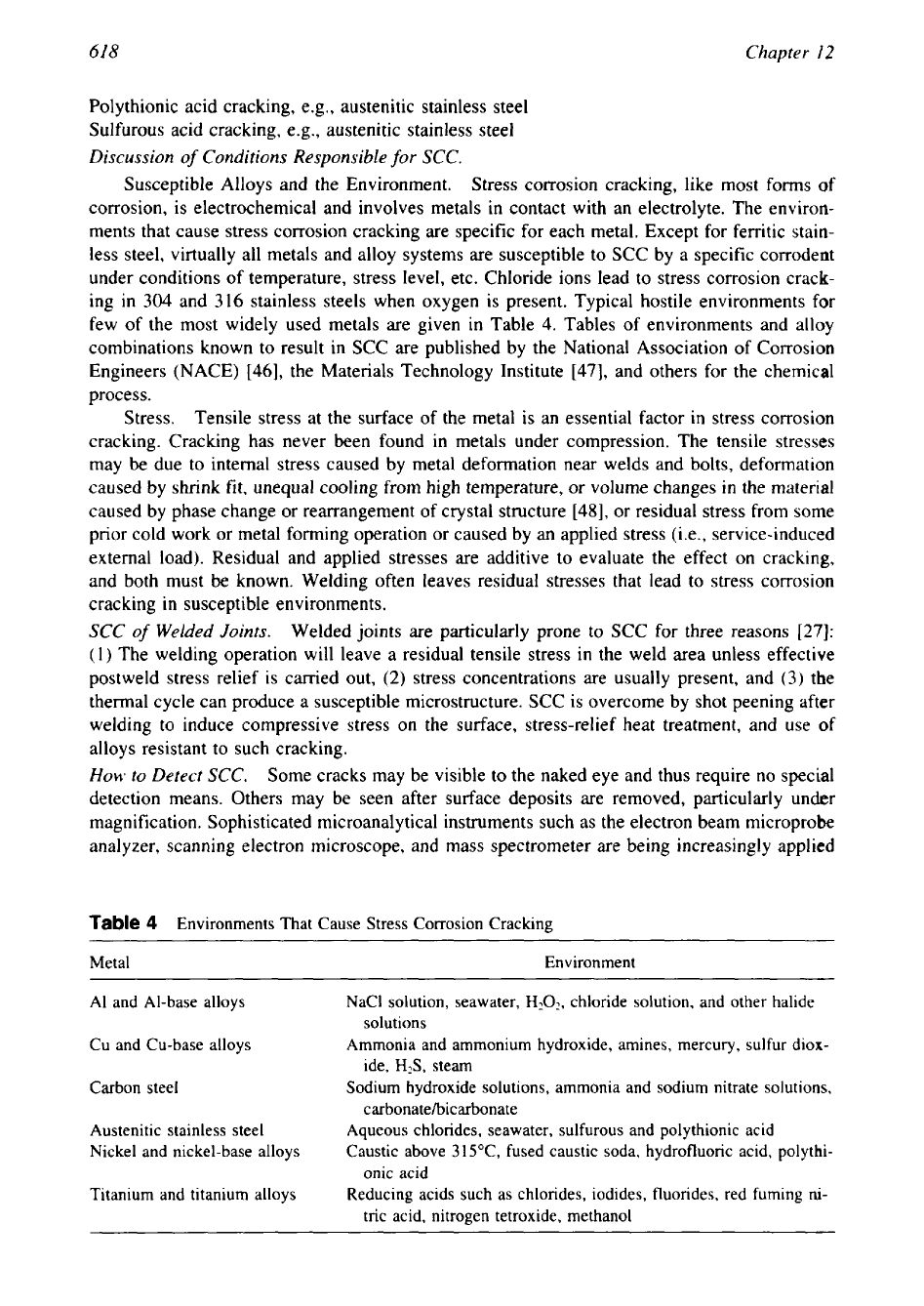
618
Chapter
12
Polythionic acid cracking, e.g., austenitic stainless steel
Sulfurous acid cracking, e.g., austenitic stainless steel
Discussion
of
Conditions Responsible
for
SCC.
Susceptible Alloys and the Environment.
Stress corrosion cracking, like most forms of
corrosion, is electrochemical and involves metals in contact with an electrolyte. The environ-
ments that cause stress corrosion cracking are specific for each metal. Except for ferritic stain-
less steel, virtually all metals and alloy systems are susceptible to SCC by a specific corrodent
under conditions of temperature, stress level, etc. Chloride ions lead to stress corrosion crack-
ing in 304 and 316 stainless steels when oxygen is present. Typical hostile environments for
few of the most widely used metals are given in Table 4. Tables of environments and alloy
combinations known to result in SCC are published by the National Association of Corrosion
Engineers (NACE) [46], the Materials Technology Institute [47], and others for the chemical
process.
Stress.
Tensile stress at the surface of the metal is an essential factor in stress corrosion
cracking. Cracking has never been found in metals under compression. The tensile stresses
may be due to internal stress caused by metal deformation near welds and bolts, deformation
caused by shrink fit, unequal cooling from high temperature, or volume changes
in
the material
caused by phase change or rearrangement of crystal structure [48], or residual stress from some
prior cold work or metal forming operation or caused by an applied stress (i.e., service-induced
external load). Residual and applied stresses are additive to evaluate the effect on cracking,
and both must be known. Welding often leaves residual stresses that lead to stress corrosion
cracking in susceptible environments.
SCC
of
Welded Joints.
Welded joints are particularly prone to SCC for three reasons [27]:
(1)
The welding operation will leave a residual tensile stress in the weld area unless effective
postweld stress relief is carried out,
(2)
stress concentrations are usually present, and (3) the
thermal cycle can produce a susceptible microstructure. SCC is overcome by shot peening after
welding to induce compressive stress on the surface, stress-relief heat treatment, and use of
alloys resistant to such cracking.
HOW
to Detect
SCC.
Some cracks may be visible to the naked eye and thus require no special
detection means. Others may be seen after surface deposits are removed, particularly under
magnification. Sophisticated microanalytical instruments such as the electron beam microprobe
analyzer, scanning electron microscope, and mass spectrometer are being increasingly applied
Table
4
Environments That Cause Stress Corrosion Cracking
Metal Environment
A1 and Al-base alloys
NaCl solution, seawater,
H202,
chloride solution, and other halide
solutions
Cu and Cu-base alloys
Ammonia and ammonium hydroxide, amines, mercury, sulfur diox-
ide,
H2S,
steam
Carbon steel
Sodium hydroxide solutions, ammonia and sodium nitrate solutions,
carbonatehicarbonate
Austenitic stainless steel
Aqueous chlorides, seawater, sulfurous and polythionic acid
Nickel and nickel-base alloys Caustic above
3
15OC, fused caustic soda, hydrofluoric acid, polythi-
onic acid
Titanium and titanium alloys
Reducing acids such as chlorides, iodides, fluorides, red fuming
ni-
tric acid, nitrogen tetroxide, methanol