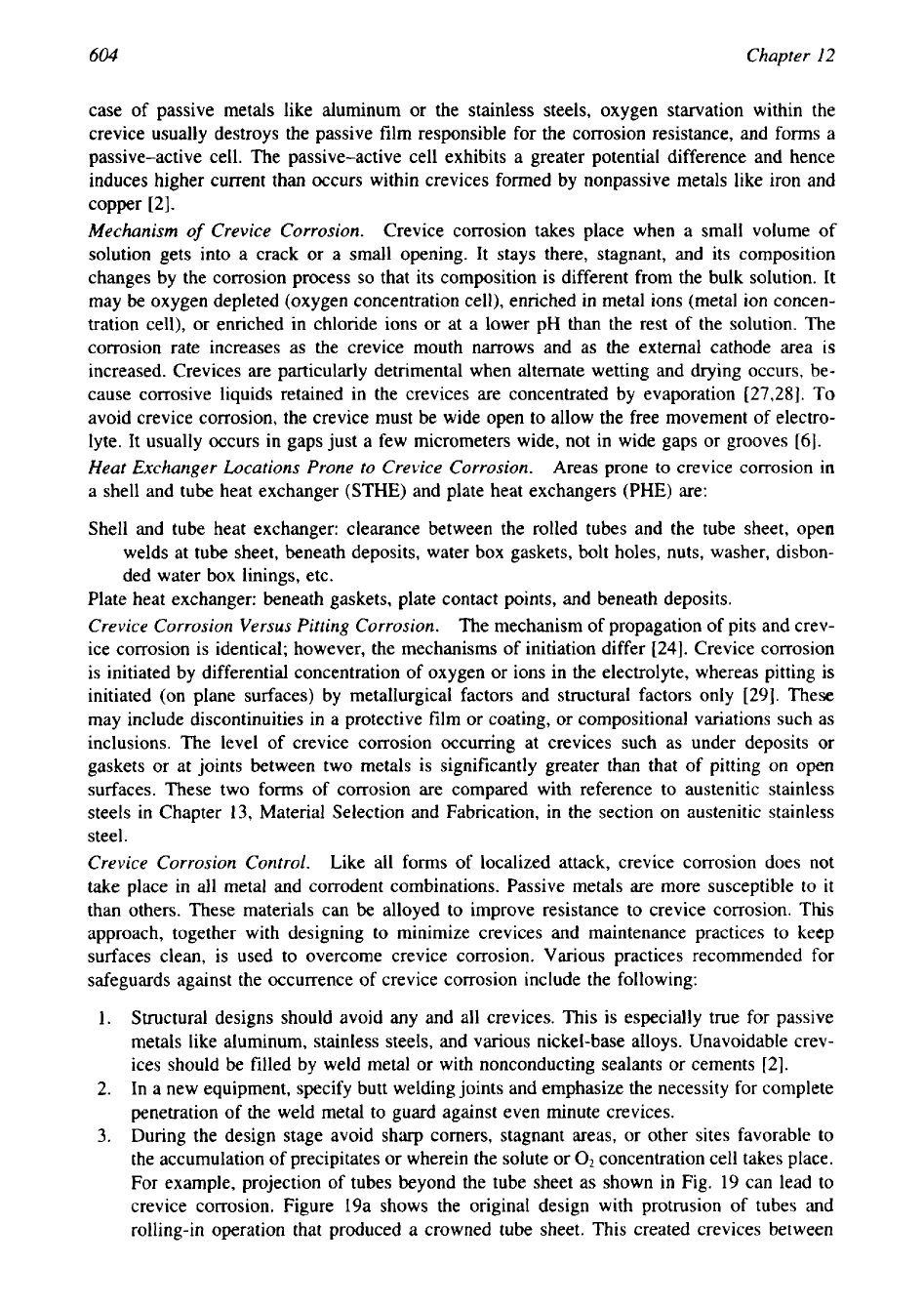
604
Chapter
12
case of passive metals like aluminum or the stainless steels, oxygen starvation within the
crevice usually destroys the passive film responsible for the corrosion resistance, and forms a
passive-active cell. The passive-active cell exhibits a greater potential difference and hence
induces higher current than occurs within crevices formed by nonpassive metals like iron and
copper 121.
Mechanism
of
Crevice Corrosion.
Crevice corrosion takes place when a small volume of
solution gets into a crack or a small opening. It stays there, stagnant, and its composition
changes by the corrosion process
so
that its composition is different from the bulk solution. It
may be oxygen depleted (oxygen concentration cell), enriched in metal ions (metal ion concen-
tration cell), or enriched in chloride ions or at a lower pH than the rest of the solution. The
corrosion rate increases as the crevice mouth narrows and
as
the external cathode area is
increased. Crevices are particularly detrimental when alternate wetting and drying occurs, be-
cause corrosive liquids retained in the crevices are concentrated by evaporation [27,28].
To
avoid crevice corrosion, the crevice must be wide open to allow the free movement
of
electro-
lyte. It usually occurs in gaps just a few micrometers wide, not in wide gaps or grooves
[6].
Heat Exchanger Locations Prone to Crevice Corrosion.
Areas prone to crevice corrosion
in
a shell and tube heat exchanger (STHE) and plate heat exchangers (PHE) are:
Shell and tube heat exchanger: clearance between the rolled tubes and the tube sheet, open
welds at tube sheet, beneath deposits, water box gaskets, bolt holes, nuts, washer, disbon-
ded water box linings, etc.
Plate heat exchanger: beneath gaskets, plate contact points, and beneath deposits.
Crevice Corrosion Versus
Pitting
Corrosion.
The mechanism of propagation of pits and crev-
ice corrosion is identical; however, the mechanisms of initiation differ [24]. Crevice corrosion
is initiated by differential concentration of oxygen or ions in the electrolyte, whereas pitting
is
initiated (on plane surfaces) by metallurgical factors and structural factors only [29]. These
may include discontinuities in a protective film or coating, or compositional variations such
as
inclusions. The level of crevice corrosion occurring at crevices such as under deposits or
gaskets or at joints between two metals is significantly greater than that of pitting on open
surfaces. These two forms of corrosion are compared with reference to austenitic stainless
steels in Chapter 13, Material Selection and Fabrication, in the section
on
austenitic stainless
steel.
Crevice Corrosion Control.
Like all forms of localized attack, crevice corrosion does not
take place in all metal and corrodent combinations. Passive metals are more susceptible
to
it
than others. These materials can be alloyed to improve resistance to crevice corrosion.
This
approach, together with designing to minimize crevices and maintenance practices to keep
surfaces clean, is used to overcome crevice corrosion. Various practices recommended for
safeguards against the occurrence of crevice corrosion include the following:
1.
Structural designs should avoid any and all crevices. This is especially true for passive
metals like aluminum, stainless steels, and various nickel-base alloys. Unavoidable crev-
ices should be filled by weld metal or with nonconducting sealants or cements [2].
2.
In a new equipment, specify butt welding joints and emphasize the necessity for complete
penetration of the weld metal to guard against even minute crevices.
3.
During the design stage avoid sharp corners, stagnant areas, or other sites favorable to
the accumulation of precipitates or wherein the solute or
O2
concentration cell takes place.
For example, projection of tubes beyond the tube sheet as shown in Fig. 19 can lead to
crevice corrosion. Figure 19a shows the original design with protrusion of tubes and
rolling-in operation that produced a crowned tube sheet. This created crevices between