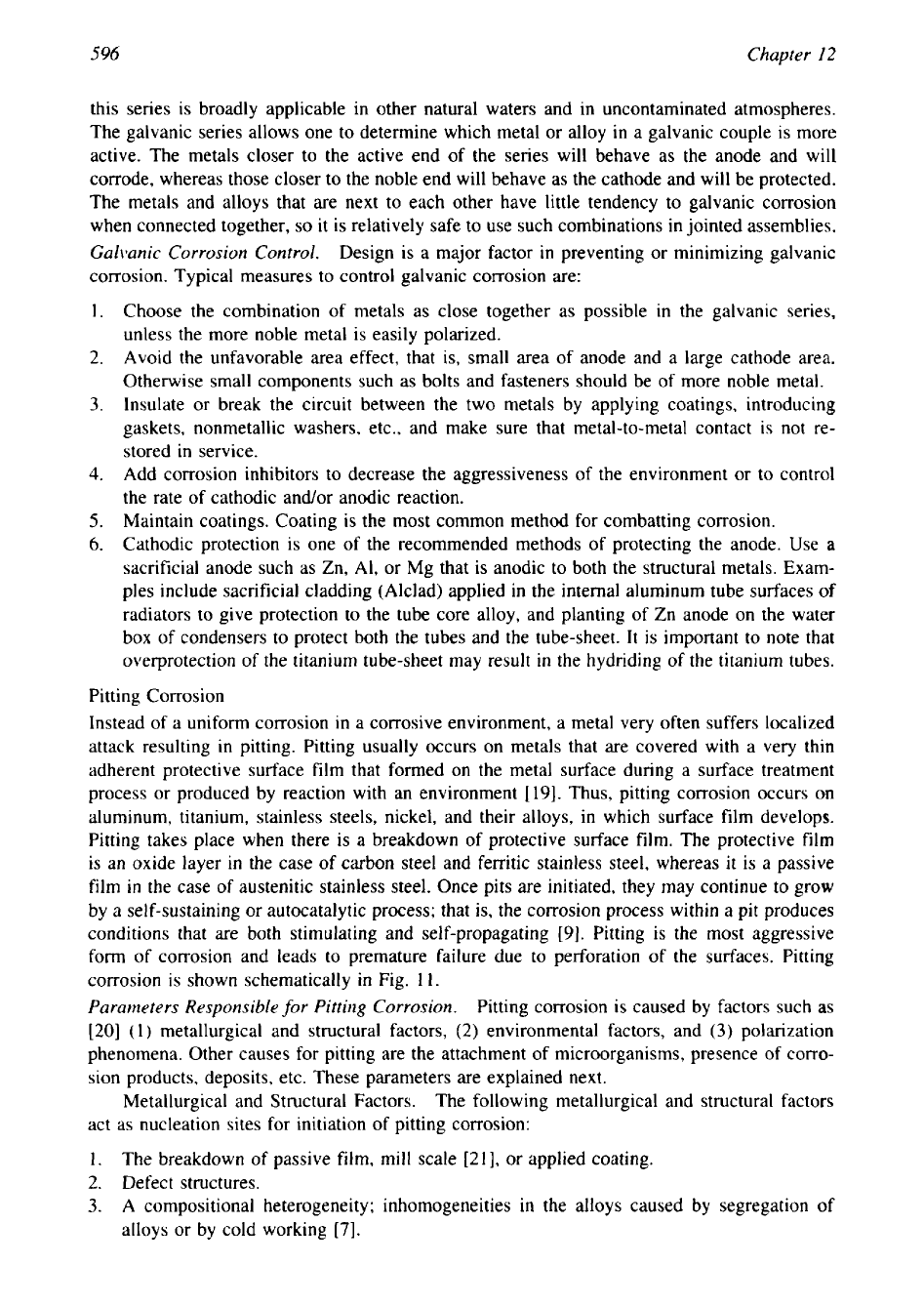
596
Chapter
12
this series is broadly applicable in other natural waters and in uncontaminated atmospheres.
The galvanic series allows one to determine which metal or alloy in a galvanic couple is more
active. The metals closer to the active end of the series will behave as the anode and will
corrode, whereas those closer to the noble end will behave as the cathode and will be protected.
The metals and alloys that are next to each other have little tendency to galvanic corrosion
when connected together,
so
it is relatively safe to use such combinations in jointed assemblies,
Galrwnic Corrosion Control.
Design is a major factor in preventing or minimizing galvanic
corrosion. Typical measures to control galvanic corrosion are:
1.
Choose the combination of metals as close together as possible in the galvanic series,
unless the more noble metal is easily polarized.
2.
Avoid the unfavorable area effect, that is, small area
of
anode and a large cathode area,
Otherwise small components such as bolts and fasteners should be of more noble metal.
3.
Insulate
or
break the circuit between the two metals by applying coatings, introducing
gaskets, nonmetallic washers, etc., and make sure that metal-to-metal contact is not re-
stored
in
service.
4.
Add corrosion inhibitors to decrease the aggressiveness of the environment or to control
the rate of cathodic andor anodic reaction.
5.
Maintain coatings. Coating is the most common method for combatting corrosion.
6.
Cathodic protection is one
of
the recommended methods of protecting the anode. Use
a
sacrificial anode such as Zn, Al, or Mg that is anodic to both the structural metals. Exam-
ples include sacrificial cladding (Alclad) applied
in
the internal aluminum tube surfaces
of
radiators to give protection to the tube core alloy, and planting of Zn anode on the water
box of condensers to protect both the tubes and the tube-sheet.
It
is important to note that
overprotection of the titanium tube-sheet may result
in
the hydriding of the titanium tubes.
Pitting Corrosion
Instead of a uniform corrosion
in
a corrosive environment, a metal very often suffers localized
attack resulting in pitting. Pitting usually occurs on metals that are covered with a very thin
adherent protective surface film that formed on the metal surface during a surface treatment
process or produced by reaction with an environment
[
191. Thus, pitting corrosion occurs
on
aluminum, titanium, stainless steels, nickel, and their alloys, in which surface film develops.
Pitting takes place when there is a breakdown of protective surface film. The protective film
is an oxide layer in the case of carbon steel and ferritic stainless steel, whereas it is a passive
film
in
the case of austenitic stainless steel. Once pits are initiated, they may continue to grow
by
a
self-sustaining or autocatalytic process; that is, the corrosion process within a pit produces
conditions that are both stimulating and self-propagating [9]. Pitting is the most aggressive
form of corrosion and leads to premature failure due to perforation of the surfaces. Pitting
corrosion is shown schematically
in
Fig.
11.
Parameters Responsible
for
Pitting
Corrosion.
Pitting corrosion is caused by factors such
as
[20]
(
1
)
metallurgical and structural factors,
(2)
environmental factors, and
(3)
polarization
phenomena. Other causes for pitting are the attachment of microorganisms, presence of corro-
sion products, deposits, etc. These parameters are explained next.
Metallurgical and Structural Factors.
The following metallurgical and structural factors
act as nucleation sites for initiation of pitting corrosion:
1.
The breakdown of passive film, mill scale
[21],
or applied coating.
2.
Defect structures.
3.
A compositional heterogeneity; inhomogeneities in the alloys caused by segregation of
alloys or by cold working
[7].