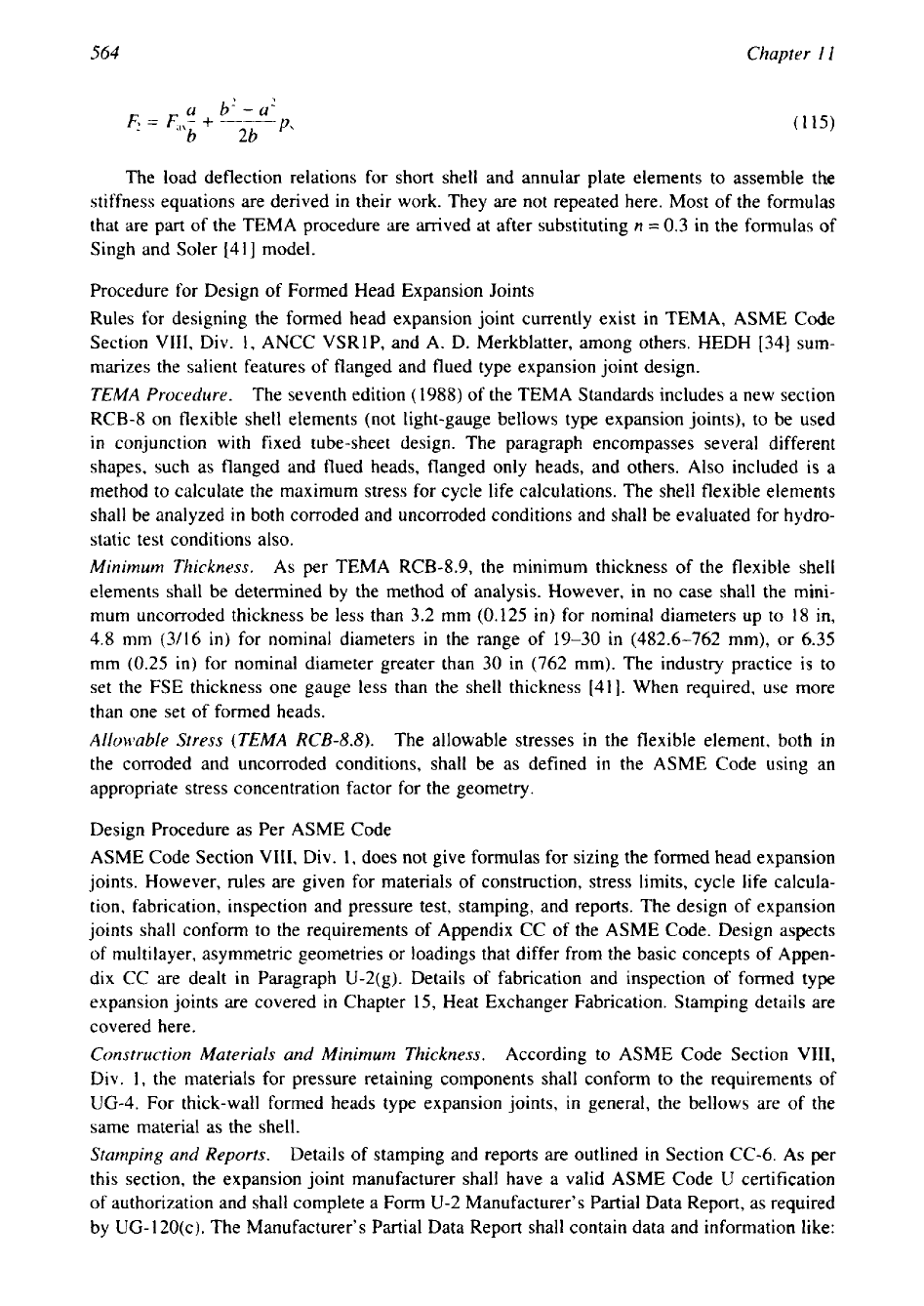
564
Chapter
I1
The load deflection relations for short shell and annular plate elements to assemble the
stiffness equations are derived
in
their work. They are not repeated here. Most of the formulas
that are part of the TEMA procedure are arrived at after substituting
n
=
0.3
in the formulas of
Singh and Soler [41] model.
Procedure for Design of Formed Head Expansion Joints
Rules for designing the formed head expansion joint currently exist in TEMA, ASME Code
Section VIII, Div.
1,
ANCC VSRlP, and A. D. Merkblatter, among others. HEDH [34] sum-
marizes the salient features of flanged and flued type expansion joint design.
TEMA Procedure.
The seventh edition
(1988)
of the TEMA Standards includes a new section
RCB-8 on flexible shell elements (not light-gauge bellows type expansion joints), to be used
in
conjunction with fixed tube-sheet design. The paragraph encompasses several different
shapes, such as flanged and flued heads, flanged only heads, and others. Also included is a
method to calculate the maximum stress for cycle life calculations. The shell flexible elements
shall be analyzed
in
both corroded and uncorroded conditions and shall be evaluated for hydro-
static test conditions also.
Minimum Thickness.
As per TEMA RCB-8.9, the minimum thickness of the flexible shell
elements shall be determined by the method of analysis. However, in no case shall the mini-
mum uncorroded thickness be less than 3.2 mm (0.125
in)
for nominal diameters up to
18
in,
4.8 mm (3/16
in)
for nominal diameters in the range of
19-30
in (482.6-762 mm), or
6.35
mm (0.25
in)
for nominal diameter greater than
30
in
(762 mm). The industry practice is to
set the FSE thickness one gauge less than the shell thickness [41]. When required, use more
than one set of formed heads.
Allowable Stress (TEMA RCB-8.8).
The allowable stresses
in
the flexible element, both
in
the corroded and uncorroded conditions, shall be as defined in the ASME Code using an
appropriate stress concentration factor for the geometry.
Design Procedure as Per ASME Code
ASME Code Section VIII, Div.
1,
does not give formulas for sizing the formed head expansion
joints. However, rules are given for materials of construction, stress limits, cycle life calcula-
tion, fabrication, inspection and pressure test, stamping, and reports. The design of expansion
joints shall conform to the requirements of Appendix CC of the ASME Code. Design aspects
of multilayer, asymmetric geometries or loadings that differ from the basic concepts of Appen-
dix CC are dealt in Paragraph U-2(g). Details of fabrication and inspection of formed type
expansion joints are covered
in
Chapter
15,
Heat Exchanger Fabrication. Stamping details are
covered here.
Construction Materials and Minimum Thickness.
According to ASME Code Section VIII,
Div.
1,
the materials for pressure retaining components shall conform to the requirements of
UG-4. For thick-wall formed heads type expansion joints,
in
general, the bellows are
of
the
same material as the shell.
Stamping and Reports.
Details of stamping and reports are outlined
in
Section CC-6.
As
per
this section, the expansion joint manufacturer shall have a valid ASME Code
U
certification
of authorization and shall complete a Form U-2 Manufacturer’s Partial Data Report, as required
by UG- 120(c). The Manufacturer’s Partial Data Report shall contain data and information like: