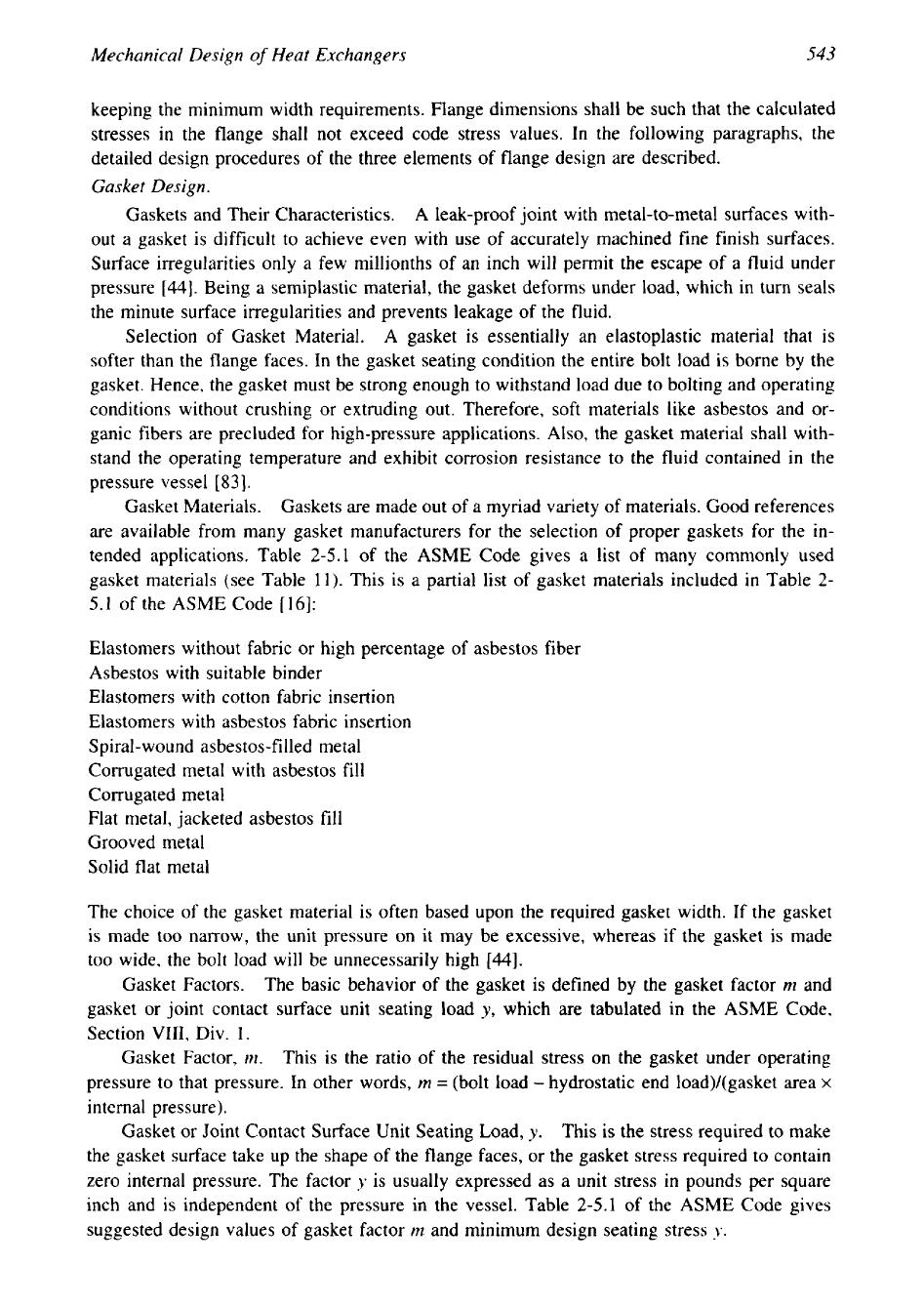
543
Mechanical Design
of
Heat Exchangers
keeping the minimum width requirements, Flange dimensions shall be such that the calculated
stresses in the flange shall not exceed code stress values. In the following paragraphs, the
detailed design procedures of the three elements of flange design are described.
Gasket Design
.
Gaskets and Their Characteristics.
A
leak-proof joint with metal-to-metal surfaces with-
out a gasket is difficult to achieve even with use of accurately machined fine finish surfaces.
Surface irregularities only a few millionths of
an
inch will permit the escape of a fluid under
pressure
[44].
Being a semiplastic material, the gasket deforms under load, which in turn seals
the minute surface irregularities and prevents leakage of the fluid.
Selection of Gasket Material.
A gasket is essentially an elastoplastic material that is
softer than the flange faces. In the gasket seating condition the entire bolt load is borne by the
gasket. Hence, the gasket must be strong enough to withstand load due to bolting and operating
conditions without crushing or extruding out. Therefore, soft materials like asbestos and or-
ganic fibers are precluded for high-pressure applications.
Also,
the gasket material shall with-
stand the operating temperature and exhibit corrosion resistance to the fluid contained in the
pressure vessel [83].
Gasket Materials.
Gaskets are made out of a myriad variety
of
materials. Good references
are available from many gasket manufacturers for the selection of proper gaskets for the in-
tended applications. Table
2-5.1
of the ASME Code gives a list of many commonly used
gasket materials (see Table
11).
This is a partial list of gasket materials included in Table
2-
5.1
of the ASME Code
[
161:
Elastomers without fabric or high percentage of asbestos fiber
Asbestos with suitable binder
Elastomers with cotton fabric insertion
Elastomers with asbestos fabric insertion
Spiral-wound asbestos-filled metal
Corrugated metal with asbestos fill
Corrugated metal
Flat metal, jacketed asbestos fill
Grooved metal
Solid flat metal
The choice of the gasket material is often based upon the required gasket width. If the gasket
is made too narrow, the unit pressure on it may be excessive, whereas if the gasket is made
too wide, the bolt load will be unnecessarily high
[44].
Gasket Factors. The basic behavior of the gasket is defined by the gasket factor
rn
and
gasket
or
joint contact surface unit seating load
y,
which are tabulated in the ASME Code,
Section VIII, Div.
1.
Gasket Factor,
in.
This is the ratio of the residual stress on the gasket under operating
pressure to that pressure. In other words,
rn
=
(bolt load
-
hydrostatic end load)/(gasket area
x
internal pressure).
Gasket or Joint Contact Surface Unit Seating Load,
y.
This is the stress required to make
the gasket surface take up the shape of the flange faces, or the gasket stress required to contain
zero internal pressure. The factor
y
is usually expressed as a unit stress in pounds per square
inch and is independent of the pressure in the vessel. Table
2-5.1
of the ASME Code gives
suggested design values of gasket factor
rn
and minimum design seating stress
y.