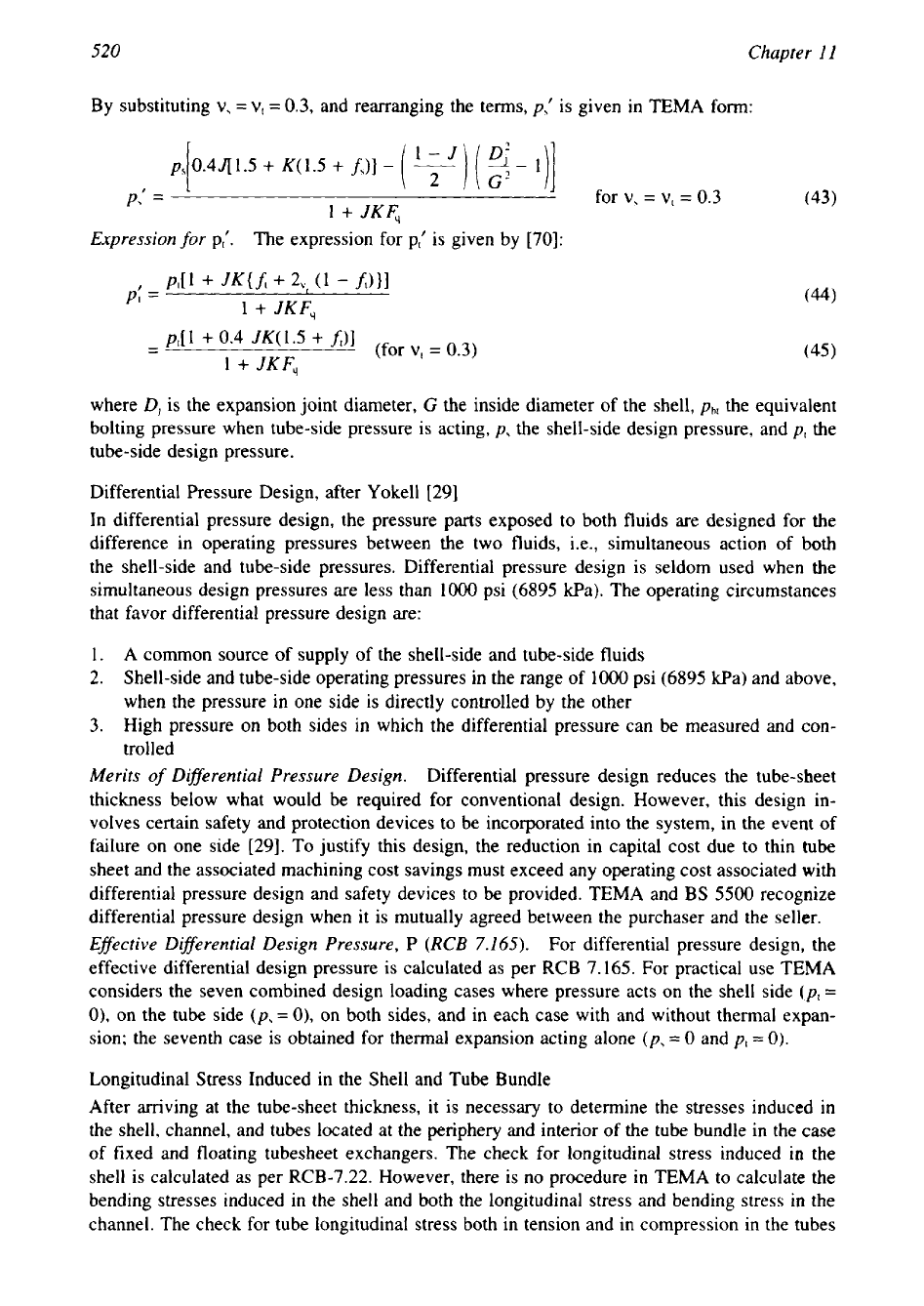
520
Chapter
I1
By substituting
v,
=
vI
=
0.3,
and rearranging the terms,
p,I
is given in TEMA form:
Expression
for
p,', The expression for pIf is given by
[70]:
p"l
+
JUft
+
2,,
(1
-
ftHl
p:
=
1
+
JKF,
-
p,[
1
+
0.4
JK(
1.5
+
A)]
(for
v,
=
0.3)
-
1
+
JKF,
(45)
where
D,
is the expansion joint diameter,
G
the inside diameter of the shell,
Pb[
the equivalent
bolting pressure when tube-side pressure is acting,
p,
the shell-side design pressure, and
p(
the
tube-side design pressure.
Differential Pressure Design, after Yokel1
[
291
In differential pressure design, the pressure
parts
exposed to both fluids are designed for the
difference in operating pressures between the two fluids, i.e., simultaneous action of both
the shell-side and tube-side pressures. Differential pressure design is seldom used when the
simultaneous design pressures are less than
1000
psi (6895 kPa). The operating circumstances
that favor differential pressure design are:
1.
A
common source of supply of the shell-side and tube-side fluids
2.
Shell-side and tube-side operating pressures in the range of
1000
psi (6895 kPa) and above,
when the pressure in one side is directly controlled by the other
3.
High pressure on both sides in which the differential pressure can be measured and con-
trolled
Merits
of
Diflerential Pressure Design.
Differential pressure design reduces the tube-sheet
thickness below what would be required for conventional design. However, this design in-
volves certain safety
and
protection devices to be incorporated into the system, in the event of
failure on one side [29]. To justify this design, the reduction in capital cost due to thin tube
sheet and the associated machining cost savings must exceed any operating cost associated with
differential pressure design and safety devices to be provided. TEMA and
BS
5500
recognize
differential pressure design when it is mutually agreed between the purchaser and the seller.
Effective DifSerential Design Pressure,
P
(RCB
7.165).
For differential pressure design, the
effective differential design pressure is calculated as per RCB 7.165. For practical use TEMA
considers the seven combined design loading cases where pressure acts on the shell side
(p,
=
0),
on the tube side
(p,
=
0),
on both sides, and in each case with and without thermal expan-
sion; the seventh case is obtained for thermal expansion acting alone
(p,
=
0
and
p,
=
0).
Longitudinal Stress Induced in the Shell and Tube Bundle
After arriving at the tube-sheet thickness, it is necessary to determine the
stresses
induced in
the shell, channel, and tubes located at the periphery and interior of the tube bundle in the case
of fixed and floating tubesheet exchangers. The check for longitudinal stress induced
in
the
shell is calculated as per RCB-7.22. However, there is no procedure in TEMA to calculate the
bending stresses induced in the shell and both the longitudinal stress and bending stress
in
the
channel. The check for tube longitudinal stress both in tension and in compression in the tubes