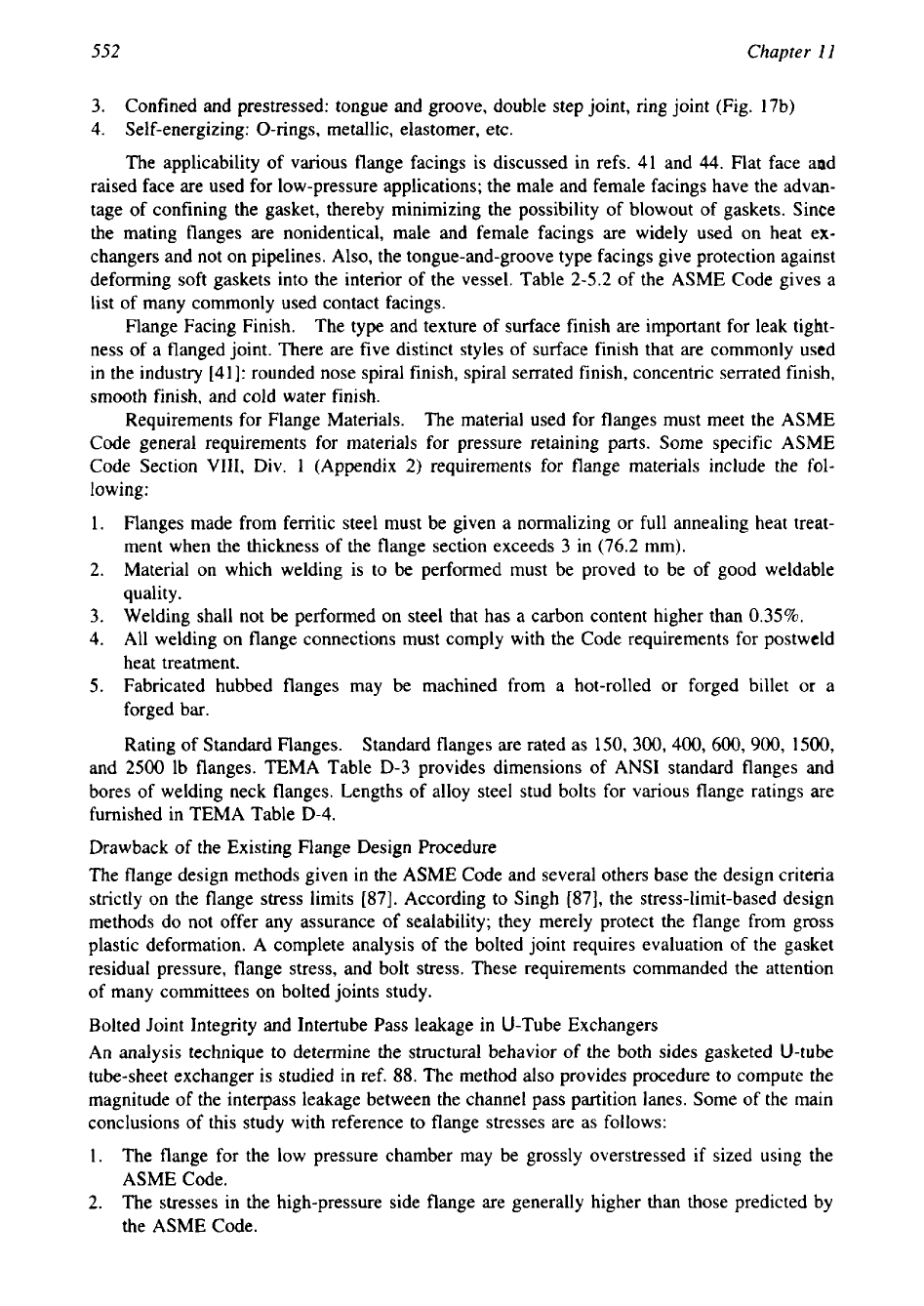
552
Chapter
11
3.
Confined and prestressed: tongue and groove, double step joint, ring joint (Fig. 17b)
4. Self-energizing: 0-rings, metallic, elastomer, etc.
The applicability of various flange facings is discussed in refs. 41 and 44. Flat face aQd
raised face are used for low-pressure applications; the male and female facings have the advan-
tage of confining the gasket, thereby minimizing the possibility of blowout of gaskets. Since
the mating flanges are nonidentical, male and female facings are widely used on heat ex-
changers and not on pipelines. Also, the tongue-and-groove type facings give protection against
deforming soft gaskets into the interior of the vessel. Table
2-5.2
of the ASME Code gives a
list of many commonly used contact facings.
Flange Facing Finish. The type and texture of surface finish are important for leak tight-
ness of a flangedjoint. There are five distinct styles of surface finish that are commonly used
in the industry [41]: rounded nose spiral finish, spiral serrated finish, concentric serrated finish,
smooth finish, and cold water finish.
Requirements for Flange Materials. The material used for flanges must meet the ASME
Code general requirements for materials for pressure retaining parts. Some specific ASME
Code Section VIII, Div. 1 (Appendix
2)
requirements for flange materials include the fol-
lowing:
1. Flanges made from ferritic steel must be given a normalizing or full annealing heat treat-
ment when the thickness of the flange section exceeds
3
in
(76.2
mm).
2.
Material on which welding is to be performed must be proved to be of good weldable
quality.
3.
Welding shall not be performed on steel that has a carbon content higher than 0.35%.
4.
All welding on flange connections must comply with the Code requirements for postweld
heat treatment.
5.
Fabricated hubbed flanges may be machined from a hot-rolled or forged billet
or
a
forged bar.
Rating of Standard Flanges. Standard flanges are rated as 150,300,400,600,900, 1500,
and
2500
lb flanges. TEMA Table D-3 provides dimensions of ANSI standard flanges and
bores of welding neck flanges. Lengths of alloy steel stud bolts for various flange ratings are
furnished in TEMA Table D-4.
Drawback of the Existing Flange Design Procedure
The flange design methods given in the ASME Code and several others base the design criteria
strictly on the flange stress limits [87]. According to Singh [87], the stress-limit-based design
methods do not offer any assurance of sealability; they merely protect the flange from gross
plastic deformation.
A
complete analysis of the bolted joint requires evaluation of the gasket
residual pressure, flange stress, and bolt stress. These requirements commanded the attention
of many committees on bolted joints study.
Bolted Joint Integrity and Intertube Pass leakage in U-Tube Exchangers
An analysis technique
to
determine the structural behavior of the both sides gasketed U-tube
tube-sheet exchanger is studied in ref.
88.
The method also provides procedure to compute the
magnitude of the interpass leakage between the channel pass partition lanes. Some
of
the main
conclusions
of
this study with reference to flange stresses are as follows:
1.
The
flange for the low pressure chamber may be grossly overstressed if sized using the
ASME Code.
2.
The stresses in the high-pressure side flange are generally higher than those predicted by
the ASME Code.