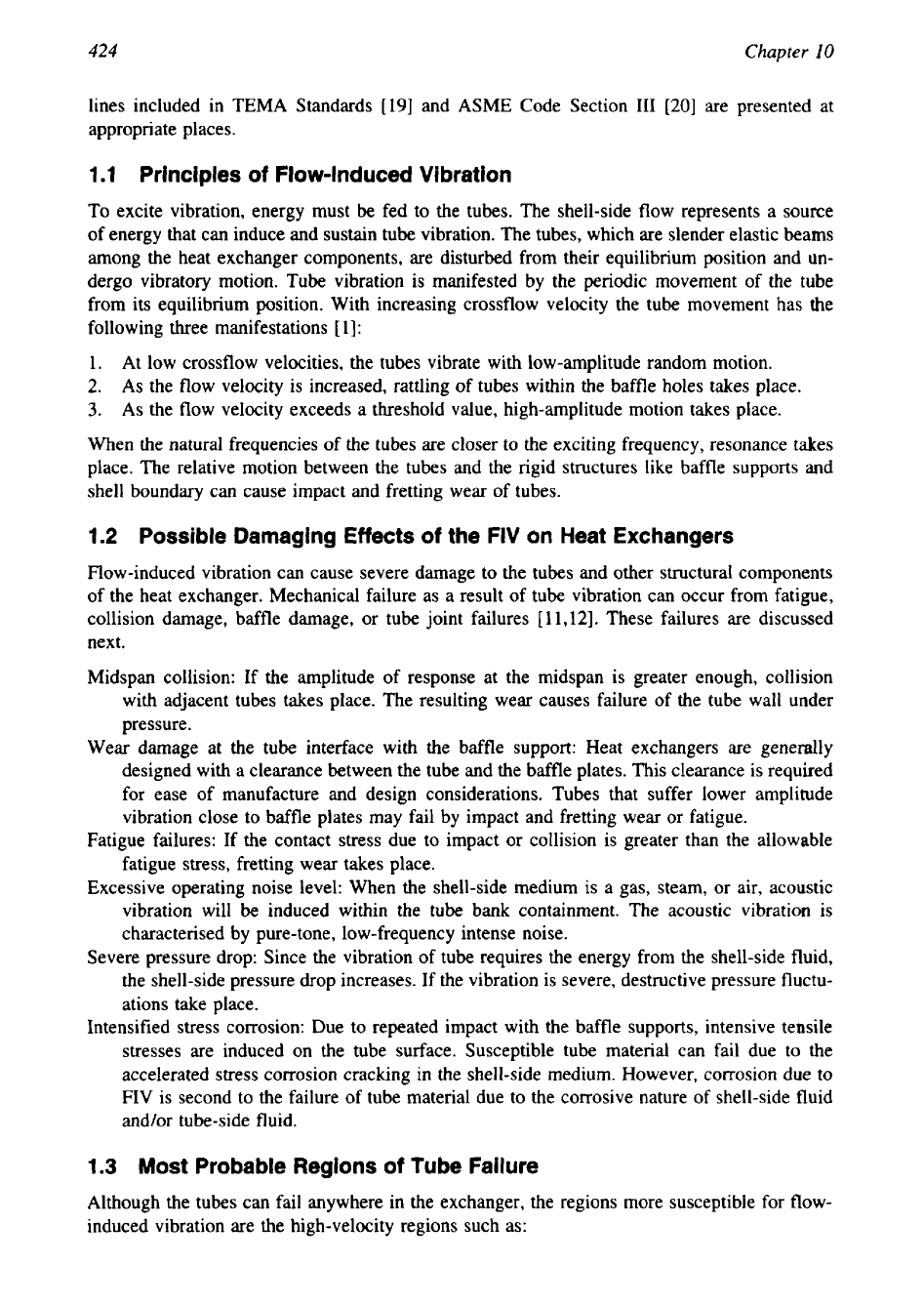
424 Chapter
10
lines included in TEMA Standards [19] and ASME Code Section 111 [20] are presented at
appropriate places.
1
.I
Principles
of
Flow-Induced Vibration
To excite vibration, energy must be fed to the tubes. The shell-side flow represents a source
of energy that can induce and sustain tube vibration. The tubes, which are slender elastic beams
among the heat exchanger components, are disturbed from their equilibrium position and un-
dergo vibratory motion. Tube vibration is manifested by the periodic movement of the tube
from its equilibrium position. With increasing crossflow velocity the tube movement has the
following three manifestations
[
11:
1. At low crossflow velocities, the tubes vibrate with low-amplitude random motion.
2.
As the flow velocity is increased, rattling of tubes within the baffle holes takes place.
3.
As the flow velocity exceeds a threshold value, high-amplitude motion takes place.
When the natural frequencies of the tubes are closer to the exciting frequency, resonance takes
place. The relative motion between the tubes and the rigid structures like baffle supports and
shell boundary can cause impact and fretting wear of tubes.
1.2
Possible Damaging Effects
of
the FIV
on
Heat Exchangers
Flow-induced vibration can cause severe damage to the tubes and other structural components
of the heat exchanger. Mechanical failure as
a
result of tube vibration can occur from fatigue,
collision damage, baffle damage, or tube joint failures
[
11,121. These failures are discussed
next.
Midspan collision: If the amplitude of response at the midspan is greater enough, collision
with adjacent tubes takes place. The resulting wear causes failure of the tube wall under
pressure.
Wear damage at the tube interface with the baffle support: Heat exchangers are generally
designed with a clearance between the tube and the baffle plates. This clearance is required
for ease of manufacture and design considerations. Tubes that suffer lower amplitude
vibration close
to
baffle plates may fail by impact and fretting wear or fatigue.
Fatigue failures: If the contact stress due to impact or collision is greater than the allowable
fatigue stress, fretting wear takes place.
Excessive operating noise level: When the shell-side medium is a gas, steam, or air, acoustic
vibration will be induced within the tube bank containment. The acoustic vibration is
characterised by pure-tone, low-frequency intense noise.
Severe pressure drop: Since the vibration of tube requires the energy from the shell-side fluid,
the shell-side pressure drop increases. If the vibration is severe, destructive pressure fluctu-
ations take place.
Intensified stress corrosion: Due to repeated impact with the baffle supports, intensive tensile
stresses are induced on the tube surface. Susceptible tube material can fail due to the
accelerated stress corrosion cracking in the shell-side medium. However, corrosion due to
FIV
is second to the failure of tube material due to the corrosive nature of shell-side fluid
and/or tube-side fluid.
1.3
Most Probable Regions
of
Tube Failure
Although the tubes can fail anywhere in the exchanger, the regions more susceptible for flow-
induced vibration are the high-velocity regions such
as: