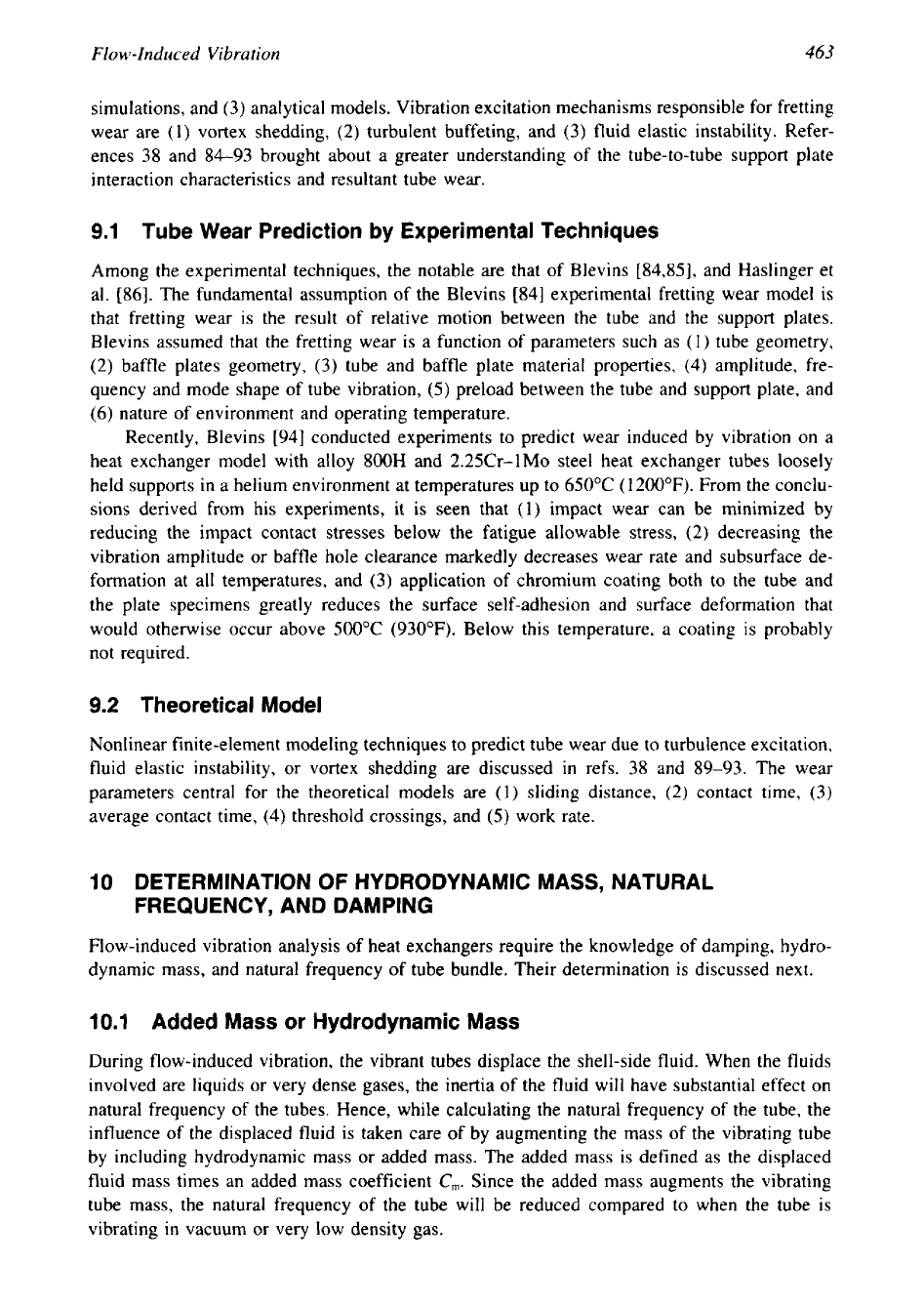
Flow-Induced
Vibration
463
simulations, and (3) analytical models. Vibration excitation mechanisms responsible for fretting
wear are (1) vortex shedding,
(2)
turbulent buffeting, and
(3)
fluid elastic instability. Refer-
ences 38 and 84-93 brought about a greater understanding of the tube-to-tube support plate
interaction characteristics and resultant tube wear.
9.1
Tube Wear Prediction by Experimental Techniques
Among the experimental techniques, the notable are that of Blevins [84,85], and Haslinger et
al. [86]. The fundamental assumption of the Blevins [84] experimental fretting wear model is
that fretting wear is the result of relative motion between the tube and the support plates.
Blevins assumed that the fretting wear is a function of parameters such as
(1)
tube geometry,
(2) baffle plates geometry,
(3)
tube and baffle plate material properties, (4) amplitude, fre-
quency and mode shape of tube vibration,
(5)
preload between the tube and support plate, and
(6) nature of environment and operating temperature.
Recently, Blevins [94] conducted experiments to predict wear induced by vibration on a
heat exchanger model with alloy 800H and 2.25Cr-1Mo steel heat exchanger tubes loosely
held supports
in
a helium environment at temperatures up to
650°C
(1200°F).
From the conclu-
sions derived from his experiments, it is seen that
(1)
impact wear can be minimized by
reducing the impact contact stresses below the fatigue allowable stress,
(2)
decreasing the
vibration amplitude or baffle hole clearance markedly decreases wear rate and subsurface de-
formation at all temperatures, and
(3)
application of chromium coating both to the tube and
the plate specimens greatly reduces the surface self-adhesion and surface deformation that
would otherwise occur above
500°C
(930°F). Below this temperature, a coating is probably
not required.
9.2
Theoretical Model
Nonlinear finite-element modeling techniques to predict tube wear due to turbulence excitation,
fluid elastic instability, or vortex shedding are discussed in refs. 38 and 89-93. The wear
parameters central for the theoretical models are
(1)
sliding distance,
(2)
contact time, (3)
average contact time, (4) threshold crossings, and
(5)
work rate.
10
DETERMINATION
OF
HYDRODYNAMIC MASS, NATURAL
FREQUENCY, AND DAMPING
Flow-induced vibration analysis of heat exchangers require the knowledge of damping, hydro-
dynamic mass, and natural frequency of tube bundle. Their determination is discussed next.
10.1
Added
Mass
or
Hydrodynamic
Mass
During flow-induced vibration, the vibrant tubes displace the shell-side fluid. When the fluids
involved are liquids or very dense gases, the inertia of the fluid will have substantial effect on
natural frequency of the tubes. Hence, while calculating the natural frequency of the tube, the
influence
of
the displaced fluid is taken care
of
by augmenting the mass of the vibrating tube
by including hydrodynamic mass or added mass. The added mass is defined as the displaced
fluid mass times an added mass coefficient
C,.
Since the added mass augments the vibrating
tube mass, the natural frequency of the tube will be reduced compared to when the tube is
vibrating in vacuum or very low density gas.