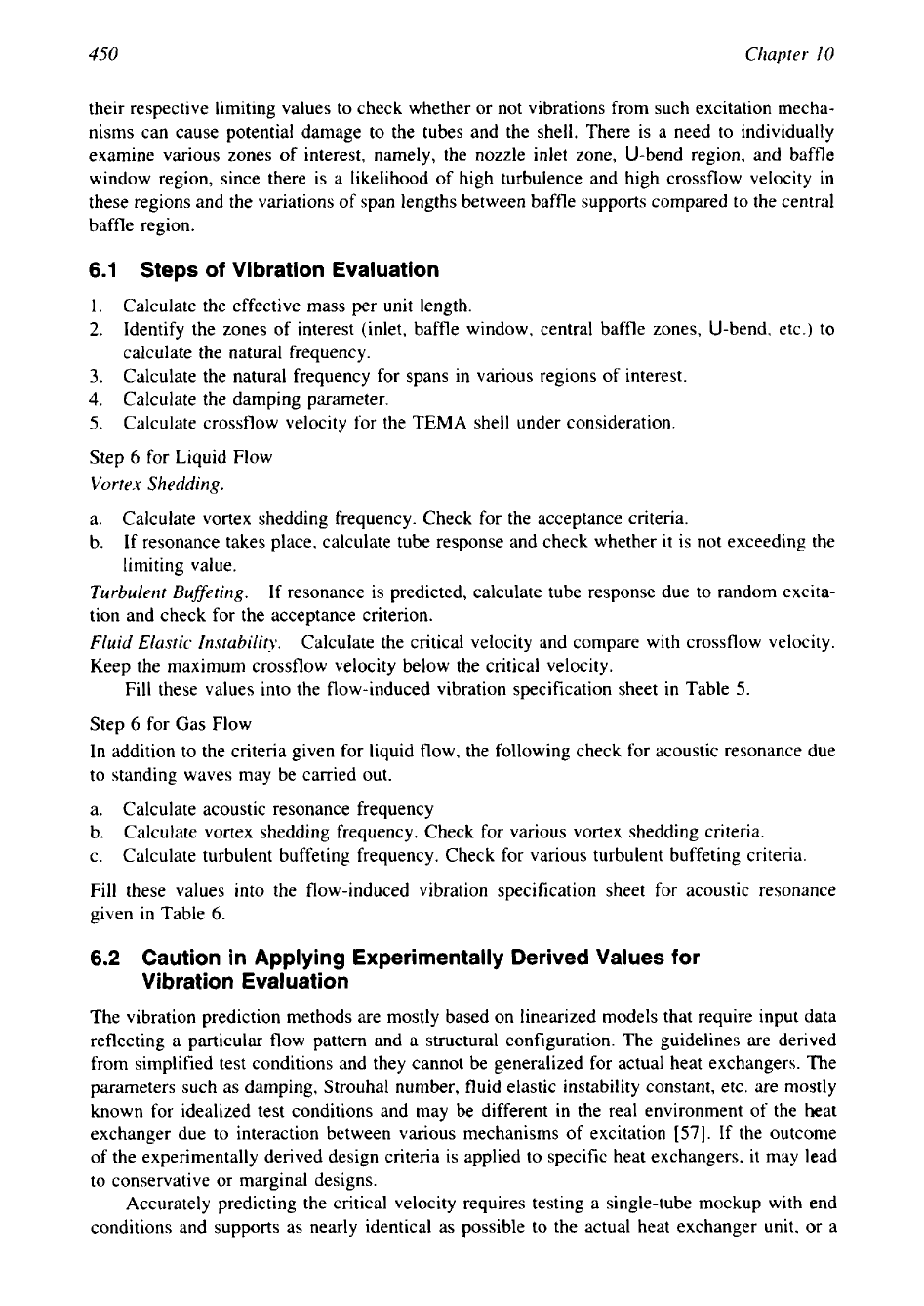
450
Chapter
I0
their respective limiting values to check whether or not vibrations from such excitation mecha-
nisms can cause potential damage to the tubes and the shell. There is a need to individually
examine various zones of interest, namely, the nozzle inlet zone, U-bend region, and baffle
window region, since there is a likelihood of high turbulence and high crossflow velocity
in
these regions and the variations of span lengths between baffle supports compared to the central
baffle region.
6.1
Steps
of
Vibration Evaluation
1.
Calculate the effective mass per unit length.
2.
Identify the zones
of
interest (inlet, baffle window, central baffle zones, U-bend, etc.) to
calculate the natural frequency.
3.
Calculate the natural frequency for spans in various regions of interest.
4. Calculate the damping parameter.
5.
Calculate crossflow velocity for the
TEMA
shell under consideration.
Step
6
for Liquid Flow
Vortex Shedding.
a.
Calculate vortex shedding frequency. Check for the acceptance criteria.
b.
If resonance takes place, calculate tube response and check whether it is not exceeding the
limiting value.
Turbulent Buffeting.
If resonance is predicted, calculate tube response due to random excita-
tion and check for the acceptance criterion.
Fluid Elastic Instability.
Calculate the critical velocity and compare with crossflow velocity.
Keep the maximum crossflow velocity below the critical velocity.
Fill these values into the flow-induced vibration specification sheet in Table
5.
Step
6
for Gas Flow
In addition to the criteria given for liquid flow, the following check for acoustic resonance due
to standing waves may be carried out.
a. Calculate acoustic resonance frequency
b. Calculate vortex shedding frequency. Check for various vortex shedding criteria.
c. Calculate turbulent buffeting frequency. Check for various turbulent buffeting criteria.
Fill these values into the flow-induced vibration specification sheet for acoustic resonance
given in Table
6.
6.2
Caution in Applying Experimentally Derived Values for
Vibration Evaluation
The vibration prediction methods are mostly based on linearized models that require input data
reflecting a particular flow pattern and a structural configuration. The guidelines are derived
from simplified test conditions and they cannot be generalized for actual heat exchangers. The
parameters such as damping, Strouhal number, fluid elastic instability constant, etc. are mostly
known for idealized test conditions and may be different in the real environment of the heat
exchanger due to interaction between various mechanisms of excitation
[57].
If the outcome
of the experimentally derived design criteria is applied to specific heat exchangers, it may lead
to conservative or marginal designs.
Accurately predicting the critical velocity requires testing a single-tube mockup with end
conditions and supports as nearly identical as possible to the actual heat exchanger unit, or a