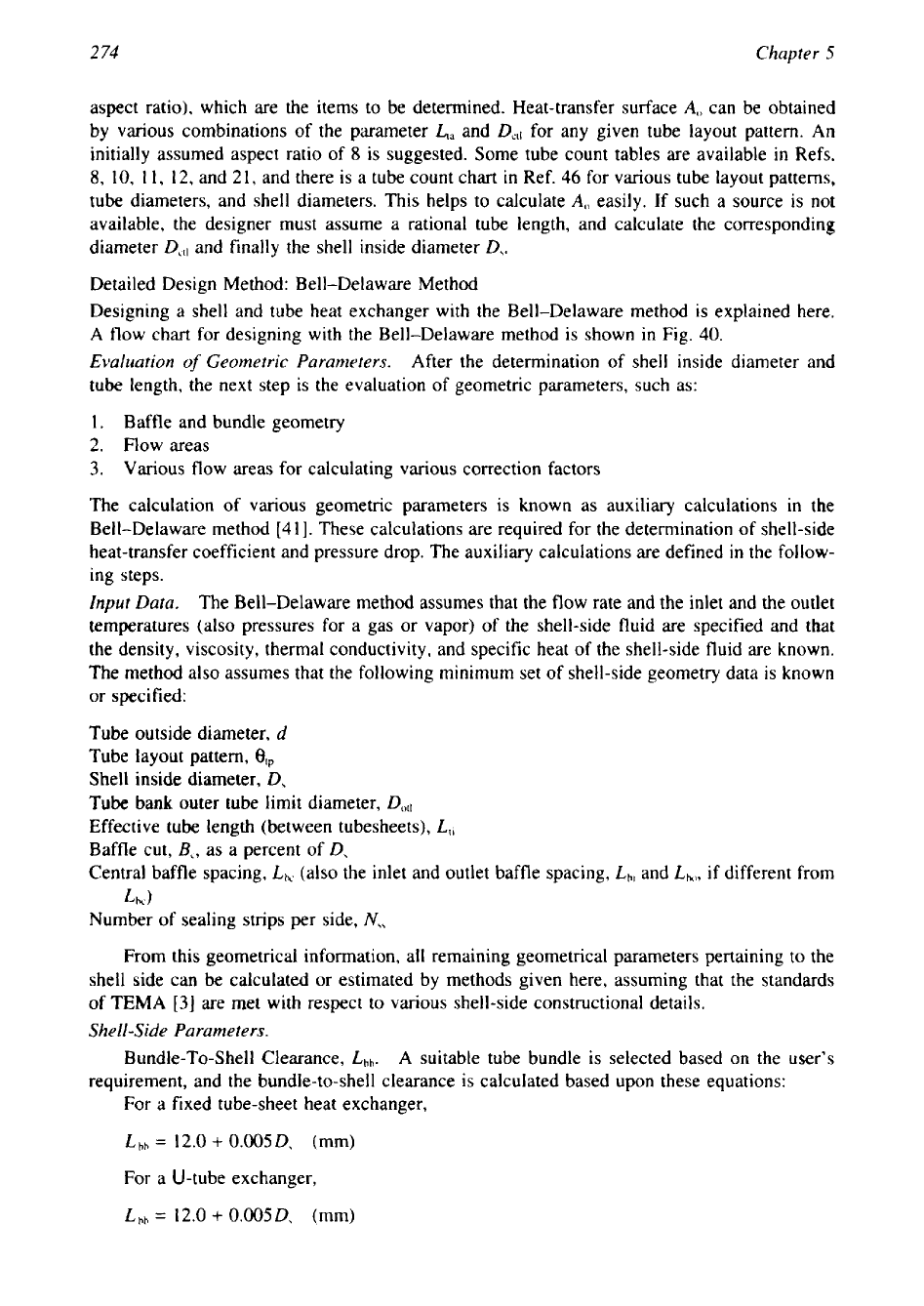
2
74
Chapter
5
aspect ratio), which are the items to be determined. Heat-transfer surface
A,,
can be obtained
by various combinations of the parameter
L,,
and
D,,,
for any given tube layout pattern. An
initially assumed aspect ratio of
8
is suggested. Some tube count tables are available
in
Refs.
8,
10,
1
1,
12, and
2
1,
and there is a tube count chart
in
Ref.
46
for various tube layout patterns,
tube diameters, and shell diameters. This helps to calculate
A,,
easily. If such a source is not
available, the designer must assume a rational tube length, and calculate the corresponding
diameter
Dc,,
and finally the shell inside diameter
D,.
Detailed Design Method: Bell-Delaware Method
Designing a shell and tube heat exchanger with the Bell-Delaware method is explained here.
A
flow chart for designing with the Bell-Delaware method is shown
in
Fig.
40.
Evaluation
of
Geometric
Parameters.
After the determination of shell inside diameter and
tube
length, the next step is the evaluation of geometric parameters, such as:
1.
Baffle and bundle geometry
2.
Flow areas
3.
Various flow areas for calculating various correction factors
The calculation of various geometric parameters is known as auxiliary calculations in the
Bell-Delaware method
[4
I].
These calculations are required for the determination of shell-side
heat-transfer coefficient and pressure drop. The auxiliary calculations are defined
in
the follow-
ing steps.
Input
Data.
The Bell-Delaware method assumes that the flow rate and the inlet and the outlet
temperatures (also pressures for a gas or vapor) of the shell-side fluid are specified and that
the density, viscosity, thermal conductivity, and specific heat of the shell-side fluid are known.
The method also assumes that the following minimum set of shell-side geometry data is known
or specified
:
Tube outside diameter,
d
Tube layout pattern,
et,
Shell inside diameter,
D,
Tube
bank outer tube limit diameter,
Doll
Effective tube length (between tubesheets),
L,,
Baffle cut,
B,,
as a percent of
D,
Central baffle spacing,
Lhc.
(also the inlet and outlet baffle spacing,
Lh,
and
Lh,,
if
different from
Lhc)
Number of sealing strips per side,
N,,
From this geometrical information, all remaining geometrical parameters pertaining to the
shell side can
be
calculated or estimated by methods given here, assuming that the standards
of
TEMA
[3]
are met with respect to various shell-side constructional details.
Shell-Side Parameters.
Bundle-To-Shell Clearance,
Lhh.
A suitable tube bundle is selected based
on
the user’s
requirement, and the bundle-to-shell clearance is calculated based upon these equations:
For a fixed tube-sheet heat exchanger,
Lhh
=
12.0
+
O.O05D,
(mm)
For
a U-tube exchanger,
Lh,
=
12.0
+
0.005D,
(mm)