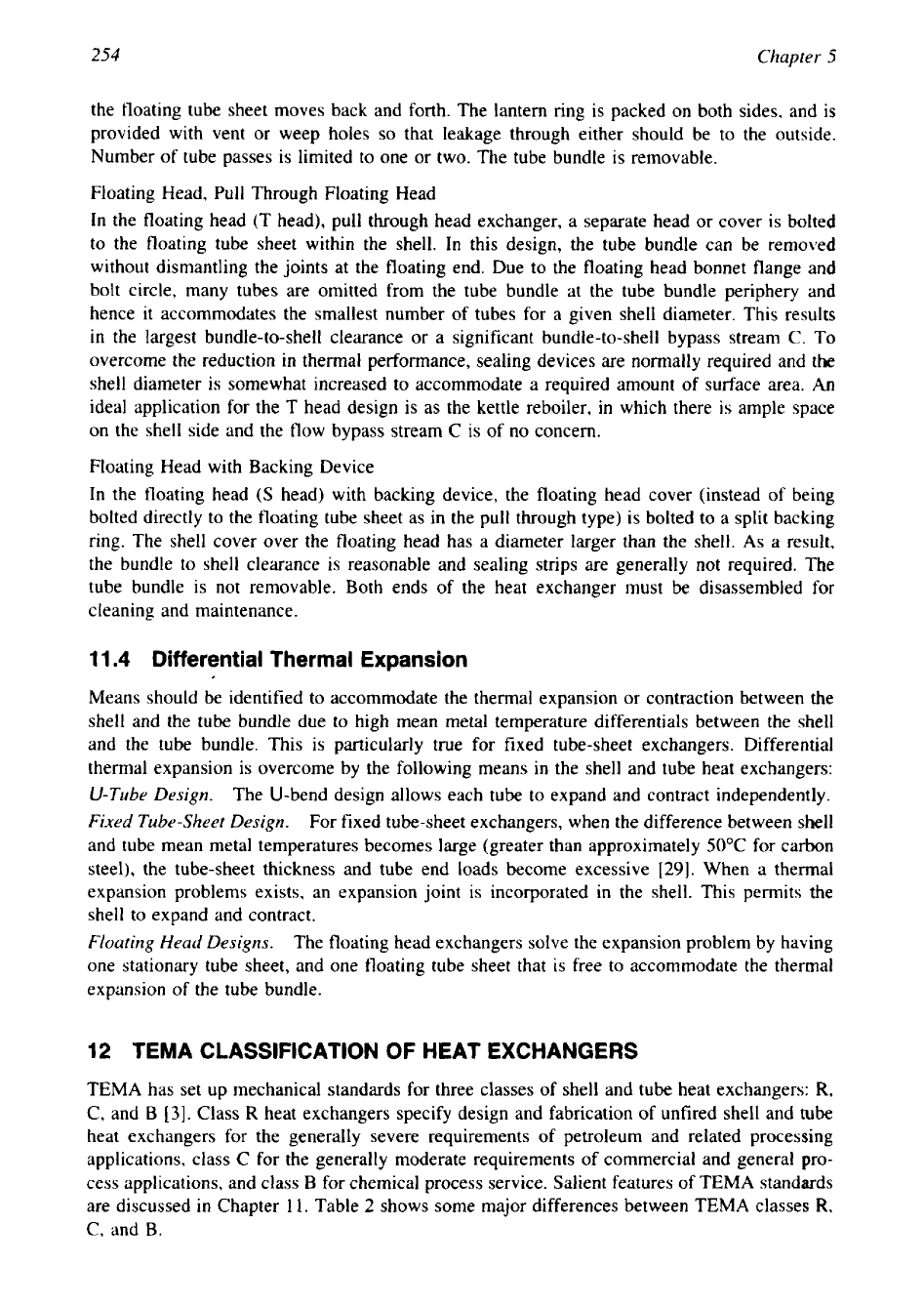
254
Chapter
5
the floating tube sheet moves back and forth. The lantern ring is packed on both sides, and
is
provided with vent or weep holes
so
that leakage through either should be to the outside.
Number of tube passes is limited to one or two. The tube bundle is removable.
Floating Head, Pull Through Floating Head
In the floating head (T head), pull through head exchanger, a separate head or cover is bolted
to the floating tube sheet within the shell. In this design, the tube bundle can be removed
without dismantling the joints at the floating end. Due to the floating head bonnet flange and
bolt circle, many tubes are omitted from the tube bundle at the tube bundle periphery and
hence it accommodates the smallest number of tubes for a given shell diameter. This results
in the largest bundle-to-shell clearance or a significant bundle-to-shell bypass stream
C.
To
overcome the reduction in thermal performance, sealing devices are normally required and
the
shell diameter is somewhat increased to accommodate a required amount of surface area.
An
ideal application for the T head design is as the kettle reboiler, in which there
is
ample space
on the shell side and the flow bypass stream
C
is of no concern.
Floating Head with Backing Device
In the floating head
(S
head) with backing device, the floating head cover (instead of being
bolted directly to the floating tube sheet as in the pull through type) is bolted to a split backing
ring. The shell cover over the floating head has
a
diameter larger than the shell.
As
a result,
the bundle to shell clearance is reasonable and sealing strips are generally
not
required. The
tube bundle is not removable. Both ends of the heat exchanger must be disassembled for
cleaning and maintenance.
11.4
Differential Thermal Expansion
Means should be identified to accommodate the thermal expansion or contraction between the
shell and the tube bundle due to high mean metal temperature differentials between the shell
and the tube bundle. This is particularly true for fixed tube-sheet exchangers. Differential
thermal expansion is overcome by the following means in the shell and tube heat exchangers:
U-Tube Design.
The U-bend design allows each tube to expand and contract independently.
Fixed Tube-Sheet Design.
For fixed tube-sheet exchangers, when the difference between shell
and tube mean metal temperatures becomes large (greater than approximately
50°C
for carbon
steel), the tube-sheet thickness and tube end loads become excessive [29]. When a thermal
expansion problems exists, an expansion joint is incorporated in the shell. This permits the
shell to expand and contract.
Flouting Head Designs.
The floating head exchangers solve the expansion problem by having
one stationary tube sheet, and one floating tube sheet that
is
free to accommodate the thermal
expansion of the tube bundle.
12
TEMA CLASSIFICATION OF HEAT EXCHANGERS
TEMA has set up mechanical standards for three classes of shell and tube heat exchangers:
R,
C,
and
B
[3].
Class
R
heat exchangers specify design and fabrication of unfired shell and tube
heat exchangers for the generally severe requirements of petroleum and related processing
applications, class
C
for the generally moderate requirements of commercial and general
pro-
cess applications, and class B for chemical process service. Salient features of TEMA standards
are discussed in Chapter 11. Table
2
shows some major differences between TEMA classes
R,
C.
and B.