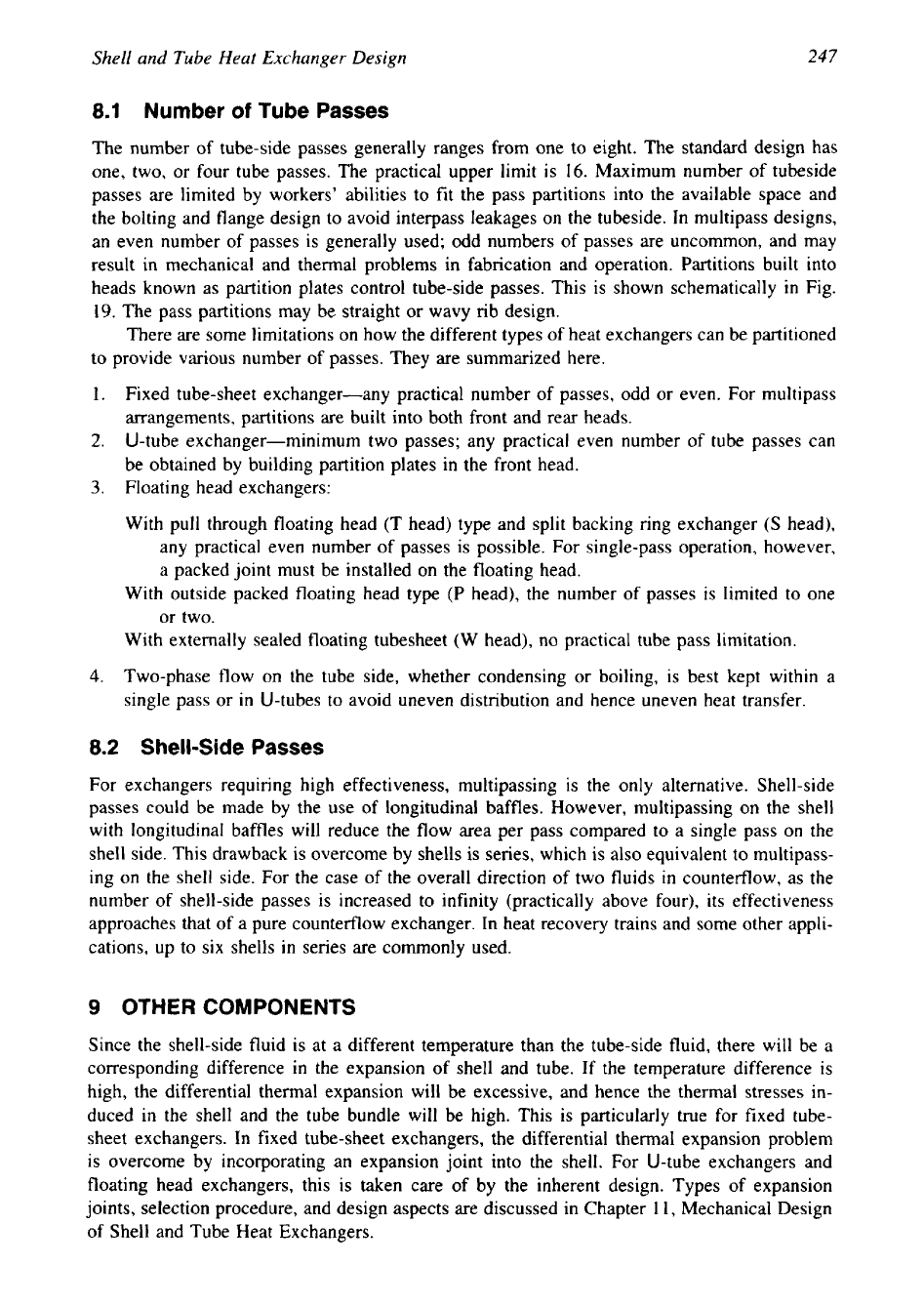
Shell and Tube Heat Exchanger Design
247
8.1
Number
of
Tube
Passes
The number
of
tube-side passes generally ranges from one to eight. The standard design has
one, two, or four tube passes. The practical upper limit is 16. Maximum number of tubeside
passes are limited by workers’ abilities to fit the pass partitions into the available space and
the bolting and flange design to avoid interpass leakages on the tubeside. In multipass designs,
an even number of passes is generally used; odd numbers of passes are uncommon, and may
result in mechanical and thermal problems in fabrication and operation. Partitions built into
heads known as partition plates control tube-side passes. This is shown schematically in Fig.
19. The pass partitions may be straight or wavy rib design.
There are some limitations on how the different types of heat exchangers can be partitioned
to provide various number of passes. They are summarized here.
1.
Fixed tube-sheet exchanger-any practical number of passes, odd or even. For multipass
arrangements, partitions are built into both front and rear heads.
2.
U-tube exchanger-minimum two passes; any practical even number of tube passes can
be obtained by building partition plates in the front head.
3.
Floating head exchangers:
With pull through floating head (T head) type and split backing ring exchanger
(S
head),
any practical even number of passes is possible. For single-pass operation, however,
a packed joint must be installed on the floating head.
With outside packed floating head type (P head), the number of passes is limited to one
or two.
With externally sealed floating tubesheet (W head), no practical tube pass limitation.
4.
Two-phase flow on the tube side, whether condensing or boiling, is best kept within a
single pass or in U-tubes to avoid uneven distribution and hence uneven heat transfer.
8.2
Shell-Side Passes
For exchangers requiring high effectiveness, multipassing is the only alternative. Shell-side
passes could be made by the use of longitudinal baffles. However, multipassing on the shell
with longitudinal baffles will reduce the flow area per pass compared to a single pass on the
shell side. This drawback is overcome by shells is series, which is also equivalent to multipass-
ing on the shell side. For the case
of
the overall direction of two fluids in counterflow, as the
number of shell-side passes is increased to infinity (practically above four), its effectiveness
approaches that of a pure counterflow exchanger. In heat recovery trains and some other appli-
cations, up to six shells in series are commonly used.
9
OTHER COMPONENTS
Since the shell-side fluid is at a different temperature than the tube-side fluid, there will be a
corresponding difference in the expansion of shell and tube. If the temperature difference is
high, the differential thermal expansion will be excessive, and hence the thermal stresses in-
duced in the shell and the tube bundle will be high. This is particularly true for fixed tube-
sheet exchangers. In fixed tube-sheet exchangers, the differential thermal expansion problem
is overcome by incorporating an expansion joint into the shell. For U-tube exchangers and
floating head exchangers, this is taken care of by the inherent design. Types
of
expansion
joints, selection procedure, and design aspects are discussed in Chapter 1
1,
Mechanical Design
of Shell and Tube Heat Exchangers.