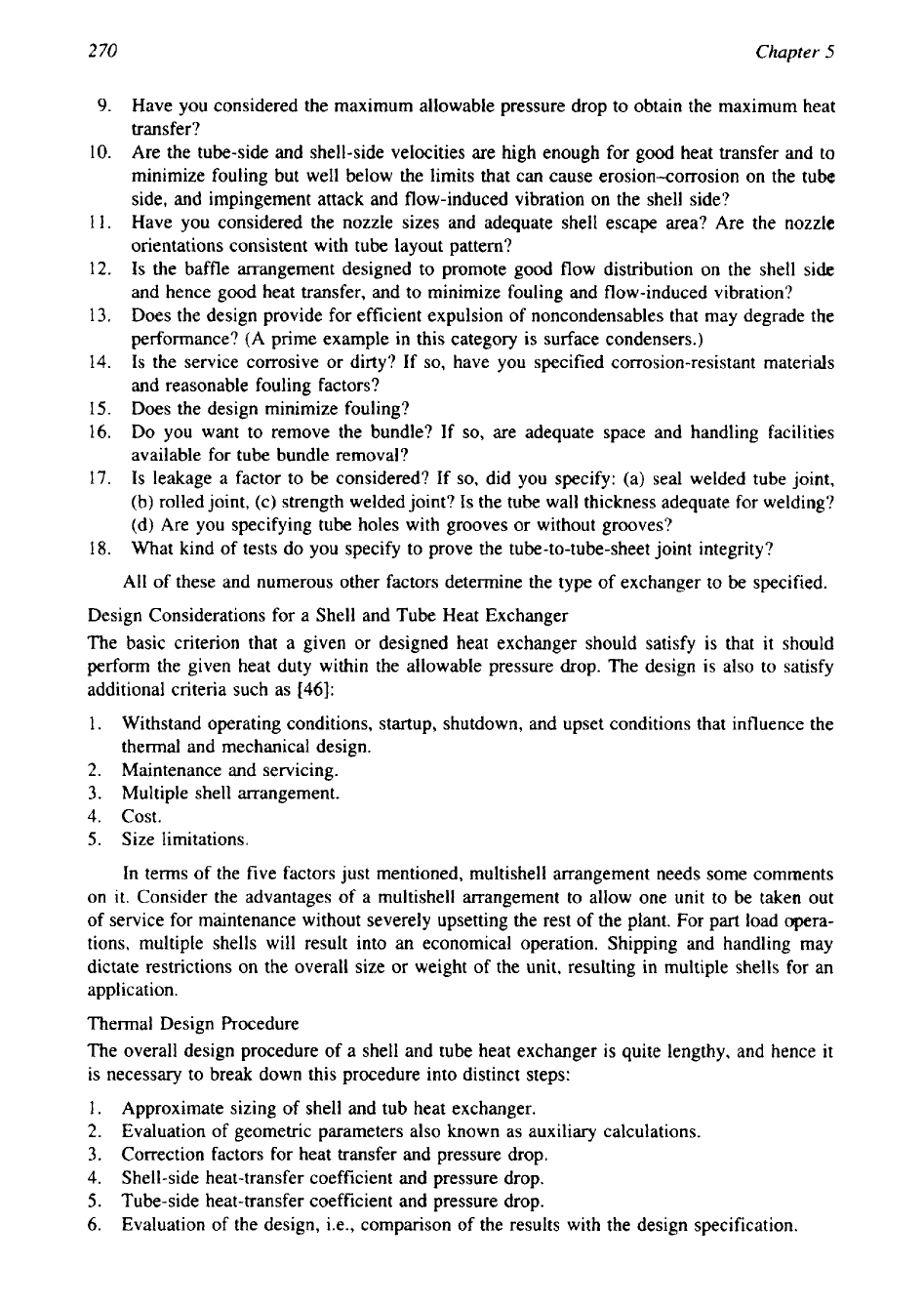
2
70
Chapter
5
9.
Have
you
considered the maximum allowable pressure drop to obtain the maximum heat
transfer?
10.
Are the tube-side and shell-side velocities are high enough for good heat transfer and
to
minimize fouling but well below the limits that can cause erosion-corrosion on the tube
side, and impingement attack and flow-induced vibration on the shell side?
11.
Have you considered the nozzle sizes and adequate shell escape area? Are the nozzle
orientations consistent with tube layout pattern?
12.
Is
the baffle arrangement designed to promote good flow distribution on the shell side
and hence good heat transfer, and to minimize fouling and flow-induced vibration?
13.
Does the design provide for efficient expulsion of noncondensables that may degrade the
performance?
(A
prime example in this category is surface condensers.)
14.
Is
the service corrosive or dirty? If
so,
have you specified corrosion-resistant materials
and reasonable fouling factors?
15.
Does the design minimize fouling?
16.
Do you want to remove the bundle? If
so,
are adequate space and handling facilities
available for tube bundle removal?
17.
Is
leakage a factor to be considered? If
so,
did you specify: (a) seal welded tube joint,
(b) rolled joint, (c) strength welded joint?
Is
the tube wall thickness adequate for welding?
(d) Are you specifying tube holes with grooves or without grooves?
18.
What kind of tests do you specify to prove the tube-to-tube-sheet joint integrity?
All of these and numerous other factors determine the type of exchanger to be specified.
Design Considerations for a Shell and Tube Heat Exchanger
The basic criterion that a given or designed heat exchanger should satisfy is that it should
perform the given heat duty within the allowable pressure drop. The design is also to satisfy
additional criteria such as [46]:
1.
Withstand operating conditions, startup, shutdown, and upset conditions that influence the
thermal and mechanical design.
2.
Maintenance and servicing.
3.
Multiple shell arrangement.
4. cost.
5.
Size limitations.
In terms of the five factors just mentioned, multishell arrangement needs some comments
on it. Consider the advantages of a multishell arrangement to allow one unit to be taken out
of
service for maintenance without severely upsetting the rest of the plant.
For
part load opera-
tions, multiple shells will result into
an
economical operation. Shipping and handling may
dictate restrictions on the overall size or weight of the unit, resulting in multiple shells for an
application.
Thermal Design Procedure
The overall design procedure of a shell and tube heat exchanger is quite lengthy, and hence it
is necessary to break down this procedure into distinct steps:
1.
Approximate sizing of shell and tub heat exchanger.
2.
Evaluation of geometric parameters also known as auxiliary calculations.
3.
Correction factors for heat transfer and pressure drop.
4.
Shell-side heat-transfer coefficient and pressure drop.
5.
Tube-side heat-transfer coefficient and pressure drop.
6.
Evaluation of the design, i.e., comparison of the results with the design specification,