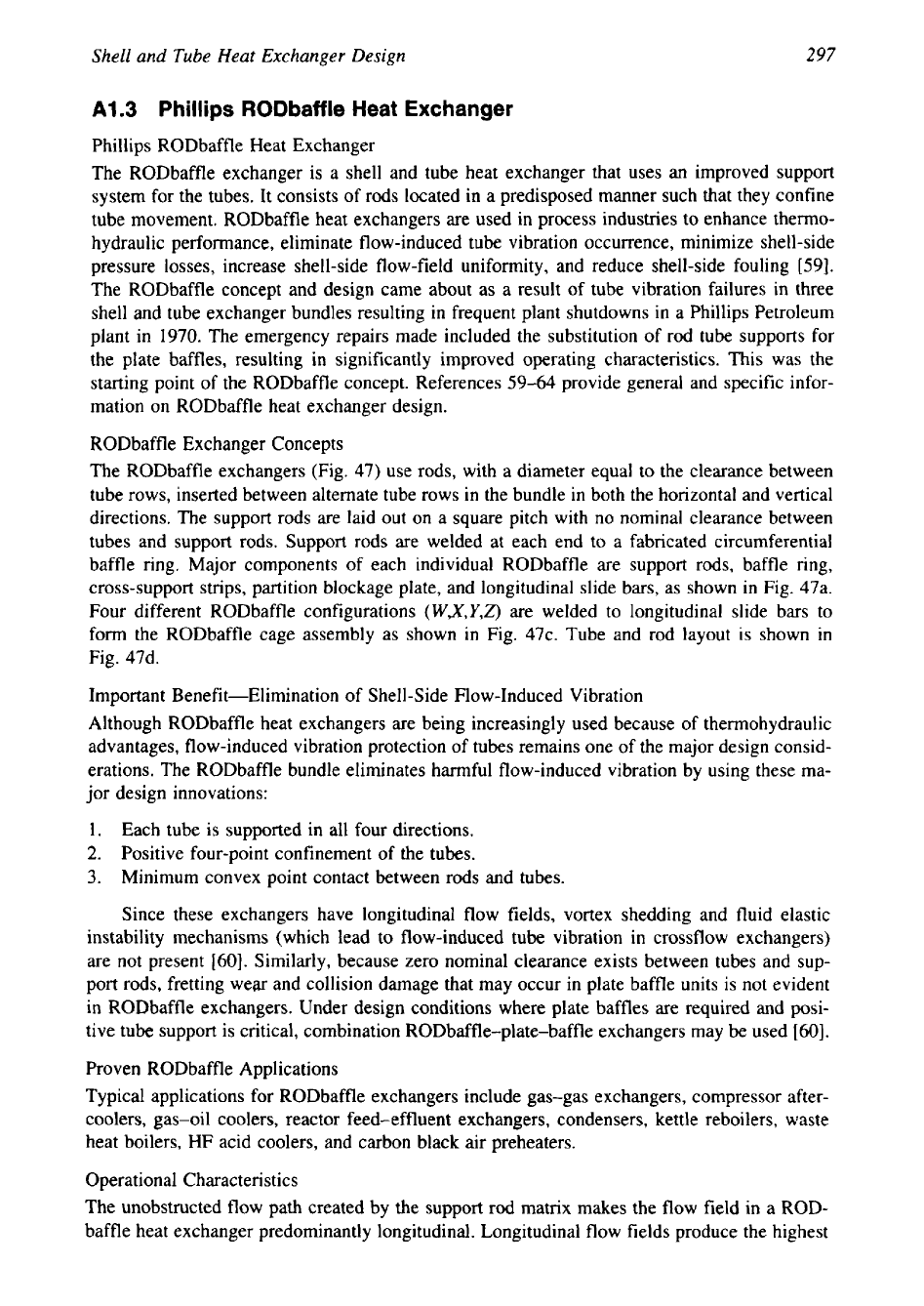
297
Shell and Tube Heat Exchanger Design
Al.3
Phillips
RODbaffle
Heat Exchanger
Phillips RODbaffle Heat Exchanger
The RODbaffle exchanger is a shell and tube heat exchanger that uses an improved support
system for the tubes. It consists of rods located in a predisposed manner such that they confine
tube movement. RODbaffle heat exchangers are used in process industries to enhance thermo-
hydraulic performance, eliminate flow-induced tube vibration occurrence, minimize shell-side
pressure losses, increase shell-side flow-field uniformity, and reduce shell-side fouling [59].
The RODbaffle concept and design came about as a result of tube vibration failures in three
shell and tube exchanger bundles resulting in frequent plant shutdowns in a Phillips Petroleum
plant in 1970. The emergency repairs made included the substitution of rod tube supports for
the plate baffles, resulting in significantly improved operating characteristics. This was the
starting point of the RODbaffle concept. References 59-64 provide general and specific infor-
mation on RODbaffle heat exchanger design.
RODbaffle Exchanger Concepts
The RODbaffle exchangers (Fig. 47) use rods, with a diameter equal to the clearance between
tube rows, inserted between alternate tube rows in the bundle in both the horizontal and vertical
directions. The support rods are laid out on a square pitch with no nominal clearance between
tubes and support rods. Support rods are welded at each end to a fabricated circumferential
baffle ring. Major components of each individual RODbaffle are support rods, baffle ring,
cross-support strips, partition blockage plate, and longitudinal slide bars, as shown in Fig. 47a.
Four different RODbaffle configurations
(W,X,Y,Z)
are welded to longitudinal slide bars to
form the RODbaffle cage assembly as shown in Fig. 47c. Tube and rod layout is shown in
Fig. 47d.
Important Benefit-Elimination of Shell-Side Flow-Induced Vibration
Although RODbaffle heat exchangers are being increasingly used because of thermohydraulic
advantages, flow-induced vibration protection of tubes remains one of the major design consid-
erations. The RODbaffle bundle eliminates harmful flow-induced vibration by using these ma-
jor design innovations:
1.
Each tube is supported in all four directions.
2.
Positive four-point confinement of the tubes.
3.
Minimum convex point contact between rods and tubes.
Since these exchangers have longitudinal flow fields, vortex shedding and fluid elastic
instability mechanisms (which lead to flow-induced
tube
vibration in crossflow exchangers)
are not present
[60].
Similarly, because zero nominal clearance exists between tubes and sup-
port rods, fretting wear and collision damage that may occur in plate baffle units is not evident
in RODbaffle exchangers. Under design conditions where plate baffles are required and posi-
tive tube support is critical, combination RODbaffle-plate-baffle exchangers may be used
[60].
Proven RODbaffle Applications
Typical applications for RODbaffle exchangers include gas-gas exchangers, compressor after-
coolers, gas-oil coolers, reactor feed-effluent exchangers, condensers, kettle reboilers, waste
heat boilers, HF acid coolers, and carbon black air preheaters.
Operational Characteristics
The unobstructed flow path created by the support rod matrix makes the flow field in a ROD-
baffle heat exchanger predominantly longitudinal. Longitudinal flow fields produce the highest