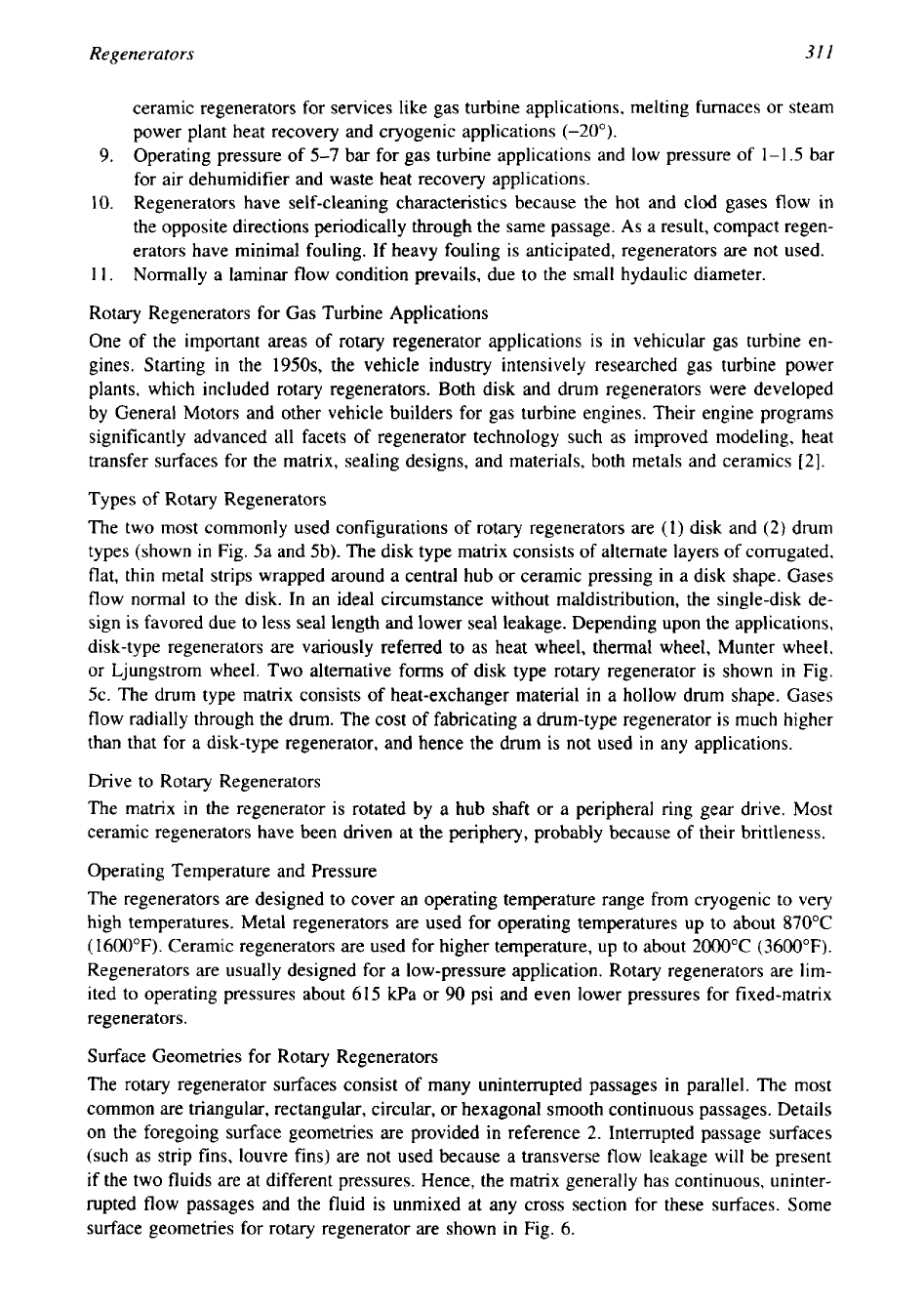
Regenerators
31
I
ceramic regenerators for services like gas turbine applications, melting furnaces or steam
power plant heat recovery and cryogenic applications
(-20").
9.
Operating pressure of
5-7
bar for gas turbine applications and low pressure of 1-1.5 bar
for air dehumidifier and waste heat recovery applications.
10.
Regenerators have self-cleaning characteristics because the hot and clod gases flow in
the opposite directions periodically through the same passage. As a result, compact regen-
erators have minimal fouling.
If
heavy fouling is anticipated, regenerators are not used.
11.
Normally a lamina flow condition prevails, due to the small hydaulic diameter.
Rotary Regenerators for Gas Turbine Applications
One of the important areas of rotary regenerator applications
is
in
vehicular gas turbine en-
gines. Starting
in
the 1950s, the vehicle industry intensively researched gas turbine power
plants, which included rotary regenerators. Both disk and drum regenerators were developed
by General Motors and other vehicle builders for gas turbine engines. Their engine programs
significantly advanced all facets of regenerator technology such as improved modeling, heat
transfer surfaces for the matrix, sealing designs, and materials, both metals and ceramics
[2].
Types of Rotary Regenerators
The two most commonly used configurations of rotary regenerators are
(1)
disk and
(2)
drum
types (shown in Fig. 5a and 5b). The disk type matrix consists of alternate layers of corrugated,
flat, thin metal strips wrapped around a central hub or ceramic pressing in a disk shape. Gases
flow normal to the disk. In an ideal circumstance without maldistribution, the single-disk de-
sign is favored due to less seal length and lower seal leakage. Depending upon the applications,
disk-type regenerators are variously referred to as heat wheel, thermal wheel, Munter wheel,
or Ljungstrom wheel. Two alternative forms of disk type rotary regenerator is shown in Fig.
5c. The drum type matrix consists of heat-exchanger material in a hollow drum shape. Gases
flow radially through the drum. The cost of fabricating a drum-type regenerator is much higher
than that for a disk-type regenerator, and hence the drum is not used in any applications.
Drive to Rotary Regenerators
The matrix in the regenerator is rotated by a hub shaft or a peripheral ring gear drive.
Most
ceramic regenerators have been driven at the periphery, probably because of their brittleness.
Operating Temperature and Pressure
The regenerators are designed to cover an operating temperature range from cryogenic to very
high temperatures. Metal regenerators are used for operating temperatures up to about 870°C
(1600°F). Ceramic regenerators are used for higher temperature, up to about
2000°C
(3600°F).
Regenerators are usually designed for a low-pressure application. Rotary regenerators are lim-
ited to operating pressures about 615 kPa or
90
psi and even lower pressures for fixed-matrix
regenerators.
Surface Geometries for Rotary Regenerators
The rotary regenerator surfaces consist of many uninterrupted passages in parallel. The most
common are triangular, rectangular, circular, or hexagonal smooth continuous passages. Details
on the foregoing surface geometries are provided in reference
2.
Interrupted passage surfaces
(such as strip fins, louvre fins) are not used because a transverse flow leakage will be present
if the two fluids are at different pressures. Hence, the matrix generally has continuous, uninter-
rupted flow passages and the fluid is unmixed at any cross section for these surfaces. Some
surface geometries for rotary regenerator are shown in Fig. 6.