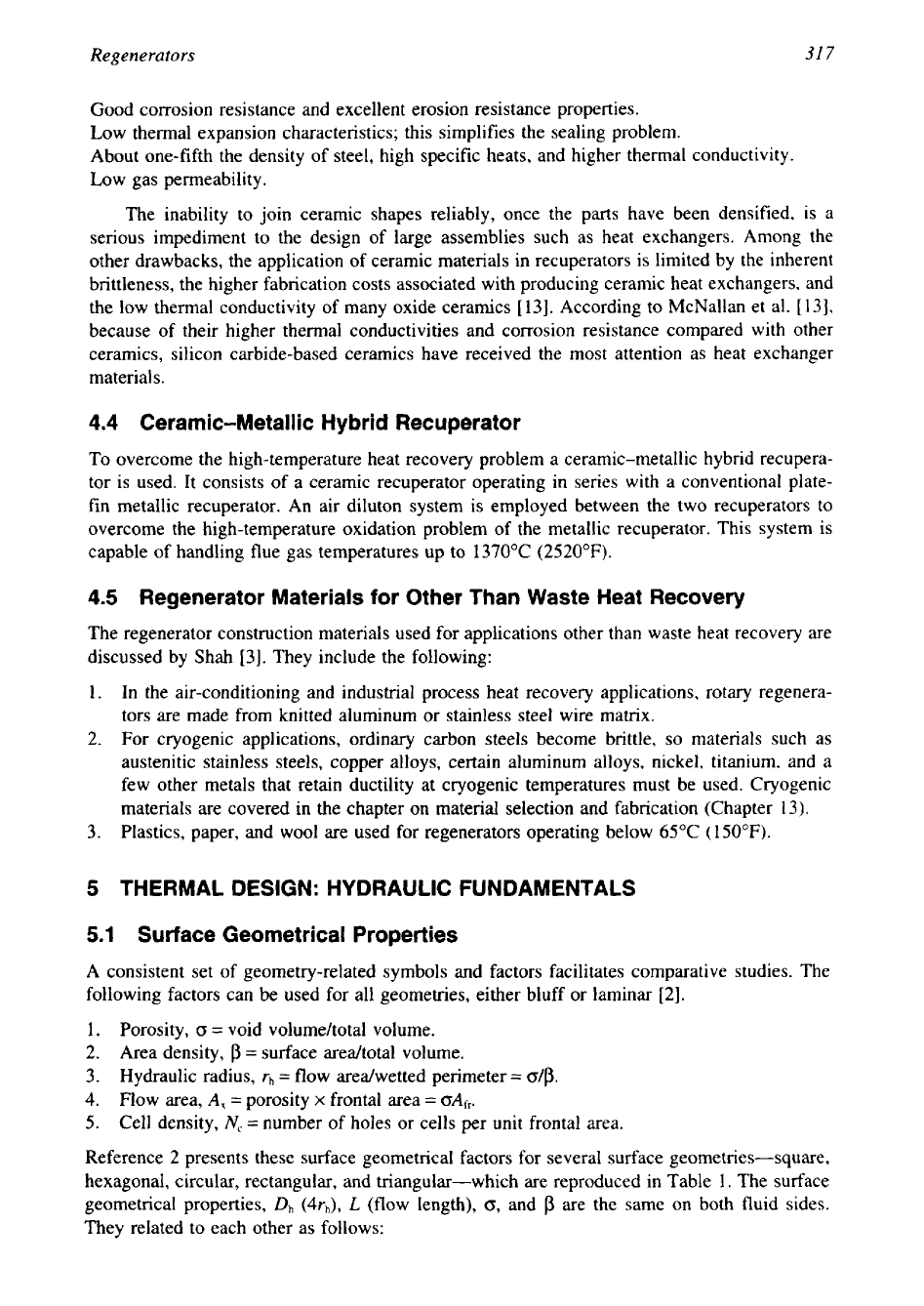
Regenerators
31
7
Good corrosion resistance and excellent erosion resistance properties.
Low thermal expansion characteristics; this simplifies the sealing problem.
About one-fifth the density
of
steel, high specific heats, and higher thermal conductivity.
Low gas permeability.
The inability to join ceramic shapes reliably, once the parts have been densified, is a
serious impediment to the design of large assemblies such as heat exchangers. Among the
other drawbacks, the application of ceramic materials in recuperators is limited by the inherent
brittleness, the higher fabrication costs associated with producing ceramic heat exchangers, and
the low thermal conductivity of many oxide ceramics [13]. According to McNallan et al. [13],
because of their higher thermal conductivities and corrosion resistance compared with other
ceramics, silicon carbide-based ceramics have received the most attention as heat exchanger
materials.
4.4
Ceramic-Metallic Hybrid Recuperator
To overcome the high-temperature heat recovery problem a ceramic-metallic hybrid recupera-
tor is used. It consists
of
a ceramic recuperator operating in series with a conventional plate-
fin metallic recuperator. An air diluton system is employed between the two recuperators to
overcome the high-temperature oxidation problem of the metallic recuperator. This system is
capable of handling flue gas temperatures up to
1370°C
(2520°F).
4.5
Regenerator Materials for Other Than Waste Heat Recovery
The regenerator construction materials used for applications other than waste heat recovery are
discussed by Shah [3]. They include the following:
1. In the air-conditioning and industrial process heat recovery applications, rotary regenera-
tors are made from knitted aluminum or stainless steel wire matrix.
2.
For cryogenic applications, ordinary carbon steels become brittle,
so
materials such as
austenitic stainless steels, copper alloys, certain aluminum alloys, nickel, titanium. and a
few other metals that retain ductility at cryogenic temperatures must be used. Cryogenic
materials are covered in the chapter
on
material selection and fabrication (Chapter 13).
3.
Plastics, paper, and wool are used for regenerators operating below 65°C (150°F).
5
THERMAL DESIGN: HYDRAULIC FUNDAMENTALS
5.1
Surface Geometrical Properties
A consistent set of geometry-related symbols
and
factors facilitates comparative studies. The
following factors can be used for all geometries, either bluff or laminar [2].
1.
Porosity,
o
=
void volume/total volume.
2.
Area density,
p
=
surface aredtotal volume.
3.
Hydraulic radius,
rh
=
flow aredwetted perimeter
=
o/p.
4.
Flow area,
A,
=
porosity
x
frontal area
=
oAfr.
5.
Cell density,
N,
=
number of holes or cells per unit frontal area.
Reference 2 presents these surface geometrical factors for several surface geometries-square,
hexagonal, circular, rectangular, and triangular-which are reproduced in Table
1.
The surface
geometrical properties, Dh (4rh),
L
(flow length),
0,
and
p
are the same on both fluid sides.
They related to each other as follows: